濺射靶材是電子信息產(chǎn)業(yè)的關(guān)鍵原材料之一,其產(chǎn)品質(zhì)量關(guān)系到濺射薄膜的品質(zhì)和濺射設(shè)備的安全。濺射靶材種類繁多l(xiāng)1 ]。從材質(zhì)來說,包括鋁及鋁合金、銅及銅合金、鎳及鎳合金、鉻、鉬、鈦、鎢及鎢合金、金、銀、鉑、鉭、硅、二氧化硅、氧化銦錫、二氧化錫、鐵基合金和稀土等。從靶材原始坯料的制造方法來分,主要有熔鑄靶和粉末靶;從有無背板的角度來分,主要是焊接靶和單體靶。熔鑄靶材的制造流程一般包括以下四步:化學(xué)提純制備高純?cè)牧?、熔煉鑄造制備鑄坯、塑性加工(鍛造、擠壓和軋制)與熱處理、最后是機(jī)械加工。難熔金屬靶材、熔點(diǎn)相差很大的金屬合金靶材和陶瓷靶材坯料一般采用粉末法制備坯料。其關(guān)鍵制造流程是:制粉、粉末冶金制坯或直接噴涂成型、對(duì)坯料進(jìn)行切割、機(jī)械加工成品。上述兩大靶坯制造流程中,除提純、制粉和機(jī)械加工外的其他制造工序都是容易產(chǎn)生內(nèi)部缺陷的高風(fēng)險(xiǎn)工藝。靶材內(nèi)部缺陷的存在將會(huì)在濺射過程中產(chǎn)生顆?;蝻w濺,從而降低薄膜質(zhì)量。對(duì)于焊接靶材,焊接質(zhì)量關(guān)系到濺射靶材與背板之間的焊接強(qiáng)度和濺射過程中靶材散熱,無論是對(duì)于濺射設(shè)備安全還是濺射薄膜質(zhì)量,焊接質(zhì)量都是衡量濺射靶材質(zhì)量是否合格的關(guān)鍵指標(biāo)之一。因此,在濺射靶材的制造過程中采用無損檢測(cè)技術(shù)成為確保制備合格濺射靶材的必要措施。
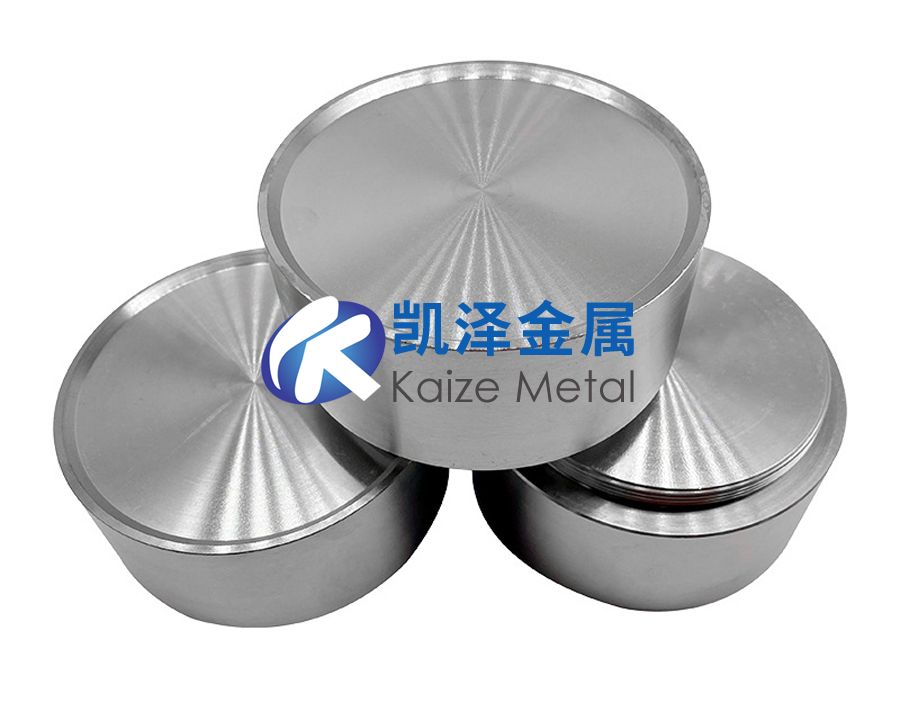
1、鑄坯與粉末冶金坯料的檢驗(yàn)
靶材制造用鑄坯中的缺陷包括氣孔、夾渣、疏松和裂紋等,多是體積型缺陷。對(duì)于鋁及鋁合金靶材來說,還存在氧化鋁顆粒的檢測(cè)問題。如果帶有缺陷的鑄坯進(jìn)入制造流程中,最終的靶材可能完全不合格。因此在下料前必須對(duì)鑄錠進(jìn)行內(nèi)部缺陷檢驗(yàn)。X射線檢測(cè)技術(shù)和超聲波檢測(cè)技術(shù)都可以進(jìn)行材料內(nèi)部缺陷檢驗(yàn),但其適用性取決于鑄坯的材質(zhì)。
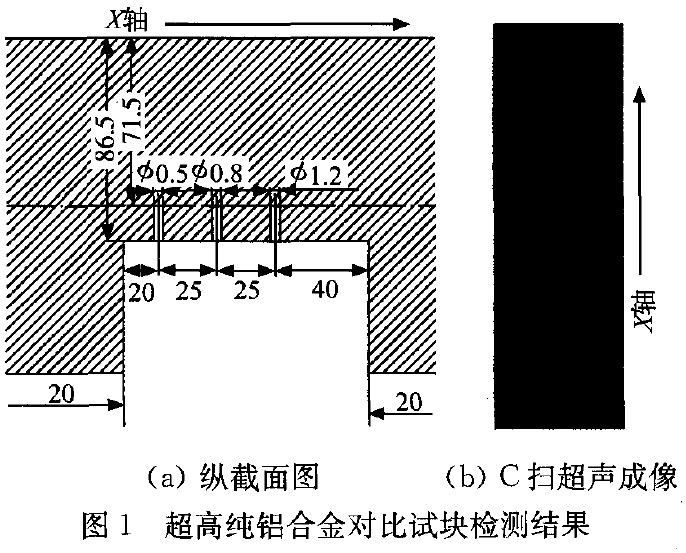
試驗(yàn)發(fā)現(xiàn),超聲波在超高純鋁及合金(>5N,99.999wt %)鑄坯中傳播時(shí),衰減較小,也不存在由于晶粒粗大導(dǎo)致的晶界散射現(xiàn)象 。圖1所示為設(shè)計(jì)的鋁合金鑄坯對(duì)比試塊軸向截面圖和超聲C掃圖像,檢測(cè)頻率為10 MHz,探頭晶片直徑0.375×25.4 mm,探頭焦距為4×25.4 mm??梢钥闯?,水浸C掃超聲波技術(shù)可以有效滿足鋁及鋁合金鑄錠內(nèi) 0.5 mm平底孔當(dāng)量的缺陷檢測(cè)要求。檢驗(yàn)質(zhì)量驗(yàn)收標(biāo)準(zhǔn)如表1所示。
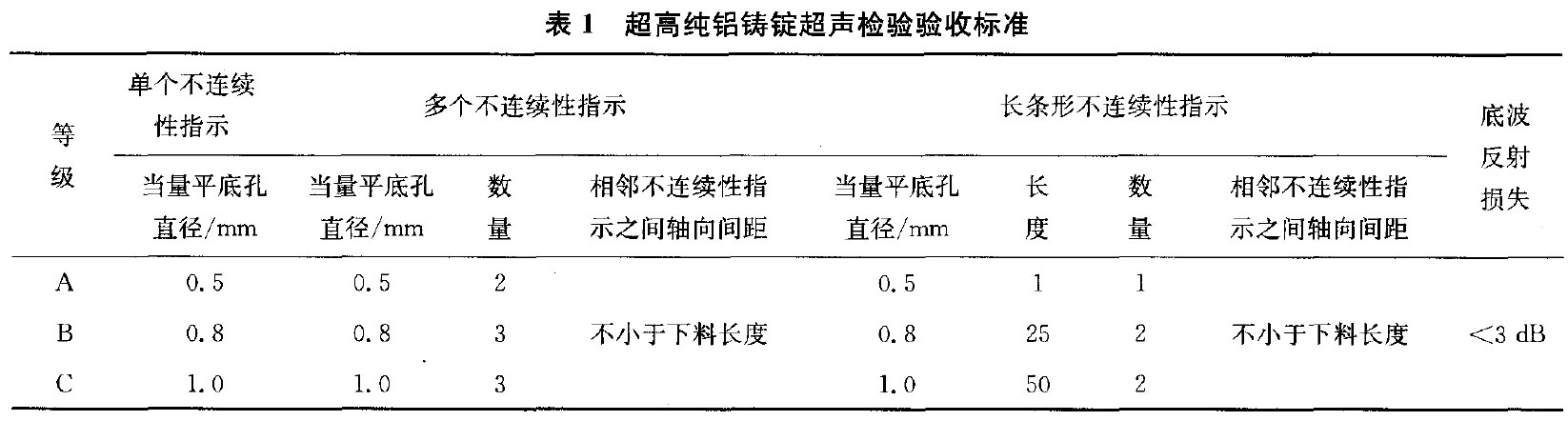
超高純銅(≥6 N)鑄坯和超高純鎳(≥5 N)鑄坯的晶粒尺寸巨大,都是厘米量級(jí),主要是因?yàn)殍T造過程中缺少型核質(zhì)心導(dǎo)致過低的形核率而造成的。
通過對(duì)兩者的鑄坯進(jìn)行超聲波檢驗(yàn)發(fā)現(xiàn),兩者都不適合采用超聲波檢驗(yàn)技術(shù)進(jìn)行內(nèi)部缺陷檢驗(yàn),但其原因卻完全不同。
超聲波在超高純銅中傳播時(shí)存在兩個(gè)問題:一是衰減嚴(yán)重;二是晶體取向的影響。首先,采用USN60超聲探傷儀和5 MHz縱波直探頭,以82 dB的增益檢驗(yàn)上下表面平行的150 mm厚鑄錠(表面粗糙度<1.6μm)時(shí),只能觀察到一次底波且波幅不超過滿屏的10%,表明超聲波衰減嚴(yán)重,無法對(duì)鑄錠進(jìn)行有效檢測(cè)。其次,在利用水浸C掃描技術(shù)采用2.25 MHz 4×25.4 mm焦距探頭對(duì)75 mm厚高純銅鑄錠進(jìn)行檢測(cè)時(shí)發(fā)現(xiàn),檢測(cè)入射面不同區(qū)域的底波顯示的厚度與實(shí)際厚度存在較大差別,如圖2所示。不同區(qū)域的C掃測(cè)量厚度的差異表明不同區(qū)域之間的聲速存在差別,與標(biāo)準(zhǔn)聲速相比最大可以增大約24.56 。這種現(xiàn)象主要是由于鑄錠內(nèi)晶粒尺寸的巨大引起的。超聲波在介質(zhì)中傳播的聲速與介質(zhì)的彈性模量E有關(guān)。對(duì)于晶粒細(xì)小的多晶材料,由于晶體取向是隨機(jī)的,因此材料整體表現(xiàn)為各向同性,其彈性模量也是各向同性,超聲波在其中傳播的聲速也各向相等。但對(duì)于單晶材料,其彈性模量與晶體取向有關(guān)。超聲波在晶粒粗大的超高純銅鑄錠中傳播時(shí),實(shí)質(zhì)是在不同晶粒內(nèi)的傳播。各個(gè)晶粒的取向都存在差異,由此導(dǎo)致了各區(qū)域聲速的不同。這種晶體取向?qū)е侣曀俚牟町悶槔贸暡z測(cè)超高純銅鑄錠內(nèi)部缺陷增加了新的困難。
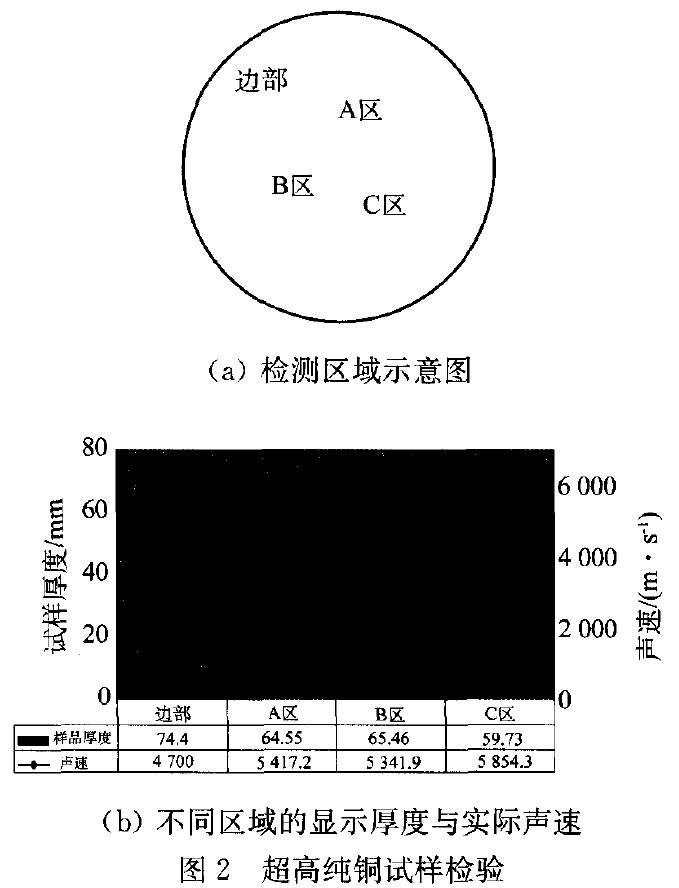
與超高純銅鑄錠明顯不同,超聲波在高純鎳中的衰減并不明顯,其主要問題是粗大晶粒導(dǎo)致的晶界散射。將高純鎳鑄錠切割成薄片,表面處理后粗糙度<1.6μm。然后分別采用x射線檢測(cè)技術(shù)和超聲波檢測(cè)技術(shù)對(duì)該切片進(jìn)行檢測(cè)。對(duì)比發(fā)現(xiàn)兩種方法的檢驗(yàn)結(jié)果并不相符,X射線判定切片中無缺陷的區(qū)域,超聲波檢驗(yàn)時(shí)判定存在缺陷。經(jīng)解剖并逐層磨制觀察,確認(rèn)這些區(qū)域不存在缺陷,而是晶界,如圖3所示。說明超純鎳鑄錠中晶界散射對(duì)超聲波檢驗(yàn)存在嚴(yán)重干擾而無法進(jìn)行有效判定。綜上所述,對(duì)于高純銅和高純鎳鑄錠的內(nèi)部缺陷,超聲波檢測(cè)存在局限,x射線技術(shù)更適用。
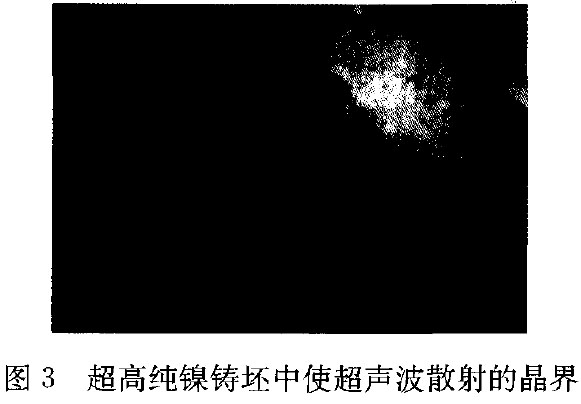
粉末法制備的靶材坯料一般超聲波聲學(xué)特征較好,且晶粒尺寸細(xì)小,因此,多數(shù)可以適用于超聲波檢測(cè)技術(shù)。
粉末法制備的坯料,無論是粉末冶金法還是噴涂法,其內(nèi)部缺陷主要包括裂紋、空洞、夾雜和不致密。與鑄錠內(nèi)的球形或長條形空洞不同,粉末法坯料中的空洞和夾雜主要是不規(guī)則形狀,其形狀與夾雜物的形狀相同。因此,空洞、夾雜和裂紋在粉末坯料中可以任意方向,必須從多個(gè)角度進(jìn)行檢測(cè)才能確保無遺漏。對(duì)于不致密則主要是觀察底波損失來判定。一般如果某區(qū)域底波損失超過4dB,即可判定該區(qū)域不致密。
2、塑性加工靶坯的檢驗(yàn)
除少數(shù)鑄造靶材和直接噴涂成型靶材外,大多數(shù)靶材都是通過一系列塑性加工和熱處理制成。塑、性加工方法包括熱鍛、冷鍛、熱軋制、冷軋制、模壓、擠壓和拉伸等。熱處理包括固溶處理、正火、退火、淬火和時(shí)效等。理論上每個(gè)工序后都應(yīng)該進(jìn)行檢驗(yàn),但考慮到生產(chǎn)效率,一般在加工完成后對(duì)最終的靶材板坯進(jìn)行檢驗(yàn)。
經(jīng)過上述工藝加工后,靶材板坯的顯微組織得到了顯著細(xì)化,板坯厚度為3~40 mm之間,超聲波聲學(xué)特征良好。在上述加工過程中,靶材板坯內(nèi)可能形成的缺陷包括裂紋、分層、夾雜、折疊、過熱、晶粒粗大、過燒、白點(diǎn)和疏松等。除裂紋外,這些缺陷有個(gè)共同的特征,即呈線性平面形狀,方向沿塑性加工的流線方向,且與塑性加工平面平行。顯然,超聲波檢測(cè)技術(shù)對(duì)此類特征的缺陷最為靈敏。因此靶材內(nèi)部缺陷的檢驗(yàn)與評(píng)判一般都采用超聲縱波脈沖反射式水浸C掃檢測(cè)技術(shù)。檢測(cè)時(shí)一般將超聲波焦點(diǎn)聚焦到靶坯厚度的中間位置。
評(píng)判驗(yàn)收標(biāo)準(zhǔn)與靶材的應(yīng)用等級(jí)有關(guān)。根據(jù)驗(yàn)收要求設(shè)計(jì)加工人工平底孔對(duì)比試塊即可。表2列出了當(dāng)前通用的靶材坯料內(nèi)部驗(yàn)收標(biāo)準(zhǔn)。
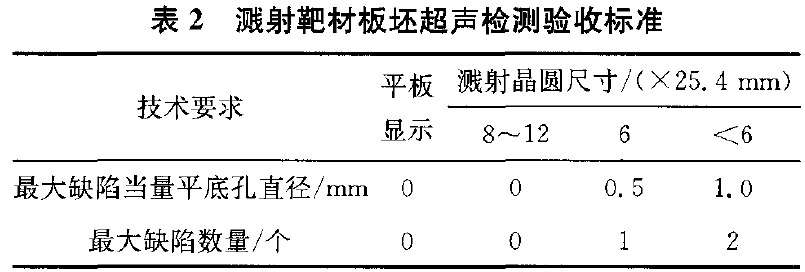
3、焊接質(zhì)量檢驗(yàn)
出于降低成本和增強(qiáng)板材組件強(qiáng)度和導(dǎo)熱性能要求,多數(shù)濺射靶材采用了與冷卻背板焊接的形式,尤其是大尺寸靶材。濺射靶材的背板一般采用鋁合金、銅合金、鉬或者不銹鋼等,其構(gòu)型有的簡(jiǎn)單,只是一塊具有一定硬度、強(qiáng)度和厚度的圓形或者矩形板材;有的構(gòu)型復(fù)雜,內(nèi)部帶有復(fù)雜的冷卻水道。
濺射靶材與背板的焊接是在對(duì)濺射靶材板坯完成機(jī)械加工后進(jìn)行,使用的焊接技術(shù)包括釬焊、電子束焊、擴(kuò)散焊和爆炸焊等。
真空電子束焊接形成的焊縫中可能存在的缺陷有裂紋、空洞、夾雜、未熔合和未焊透等。根據(jù)使用環(huán)境的技術(shù)要求來確定針對(duì)真空電子束焊接質(zhì)量的檢驗(yàn)方法。
釬焊、擴(kuò)散焊和爆炸焊應(yīng)用于靶材時(shí),焊接方式基本都是兩個(gè)平面之間的焊接。釬焊是采用中間材料將兩工件進(jìn)行粘接的連接方式,中間材料(即釬焊焊料)包括銦和錫基焊料等低溫焊料。存在的焊接缺陷主要是未粘接和夾雜。
擴(kuò)散焊過程較為復(fù)雜,焊接面還要進(jìn)行特殊處理,如噴砂毛化或者車齒。毛化或者車齒后的焊接界面本身就存在著缺陷——微小尺寸的裂隙,一般為百微米量級(jí)。因此擴(kuò)散焊檢測(cè)的主要是尺度較大的,如毫米量級(jí)的未焊合。爆炸焊和擴(kuò)散焊相似。
無論是釬焊、擴(kuò)散焊還是爆炸焊,其焊接缺陷具有共同的特征,即線狀平面型缺陷。因此主要采用超聲縱波C掃描技術(shù)進(jìn)行檢驗(yàn)和評(píng)判。
焊接檢驗(yàn)用對(duì)比試塊的設(shè)計(jì)與加工技術(shù)要求可以參考ASTM F1512標(biāo)準(zhǔn)。對(duì)于釬焊來說,一般選擇10 MHz的水浸聚焦探頭進(jìn)行檢驗(yàn)。而對(duì)于對(duì)擴(kuò)散焊,超聲波頻率的選擇則必須考慮焊接界面特征。另外,釬焊與擴(kuò)散焊的質(zhì)量驗(yàn)收標(biāo)準(zhǔn)也存在差別。
表3列出了釬焊和擴(kuò)散焊焊接質(zhì)量的驗(yàn)收標(biāo)準(zhǔn)。顯然擴(kuò)散焊的驗(yàn)收要高于釬焊。

4、結(jié)語
當(dāng)前X射線檢測(cè)技術(shù)和超聲波檢測(cè)技術(shù)基本可以滿足靶材制造的檢測(cè)要求。除鑄錠原材料外,超聲波檢測(cè)技術(shù)在濺射靶材制造中應(yīng)用得更為廣泛。超聲波檢測(cè)工序的安排要兼顧產(chǎn)品質(zhì)量和生產(chǎn)效率。靶材板坯和焊接質(zhì)量的檢驗(yàn)方法主要是超聲縱波脈沖反射C掃描技術(shù)。濺射工藝的要求導(dǎo)致靶材檢驗(yàn)的驗(yàn)收標(biāo)準(zhǔn)十分嚴(yán)格。
參考文獻(xiàn):
【1】陳建軍,楊慶山,賀豐收.濺射靶材的種類、應(yīng)用、制備及發(fā)展趨勢(shì)【J】.湖南有色金屬,2006,22(04):38—76.
【2】金永中,劉東亮,陳建.濺射靶材的制備及應(yīng)用研究[J].四川理工學(xué)院學(xué)報(bào)(自然科學(xué)版),2005,18(3):22
【3】努力古.濺射靶材的制備及發(fā)展趨勢(shì)【J】.新疆有色金屬,2008(5):55—56.
【4】尚再艷,江軒,李勇軍,等.集成電路制造用濺射靶材【J】.稀有金屬,2005,29(4):475—477.
【5】劉志堅(jiān),陳遠(yuǎn)星,黃偉嘉,等.濺射靶材的應(yīng)用及制備初探[J].南方金屬,2003,135:23—32.
【6】Wickersham C E,Poole Jr J E,Leybovich A,et a1.Measurements of the critical inclusion size for arcingand macroparticle ejection from aluminum sputteringtargetsVJ,1.J Vac Sci Technol A,2001,19(6):2767—2772.
【7】Wickersham C E,Poole Jr J E,F(xiàn)an J S.Arc genera—tion from sputtering plasma-dielectric inclusion interae—tionsVJ].J Vac Sci Technol A,2002,20(3):833—838.
【8】Wickersham C E,Poole Jr J E,F(xiàn)an J S,et a1.Videoanalysis of inclusion induced macroparticle emissionfrom aluminum sputtering targets[J].J Vac Sci Tech—nol A,2001,19(6):2741—2750.
【9】 Gary S Selwyn,Corey A Weiss,F(xiàn)ederico Sequeda,eta1. Particle contamination formation in magnetronsputtering processes[J].J Vac Sci Technol A,1997,15(4):2023— 2028.
【10】Vikram Pavate,Murali Abburi,Sunny Chiang,et a1.Correlation between aluminum alloy sputtering target
metallurgical characteristics[J].Arc initiation and InfilmDefect Density,1997(3214):42— 47.
【11】Paul S Gilman,Alfred Snowman,Andre Desert.De—termination of actual defect size in cathode sputtertargets subjected to ultrasonic inspection: US,
6269699 B1EP].2001.
【12】 Charles E Wickersham,John E Poole,AlexanderLeybovich,et a1.M ethod for determing a critical sizeof an inclusion in aluminum or aluminum alloy sputte—ring target:US,7087142 B2[P].2006.
【13】 Charles E Wlckersham JR,John E Poole,AlexanderLeybovich,et a1.Method for determing a critical sizeof an inclusion in aluminum or aluminum alloy sputte—ring target:US,2004/0118675 AI[P].2004.
【14】Russell B Gore,Ronald H Fleming.Methods of tes—ting sputtering target materials: US, 6439054 B1[-P1.2002.
【15】Charles E Wlckersham JR,John E Poole,AlexanderLeybovich,et a1. Sputter targets and methods ofmanufacturing same to reduce particulate emission
during sputtering:US,2002/0184970 A1I-p].2002.
【16】Hidemasa Tamura,Norio Yokoyama,Eiichi Shimi—ZU,et a1. Sputtering target and production method
thereof:US,6024852[P,1.2000.
【17】陳岳軍,趙海燕,史耀武.粗晶材料超聲檢測(cè)缺陷信號(hào)增強(qiáng)的小波分析法[J].中國有色金屬學(xué)報(bào),1997,7(2):94— 96.
相關(guān)鏈接