引言
物理氣相沉積技術(shù)(PhysicalVaporDeposition,PVD),具有相對(duì)較低的工藝溫度,沉積過(guò)程便于控制,制備出的涂層性能優(yōu)異(均勻性高、殘余應(yīng)力小)和易于工業(yè)化應(yīng)用等優(yōu)點(diǎn),在耐腐蝕涂層、超硬涂層、光學(xué)涂層、耐摩擦涂層以及復(fù)合多層涂層的制備等領(lǐng)域都得到廣泛的應(yīng)用[1-6],因此越來(lái)越受到研究者的關(guān)注[7]。PVD技術(shù)主要包括蒸鍍技術(shù)、陰極電弧離子鍍技術(shù)和磁控濺射技術(shù)。其中陰極電弧離子鍍技術(shù)具有沉積速率高以及靶材粒子離化率高的優(yōu)勢(shì),但在加工過(guò)程中不可避免地會(huì)產(chǎn)生金屬液滴,影響了涂層的致密程度[8]。蒸鍍技術(shù)的優(yōu)勢(shì)在于加工成本低,制備出的涂層純度較高,但其缺點(diǎn)在于加工過(guò)程中粒子能量較低,制備出的涂層與基體結(jié)合較差。相比于以上兩種技術(shù),磁控濺射技術(shù)由于其加工過(guò)程中粒子能量易于調(diào)控,制備出的涂層致密、均勻性高在現(xiàn)代裝備制造業(yè)中獲得了廣泛的應(yīng)用。
近些年來(lái)磁控濺射技術(shù)發(fā)展迅猛,產(chǎn)生了諸如直流磁控濺射(DCMS)、高功率脈沖磁控濺射技術(shù)(HiPIMS)等新技術(shù),但涂層沉積速率較低[9-11]制約了磁控濺射規(guī)?;瘧?yīng)用。例如,采用DCMS技術(shù)沉積金屬涂層的速率約為10nm/s[12],對(duì)于復(fù)合成分涂層,尤其是氧化物涂層,其沉積速率甚至更低[13-15]。由于磁控濺射過(guò)程中靶材表面的濺射是產(chǎn)生涂層粒子的主要機(jī)制,且濺射強(qiáng)度與放電功率成正比,放電功率受到電源、磁場(chǎng)強(qiáng)度和冷卻系統(tǒng)等設(shè)備本身的限制,僅依靠提高放電功率來(lái)提升涂層沉積速率,其效果非常有限。
最近的研究表明,當(dāng)靶材表面[16–22]上發(fā)生濺射作用時(shí),還出現(xiàn)了蒸發(fā)或升華,涂層的沉積速率可能會(huì)顯著增加1~2個(gè)數(shù)量級(jí)。與濺射作用不同,只有在靶材表面溫度極高的情況下,才會(huì)出現(xiàn)靶材原子的蒸發(fā)或升華。靶材蒸發(fā)速率隨著溫度的升高而幾乎呈指數(shù)增長(zhǎng),從這個(gè)角度看,如果能夠?yàn)R射液態(tài)靶材,磁控濺射的涂層沉積速率將獲得極大提高。液態(tài)靶材磁控濺射技術(shù)由Danilin等[23]最早提出,該技術(shù)一經(jīng)報(bào)道,就受到國(guó)內(nèi)外學(xué)者和工業(yè)界的廣泛關(guān)注。
由于先進(jìn)裝備制造業(yè)、航空航天、半導(dǎo)體行業(yè)對(duì)高性能涂層的迫切需求,液態(tài)靶材磁控濺射技術(shù)具有提高涂層沉積速率以及提升能量利用效率的突出優(yōu)勢(shì),使其有望成為涂層制備主流技術(shù)。國(guó)內(nèi)外學(xué)者對(duì)液態(tài)靶材磁控濺射技術(shù)仍處于探索研究階段,因此本文總結(jié)國(guó)內(nèi)外近年來(lái)對(duì)該技術(shù)的研究成果,并對(duì)該項(xiàng)技術(shù)未來(lái)的發(fā)展趨勢(shì)進(jìn)行討論與展望。
1、液態(tài)靶材磁控濺射技術(shù)特點(diǎn)及優(yōu)勢(shì)
1.1 液態(tài)靶材磁控濺射技術(shù)原理
液態(tài)靶材磁控濺射放電裝置主要由真空系統(tǒng)、供氣系統(tǒng)、磁控系統(tǒng)、冷卻系統(tǒng)、電源及其調(diào)制系統(tǒng)組成,與傳統(tǒng)磁控濺射放電裝置相類似,如圖1所示[24]。但在液態(tài)靶材磁控濺射系統(tǒng)中,靶材需要被放置在坩堝中,同時(shí)調(diào)整坩堝與冷卻系統(tǒng)的間距,使靶材在涂層制備過(guò)程中始終保持熔化狀態(tài)。在放電開(kāi)始時(shí),靶材一般是未熔化的,通過(guò)調(diào)整放電功率,靶材在等離子體轟擊作用下逐漸被加熱至熔化狀態(tài)。在靶材熔化后,通過(guò)調(diào)整放電參數(shù)來(lái)進(jìn)行所需涂層的沉積。
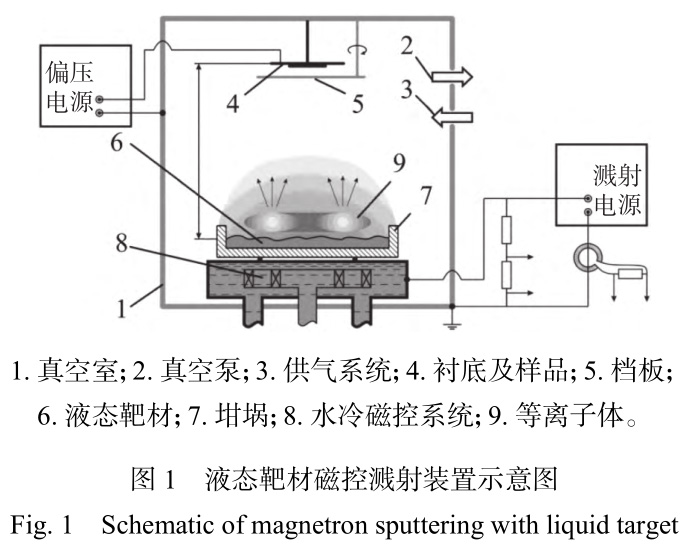
1.2 液態(tài)靶材磁控濺射放電伏安特性
研究液態(tài)靶材放電(MLT)的伏安特性曲線,對(duì)于深入理解放電機(jī)制、進(jìn)一步探索粒子的傳輸機(jī)制,對(duì)后期在涂層制備過(guò)程中具體工藝參數(shù)的選擇具有重要的指導(dǎo)意義。關(guān)于液態(tài)靶材放電特性,目前學(xué)界普遍認(rèn)為是由于高溫下劇烈的熱電子發(fā)射導(dǎo)致液態(tài)靶材的放電電流顯著增高,放電電壓相比于固態(tài)靶材有明顯的降低。
Shapovalov等[25]研究了在純氬氣氛中Ti靶在高溫條件下直流磁控濺射過(guò)程的放電特性變化趨勢(shì),如圖2(a)所示,隨著放電電流升高,放電電壓呈現(xiàn)出先增大后減小的趨勢(shì),并且在電流為3A時(shí),放電電壓出現(xiàn)最大值。呈現(xiàn)這種變化趨勢(shì)的主要原因是在第一個(gè)階段放電電流主要由離子電流(I+)及二次電子電流(γI+)組成,因此放電電壓隨放電電流增高而增大。當(dāng)電流增大至3A后,由于此前熱量的積累,靶材表面溫度顯著升高,因此熱電子發(fā)射十分劇烈并主導(dǎo)了放電過(guò)程,熱電子電流(ITe)不斷增大,放電電壓因此降低。圖2(b)給出了放電總電流與離子-二次電子電流之間的變化關(guān)系,其中α如式(1)所示:
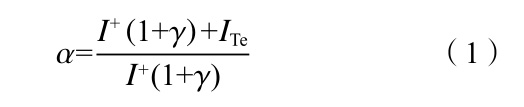
式中:α為放電總電流與離子-二次電子電流的比值。
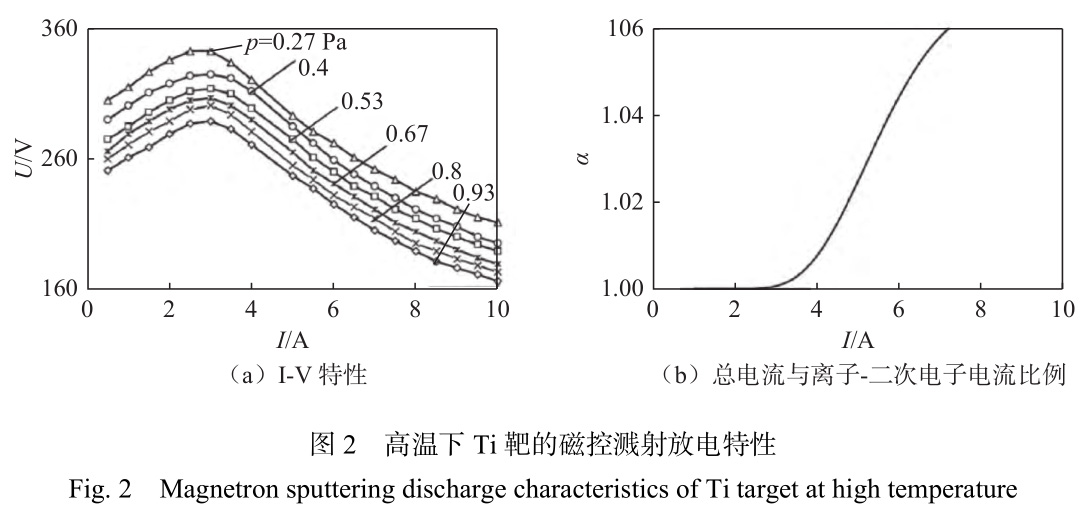
可見(jiàn)當(dāng)放電電流大于3A后,靶表面溫度升高而引發(fā)的熱電子發(fā)射十分顯著。Shapovalov等[26]還研究了熱Ti靶與冷Ti靶在純氬氣氛中放電伏安特性的異同,如圖3所示。在電流密度j小于75mA/cm2時(shí),二者沒(méi)有明顯差異,但當(dāng)電流密度大于75mA/cm2時(shí),熱Ti靶的放電電壓顯著降低,但冷Ti靶的放電電壓仍然隨電流密度的升高而增大。這說(shuō)明在強(qiáng)制冷卻條件下的Ti靶熱電子電流發(fā)射效應(yīng)不明顯,只有靶表面處于高溫狀態(tài)下才會(huì)有劇烈的熱電子發(fā)射。Zhukov等[27]對(duì)在純氬氣氛中Al靶從固態(tài)到液態(tài)的直流磁控濺射放電過(guò)程進(jìn)行了研究,檢測(cè)了放電電流、電壓及坩堝溫度隨時(shí)間的變化趨勢(shì),如圖4所示,放電過(guò)程中直流電源設(shè)置為恒功率模式運(yùn)行。研究結(jié)果表明,隨靶材溫度上升,放電電流逐漸增大,放電電壓先增高后降低并在靶材完全熔化后保持穩(wěn)定。值得注意的是,在靶材完全熔化后,放電電流相比于固態(tài)時(shí)增大了一倍,這主要是液態(tài)靶材蒸發(fā)出的金屬原子進(jìn)一步電離以及熱電子發(fā)射的增加所造成的。
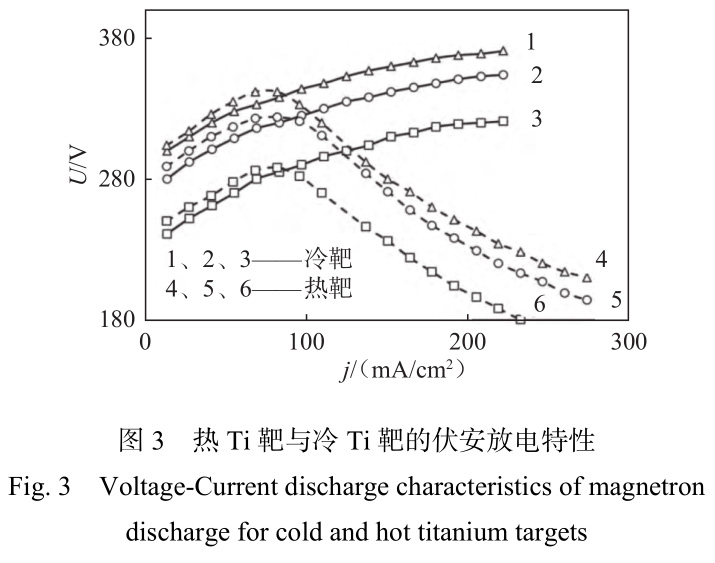
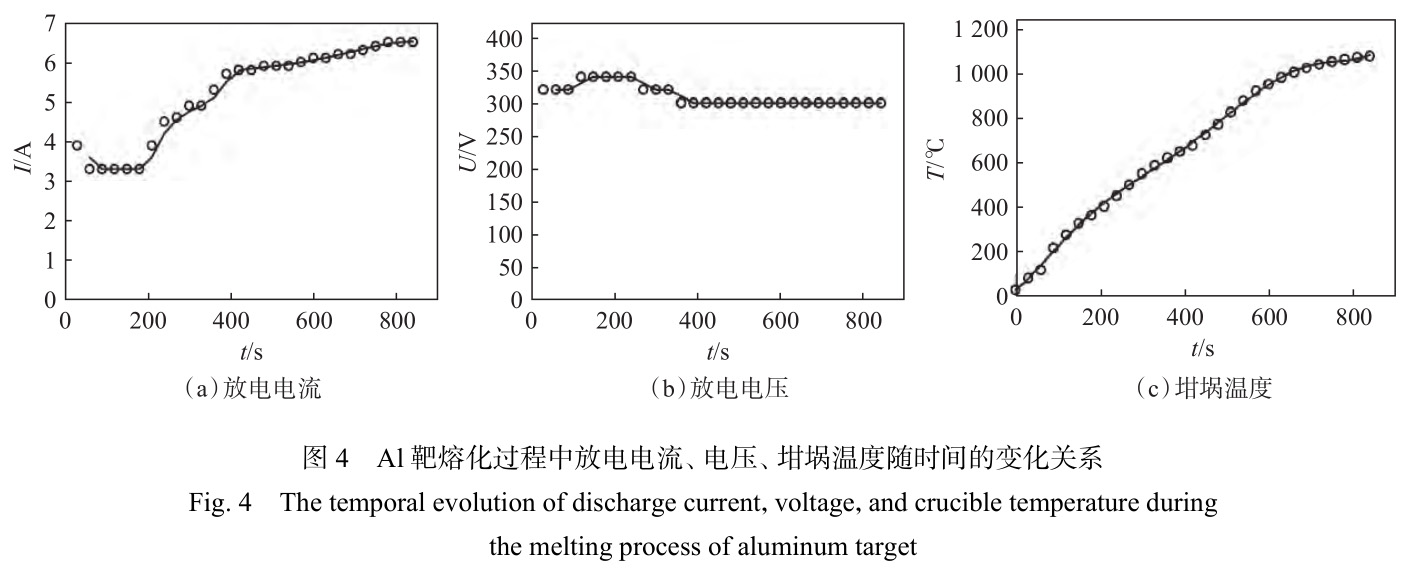
1.3 液態(tài)靶材磁控濺射放電等離子體特性
涂層沉積速率主要取決于放電等離子體中靶材粒子的密度,因此研究MLT放電過(guò)程中的等離子體特性可以為調(diào)控涂層的沉積速率及質(zhì)量提供理論指導(dǎo),并有助于深入理解液態(tài)靶材的放電機(jī)理。Kolodko等[28]利用質(zhì)譜儀探究了液態(tài)Cu靶在直流磁控濺射放電過(guò)程中襯底附近的離子通量,檢測(cè)結(jié)果如圖5所示。結(jié)果表明,液態(tài)Cu靶在放電過(guò)程中,即使沒(méi)有工作氣體的參與,也能處于一種獨(dú)特的“無(wú)氣自濺射”狀態(tài),在等離子體質(zhì)譜分析中,未檢測(cè)到Ar粒子的存在,而固態(tài)Cu靶的放電過(guò)程則必須依賴于工作氣體粒子(Ar+和Ar2+)的參與。另外,液態(tài)Cu靶在“無(wú)氣自濺射”放電模式中所展現(xiàn)出的獨(dú)特性質(zhì),可能會(huì)顯著提高所沉積Cu涂層的純度。因?yàn)樵趥鹘y(tǒng)的固態(tài)靶磁控濺射體系中氣體離子和原子會(huì)從等離子體中進(jìn)入到正在沉積的涂層中,影響沉積涂層的純度。Kaziev等[29]對(duì)放電等離子體的發(fā)射光譜(OES)研究結(jié)果同樣證實(shí)了這點(diǎn),如圖6所示,當(dāng)液態(tài)Cu靶處于無(wú)氣自濺射放電狀態(tài)時(shí),放電等離子體中主要為Cu原子和Cu+離子,工作氣體含量較少。
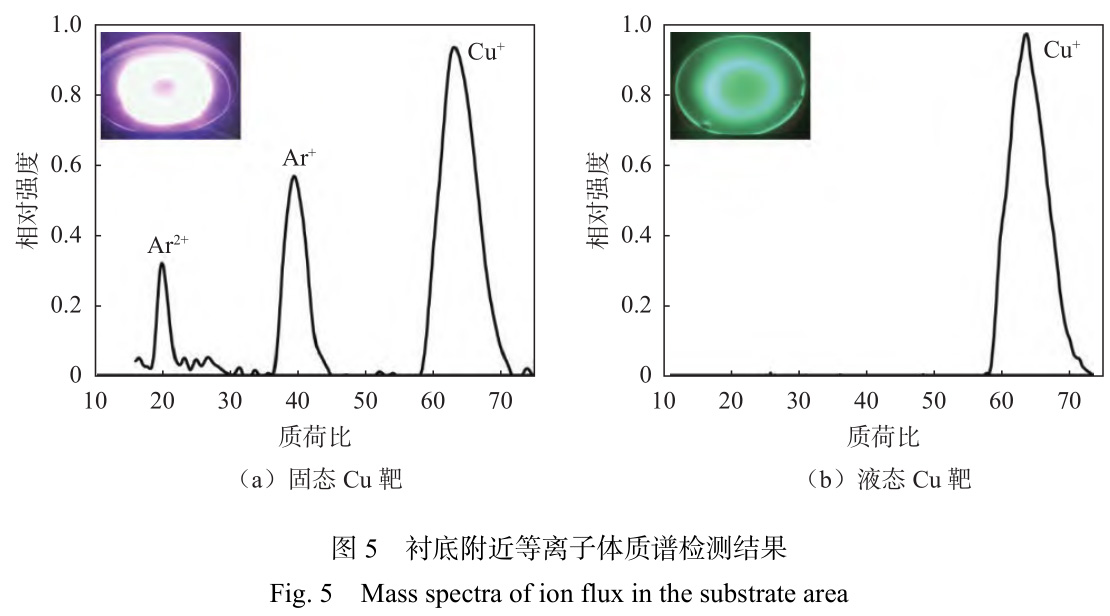
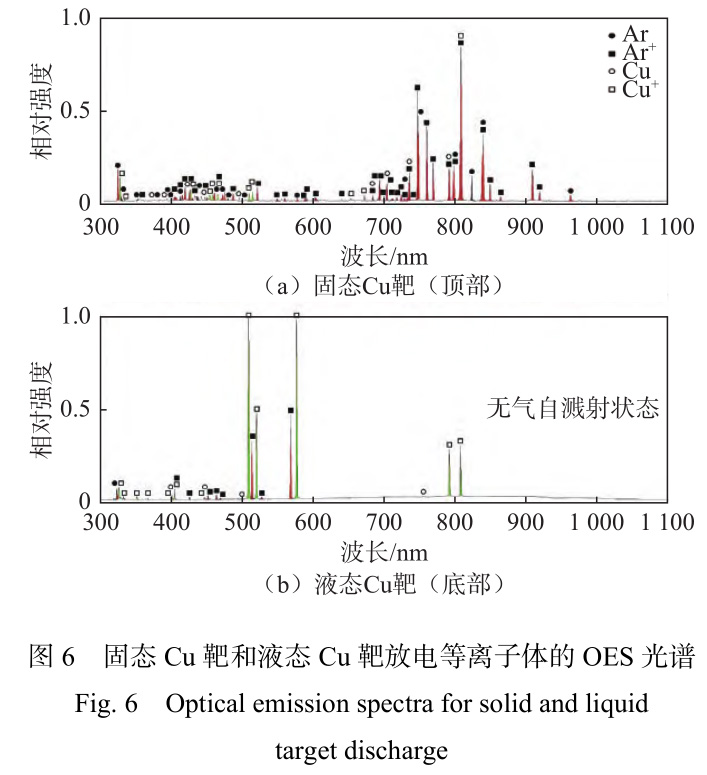
Tumarkin等[30]的研究證實(shí)了在無(wú)工作氣體的情況下,液態(tài)Cu靶可以僅依靠電離自身蒸發(fā)出的原子維持等離子體放電。相比于存在工作氣體的情況下(pAr=1.0Pa),在放電電流密度相同時(shí),液態(tài)Cu靶無(wú)氣自濺射模式(pAr=0Pa)的放電電壓降低了約10%,如圖7(a)所示,這主要是由于金屬原子比氣體原子的電離電位更低。Tumarkin等[30]還研究了液態(tài)Cu靶在脈沖放電條件下(IMLT)等離子體密度和電離度,如圖7(b)所示,等離子體密度和電離度隨放電功率密度增大而逐步增加,電離度在距Cu靶表面5cm處約為60%,呈現(xiàn)出HiPIMS的典型特征。同時(shí)還發(fā)現(xiàn),由于液態(tài)Cu靶蒸發(fā)出的大量金屬原子,使得等離子體強(qiáng)電離區(qū)域膨脹,因此增加放電功率會(huì)使等離子體密度隨距離增加而變化的梯度減小,在P=2800W/cm2時(shí),等離子體密度與靶表面間距呈線性關(guān)系。
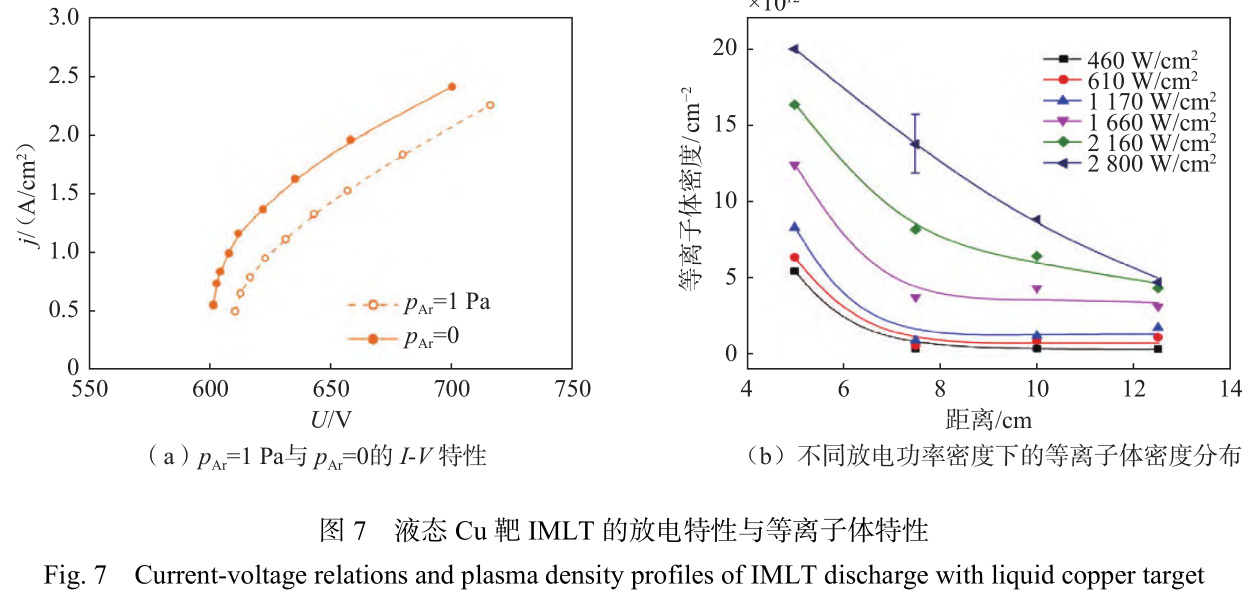
1.4 液態(tài)靶材磁控濺射優(yōu)勢(shì)
近年來(lái),對(duì)MLT技術(shù)的研究表明,其最大的優(yōu)勢(shì)在于能量利用效率高。在沉積純金屬涂層時(shí),相比于固態(tài)靶材,由于蒸發(fā)和濺射的共同作用,液態(tài)靶材的沉積速率可提高10~100倍。Bleykher等[31]研究了Pb靶的放電功率密度與靶表面侵蝕速率的變化趨勢(shì),如圖8所示,當(dāng)放電功率密度較低時(shí),靶表面溫度較低,濺射是影響靶表面侵蝕速率的主要因素,當(dāng)靶表面溫度達(dá)到熔點(diǎn)的1.65倍后,蒸發(fā)導(dǎo)致靶表面侵蝕速率呈指數(shù)增加,取代濺射成為影響靶表面侵蝕速率的主要因素。在蒸發(fā)占主導(dǎo)地位的情況下,沉積過(guò)程粒子流密度由1016atoms/(cm2·s)提升至1018atoms/(cm2·s),涂層沉積速率顯著提高到102~103nm/s,如圖9所示。Bleykher等還計(jì)算了Cr靶和Ti靶沉積速率隨放電功率密度的變化趨勢(shì),研究結(jié)果表明,在較高的放電功率密度下,熱靶表面蒸發(fā)作用十分明顯,與完全冷卻的靶材相比,放置于隔熱鉬坩堝中的Cr靶和Ti靶的沉積速率分別能夠提高20倍和5倍。
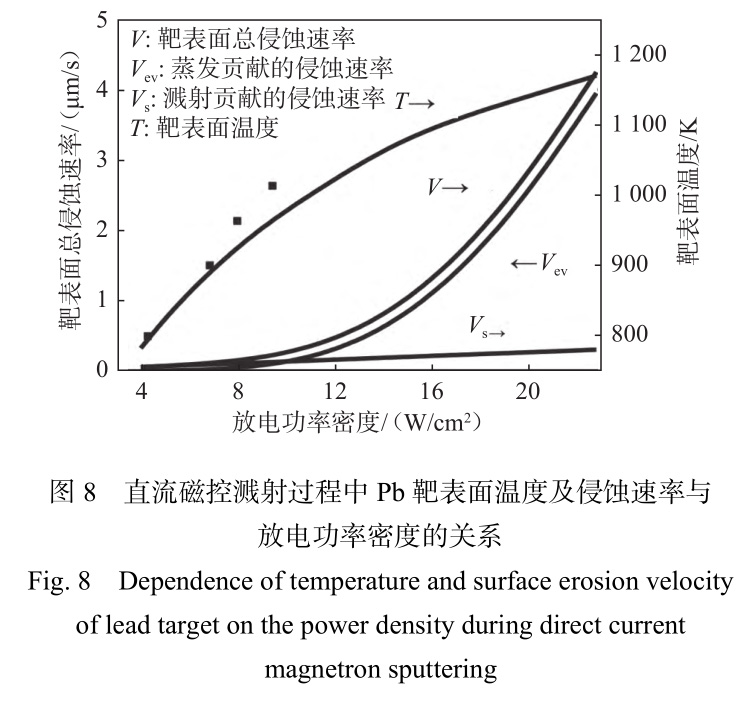
除了具有較高的沉積速率外,液態(tài)靶材磁控濺射過(guò)程中的等離子體密度與離化率也非常高。較高的離化率便于在濺射過(guò)程中調(diào)控涂層結(jié)構(gòu),例如通過(guò)向襯底施加偏壓來(lái)提高金屬離子向基底方向運(yùn)動(dòng)的通量與能量,制備出力學(xué)性能較好的涂層。Tumarkin等[24]在使用液態(tài)Cu靶直流磁控濺射技術(shù)制備純Cu涂層時(shí),分別向襯底施加了?50V、?100V、?300V、?400V的偏壓,沉積了具有不同結(jié)合強(qiáng)度的涂層,沉積涂層的截面形貌如圖10所示。研究發(fā)現(xiàn),通過(guò)提高襯底負(fù)偏壓,可以將涂層與襯底的結(jié)合力大幅提高(襯底偏壓為?400V時(shí),涂層受力達(dá)25N時(shí)仍未觀察到明顯剝落痕跡)。
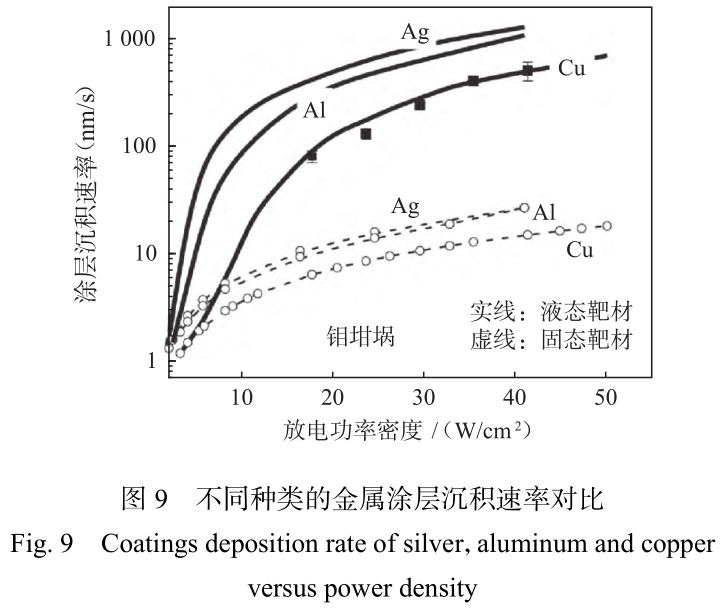
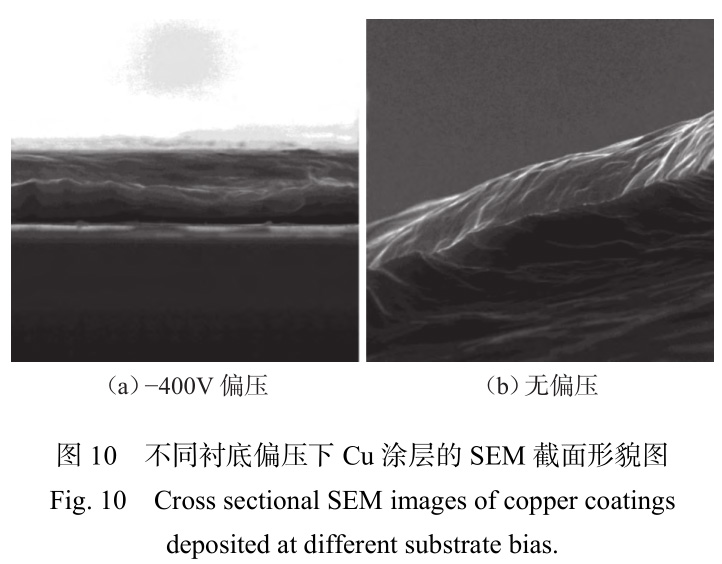
2、液態(tài)靶材磁控濺射技術(shù)在涂層制備中的應(yīng)用
在傳統(tǒng)的固態(tài)靶材磁控濺射過(guò)程中,大都需要向真空室內(nèi)通入工作氣體,并電離工作氣體中的原子用以維持等離子體放電。真空室中工作氣體的壓力的范圍一般為0.1~1Pa[32],濺射出的靶材原子與真空室內(nèi)的工作氣體原子發(fā)生碰撞,降低了靶材原子沉積到基底上的能量,并導(dǎo)致涂層沉積速率的降低。根據(jù)前文所述,液態(tài)靶材在濺射過(guò)程中伴隨著靶材原子的大量蒸發(fā),可以實(shí)現(xiàn)無(wú)氣自濺射模式。許多研究者認(rèn)為,這種模式將為金屬涂層的制備帶來(lái)許多優(yōu)勢(shì)[33-37]。目前利用液態(tài)靶材無(wú)氣自濺射模式來(lái)沉積涂層的研究主要集中在Cu、Cr等材料上。
2.1 Cu涂層
Bleykher等[38]采用液態(tài)Cu靶磁控濺射制備Cu涂層,制備出的Cu涂層相比于濺射固態(tài)Cu靶,結(jié)構(gòu)沒(méi)有明顯差異,但沉積速率高達(dá)140nm/s(濺射固態(tài)Cu靶沉積速率僅為4nm/s),且表面更光滑,平均粗糙度更低,AFM結(jié)果如圖11所示,由于蒸發(fā)而顯著增加的靶材粒子密度對(duì)涂層表面形態(tài)產(chǎn)生了影響。Bleykher等[39]還研究了不同坩堝材質(zhì)對(duì)Cu涂層沉積的影響,SEM下Cu涂層的形貌如圖12所示。圖12中,液態(tài)Cu靶置于石墨坩堝中沉積得到的涂層(a)表面形貌與(b)截面形貌;液態(tài)Cu靶置于鉬坩堝中沉積得到的涂層(c)表面形貌與(d)截面形貌;相比于石墨坩堝,使用鉬坩堝沉積得到的Cu涂層表面顆粒更加細(xì)小均勻,涂層也較為致密,而使用石墨坩堝沉積的Cu涂層表面顆粒較為粗大,孔隙和缺陷較多,具有明顯的柱狀結(jié)構(gòu)。作者認(rèn)為鉬坩堝在濺射過(guò)程中具有更高通量的熱輻射,使得基體溫度升高,表面原子流動(dòng)性增強(qiáng),形成的涂層更為致密。
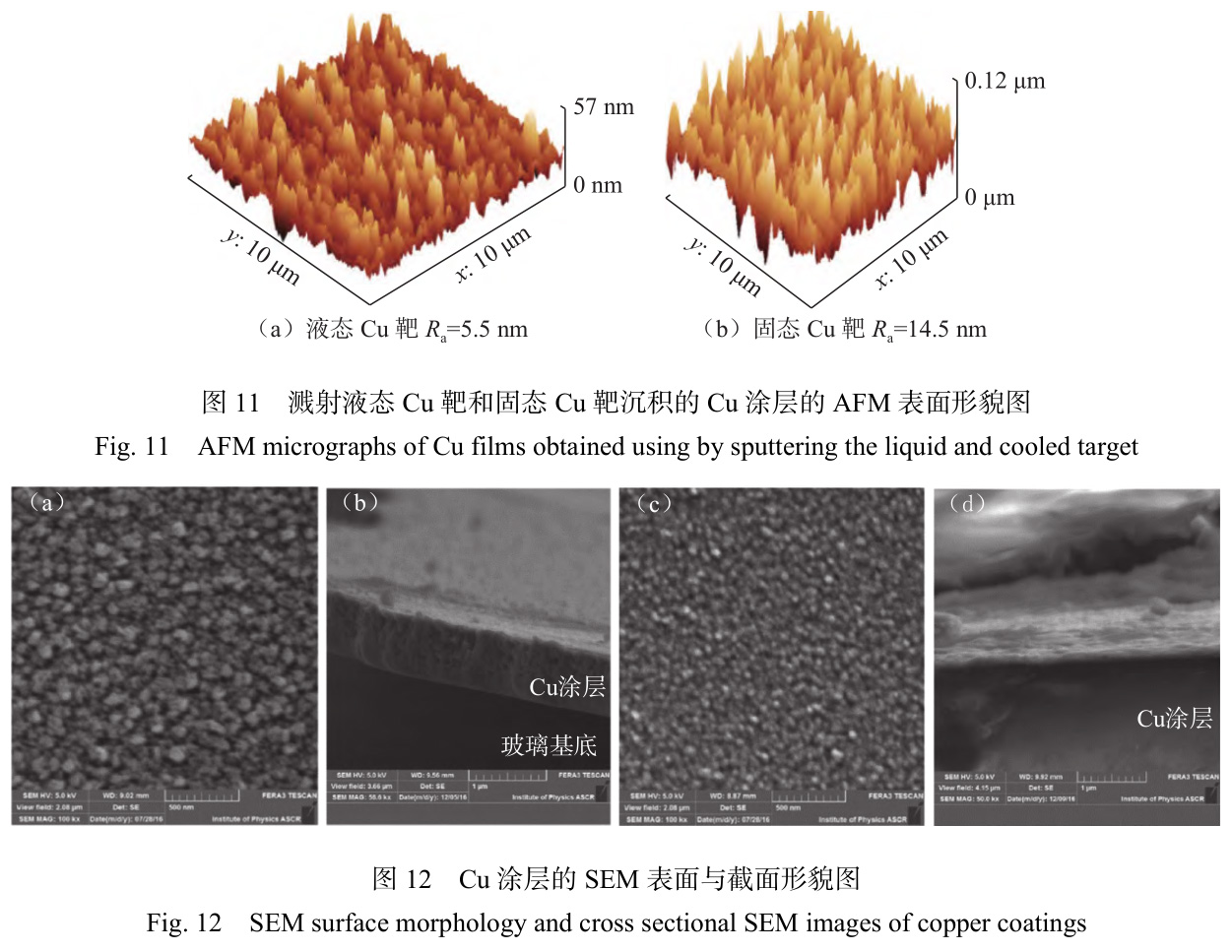
2.2 Cr涂層
Sidelev等[40]通過(guò)采用強(qiáng)制冷卻的固態(tài)Cr靶和熱Cr靶的磁控濺射技術(shù)制備了Cr涂層。研究結(jié)果表明,在放電功率密度相同的條件下,熱靶的沉積速率比固態(tài)靶高出1.5~2倍,并且涂層的結(jié)合力明顯優(yōu)于固態(tài)靶沉積的涂層,劃痕實(shí)驗(yàn)結(jié)果如圖13所示。
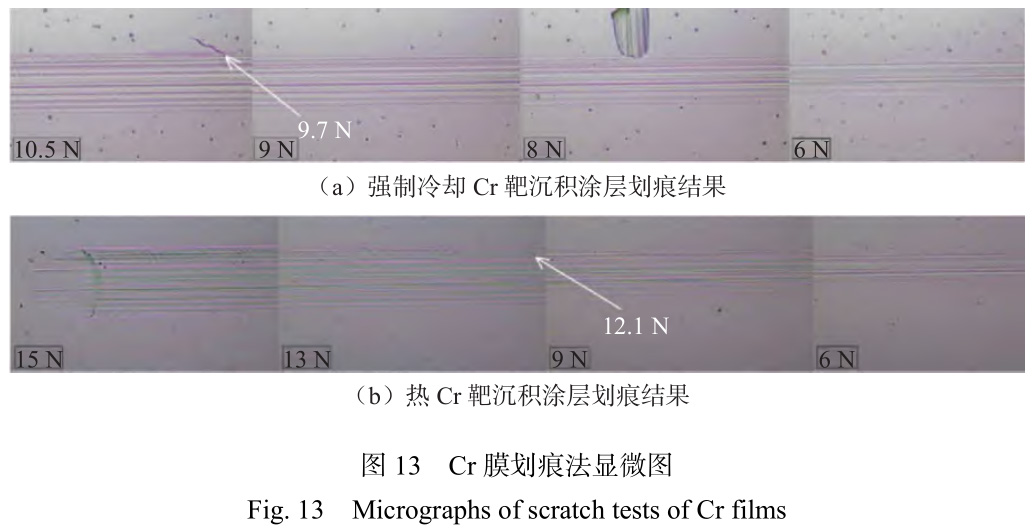
然而,熱靶沉積的涂層硬度相對(duì)較低,約比固態(tài)靶沉積的涂層低9%(固態(tài)靶12GPa降低為熱靶的11GPa)。作者認(rèn)為主要是由于熱靶在沉積過(guò)程中蒸發(fā)的大量Cr原子在基體上產(chǎn)生了熱流,導(dǎo)致了硬度的降低并改善了結(jié)合力。
3、結(jié)語(yǔ)與展望
本文綜述了近年來(lái)液態(tài)靶材磁控濺射技術(shù)(MLT)的研究進(jìn)展,重點(diǎn)探討了MLT放電過(guò)程中的放電特性及等離子體特性,通過(guò)對(duì)比MLT與傳統(tǒng)固態(tài)靶材磁控濺射過(guò)程的技術(shù)特點(diǎn),認(rèn)為MLT技術(shù)將磁控濺射和蒸鍍兩種技術(shù)的優(yōu)點(diǎn)進(jìn)行了融合,從而實(shí)現(xiàn)了極高的能量利用效率,并大幅提高了磁控濺射涂層制備過(guò)程中的沉積速率,以極高的速率沉積了如Cu、Cr等材質(zhì)的純金屬涂層。
但與傳統(tǒng)固態(tài)靶磁控濺射相比,液態(tài)靶材放電等離子體中由蒸發(fā)而產(chǎn)生的原子數(shù)量較多,其動(dòng)能相對(duì)較低,因此存在著離化率損失與涂層力學(xué)性能下降的問(wèn)題,這也是制約MLT技術(shù)發(fā)展的重要因素。另外,在濺射過(guò)程中液態(tài)靶材表面溫度較高,也會(huì)向襯底輻射大量熱量導(dǎo)致襯底升溫,因此無(wú)法使用MLT技術(shù)在對(duì)溫度敏感的不耐溫襯底上沉積涂層。由于MLT技術(shù)的發(fā)展才剛剛起步,現(xiàn)有研究的主要側(cè)重點(diǎn)在于研究液態(tài)靶材放電特性與提高涂層沉積速率,對(duì)上述兩個(gè)問(wèn)題研究較少。因此如何在保證高沉積速率的同時(shí)進(jìn)一步提高放電等離子體中粒子離化率,如何有效利用高溫下靶材表面發(fā)射的熱電子,以及如何進(jìn)一步提高涂層的力學(xué)性能,具有重大的研究?jī)r(jià)值和深遠(yuǎn)的研究前景。
參考文獻(xiàn):
[1] LI C L,WANG L G,SHANG L L,et al. Mechanical and high-temperature tribological properties of CrAlN/TiSiN multilayer coating deposited by PVD[J]. Ceramics Interna-tional,2021,47(20):29285?29294.
[2] PARK G D,YANG J H,LEE K H,et al. Ultra-high corro-sion resistance of Al-Mg-Si film on steel sheet formed by PVD Mg coating and heat treatment[J]. Corrosion Science,2021,192:109829.
[3] KONG D J,F(xiàn)U Y Z,WU Y Z,et al. Interfacial characteris-tics and tribological properties of TiN coatings prepared by PVD method[J]. Journal of Vacuum Science and technology,2012,32:1078?1083.
[4] ENGELHART W,DREHER W,EIBL O,et al. Deposition of [4]alumina thin film by dual magnetron sputtering:Is it γ-Al 2 O 3 ?[J]. Acta Materialia,2011,59(20):7757?7767.
[5]REDDY I N,REDDY V R,SRIDHARA N,et al. Optical and microstructural characterisations of pulsed rf magnetron sput-tered alumina thin film[J]. Journal of Materials Science & Technology,2013,29(10):929?936.
[6] REDDY I N,REDDY V R,SRIDHARA N,et al. Pulsed rf magnetron sputtered alumina thin films[J]. Ceramics Interna-tional,2014,40(7):9571?9582.
[7] OLSSON M K,MACAK K,GRAF W. Reactive d.c. magne-tron sputter deposited Al 2 O 3 films:large-area coatings for in-dustrial applications[J]. Surface and Coatings Technology,1999,122(2/3):202?207.
[8] LING G W,SHEN H Y,ZHOU F T. Cathode arc deposition technology and its development[J]. Vacuum,1996,1:1?12.
[9] MUSIL J. Recent advances in magnetron sputtering technology [J]. Surface and Coatings Technology,1998,100/101:280?286.
[10] BRAUER G,SZYSZKA B,VERGOHL M,et al. Magne-tron sputtering-milestones of 30 years[J]. Vacuum, 2010,84(12):1354?1359.
[11] ANDERS A. Deposition rates of high power impulse mag-netron sputtering: Physics and economics[J]. Journal of Vacuum Science & Technology A,2010,28(4):783-790.
[12] JIN Y Z,WU W,LI L. Effect of sputtering power on sur-face topography of dc magnetron sputtered Ti thin films ob-served by AFM[J]. Applied Surface Science,2009,255(8):4673?4679.
[13] EDLOU S M,SMAJKIEWICZ A,AL-JUMAILY G A. Op-tical properties and environmental stability of oxide coatings deposited by reactive sputtering[J]. Applied Optics,1993,32(28):5601?5605.
[14] ZHUKOV V V,KRIVOBOKOV V P,YANIN S N. Sput-tering of the magnetron diode target in the presence of an external ion beam[J]. Technical Physics,2006,51:453?458.
[15] PICHUGIN V F,SURMENEV R A,SHESTERIKOV E V,et al. The preparation of calcium phosphate coatings on tita-nium and nickel–titanium by rf-magnetron-sputtered depo-sition:composition,structure and micromechanical proper-ties[J]. Surface and Coatings Technology,2008,202(16):3913?3920.
[16] MUSIL J,RAJSKY A,BELL A J,et al. High-rate mag-netron sputtering[J]. Journal of Vacuum Science and Techno-logy A,1996,14:2187–2191.
[17] MERCS D,F(xiàn)ERRY F,BILLARD A. Hot target sputtering: a new way for high-rate deposition of stoichiometric cera-mic films[J]. Surface and Coatings Technology, 2006,201(6):2276?2281.
[18]VLCEK J,ZUSTIN B,REZEK J,et al. Pulsed magnetron sputtering of metallic films using a hot target[C]//52nd An-nual Technical Conference Proceedings,Santa Clara,CA:Society of Vacuum Coaters,2009:219-223.
[19] MUSIL J,SATAVA V,BAROCH P. High-rate reactive de-position of transparent SiO 2 films containing low amount of Zr from molten magnetron target[J]. Thin Solid Films,2010,519(2):775?777.
[20] TESAR J,MARTAN J,REZEK J. On surface temperatures during high power pulsed magnetron sputtering using a hot target[J]. Surface and Coatings Technology,2011,206(6):1155?1159.
[21] TUMARKIN A V,ZIBROV M,KHODACHENKO G V,et al.High-rate deposition of silicon films in a magnetron dis-charge with liquid target[J]. Journal of Physics Conference Series,2016,768(1):012015.
[22] TUMARKIN A V,ZIBROV M,KHODACHENKO G V ,et al. Technological features of the thick tin film deposition by with magnetron sputtering form liquid-phase target[J]. Key Engineering Materials,2018,781:8-13.
[23] DANILIN B S,KAKURIN M V,MINAYCHEV V E,et al.Deposition of metal coatings by magnetron sputtering from liquid target[J]. Elektron Tekhnol,1978,2(72):84?87.
[24] TUMARKIN A V,KAZIEV A V,KOLODKO D V,et al. De-position of copper coatings in a magnetron with liquid target [J]. Physics of Atomic Nuclei,2015,78(14):1674?1676.
[25] SHAPOVALOV V I,AHMEDOV H,KOZIN A A,et al.Simulation of the effect of argon pressure on thermal pro-cesses in the sputtering unit of a magnetron with a hot tar-get[J]. Vacuum,2021,192:110421.
[26] SHAPOVALOV V I,ZAVYALOV A V,MELESHKO A A.Current-voltage characteristics of a magnetron with a hot ti-tanium target in chemically active environments[J]. Surface and Coatings Technology,2021,417:127189.
[27] ZHUKOV V V,KOSMIN D M,KRIVOBOKOV V P,et al.Magnetron discharge in the diode with a liquid-metal target [R]. Tomsk, Russia: Nuclear Physics Institute at Tomsk Polytechnic University,2004.
[28] KOLODKO D V,LISENKOV V Y,et al. Cu metallization of Al 2 O 3 ceramic by coating deposition from cooled- and hot-target magnetrons[J]. Coatings,2023,13(2):238.
[29]KAZIEV A V,TUMARKINA A V,LEONOVA K A,et al.Discharge parameters and plasma characterization in a dc magnetron with liquid Cu target[J]. Vacuum, 2018, 156:48?54.
[30] TUMARKIN A V,KAZIEV A V,KHARKOV M M,et al.High-current impulse magnetron discharge with liquid tar-get[J]. Surface and Coatings Technology,2016,293:42?47.
[31] BLEYKHER G A,KRIVOBOKOV V P,YURJEVA A V,et al. Energy and substance transfer in magnetron sputtering systems with liquid-phase target[J]. Vacuum, 2016, 124:11?17.
[32] MUSSCHOOT J,HAEMERS J. Qualitative model of the magnetron discharge[J]. Vacuum,2009,84(4):488?493.
[33] MUSIL J. Low-pressure magnetron sputtering[J]. Vacuum,1998,50(3/4):363?372.
[34] POSADOWSKI W M. Self-sustained magnetron co-sputter-ing of Cu and Ni[J]. Thin Solid Films,2004,459(1/2):258?261.
[35] ANDERSSON J,ANDERS A. Gasless sputtering:opportu-nities for ultraclean metallization, coatings in space, and propulsion[J]. Applied Physics Letters,2008,92:221503.
[36] WIATROWSKI A,POSADOWSKI W M,JOZWIAK G,et al.Standard and self-sustained magnetron sputtering deposited Cu films investigated by means of AFM and XRD[J]. Mi-croelectronics Reliability,2011,51(7):1203?1206.
[37] WIATROWSKI A,POSADOWSKI W M,RADZIMSKI Z J.Pulsed dc self-sustained magnetron sputtering[J]. Journal of Vacuum Science & Technology A,2008,26:1277-1281.
[38] BLEYKHER G A,YURYEVA A V,SHABUNIN A S,et al.The properties of Cu films deposited by high rate magnetron sputtering from a liquid target[J]. Vacuum,2019,169:108914.
[39] BLEYKHER G A,BORDULEV A O,YURYEVA A V,et al.Features of copper coatings growth at high-rate deposition using magnetron sputtering systems with a liquid metal target[J]. Surface and Coatings Technology,2017,324:111?120.
[40] SIDELEV D V,BLEYKHER G A,KRIVOBOKOV V P,et al.High-rate magnetron sputtering with hot target[J]. Surface and Coatings Technology,2016,308:168?173.
相關(guān)鏈接