1、引言
由于鈦合金自身的物理屬性,在加工過程中的難度較大,與銑削的刀具之間有較高的黏結性,在銑削過程中不僅會加速刀具磨損,而且黏刀現(xiàn)象造成了摩擦力大,克服摩擦力做功多,產(chǎn)生的熱量較大,溫度難以控制,最終導致了鈦合金銑削效果較差,降低鈦合金的加工精度[1] 。 因此分析鈦合金的銑削溫度變化并實現(xiàn)溫度參數(shù)的自適應控制對其大規(guī)模應用具有重要意義。
目前 PID 控制方法控制鈦合金銑削溫度參數(shù)無法實時掌握TC4鈦合金銑削過程中的溫度變化情況,因此對溫度控制精度不高,影響鈦合金銑削加工精度。 本文以TC4鈦合金作為研究對象,設計一種TC4鈦合金銑削溫度參數(shù)自適應控制方法。
2、TC4鈦合金銑削溫度參數(shù)自適應控制方法研究
2.1 建立TC4 鈦合金銑削溫度熱模型
本文選擇TC4鈦合金在銑削過程中的溫度變化進行銑削熱模型建模。 在銑削加工時,刀具和TC4鈦合金之間發(fā)生摩擦,出現(xiàn)切屑時會產(chǎn)生塑形與剪切,釋放大量熱能[2] ,這種熱量使刀具的物理性質(zhì)產(chǎn)生變化,導致硬度和耐磨性下降。 在實際切割時,刀具前刀面與已切割底層金屬板材、刀具后刀面以及已加工表層材料存在磨擦。 由于鈦合金的彈性模數(shù)很小,可以加工表層材料的回彈率也很大,所以較小的后角將增加對后刀面的磨擦。 有限元分析包括三種摩擦模型:滑動庫侖摩擦、剪切摩擦和磨合滑摩擦。 刀具自身性質(zhì)的變化降低了銑削過程中的精度,為了保證TC4鈦合金的銑削精度,需要對銑削過程的溫度進行精準控制[3] 。 研究TC4鈦合金在銑削過程中的溫度分布,并作為溫度自適應控制的依據(jù)。 合金的銑削過程類似于單點的切削刀具聯(lián)合銑削的過程,主要形變發(fā)生在刀具的邊緣,切割產(chǎn)生的熱量分布情況如圖 1 所示。
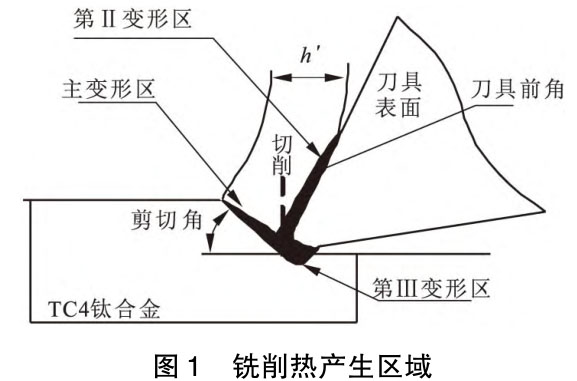
在銑削過程中主變形區(qū)所產(chǎn)生的熱能大部分來自于剪切平面上的塑性作用,第Ⅱ變形區(qū)所產(chǎn)生的熱能主要來自于磨削過程中的形變以及摩擦時做功,第Ⅲ變形區(qū)所產(chǎn)生的熱能主要來自于刀具側面的摩擦以及在銑削過程中作功克服摩擦力產(chǎn)生的熱量[4] 。銑削條件的改變對主變形區(qū)和第Ⅱ變形區(qū)的溫度影響很大,假設沒有磨損帶且加工過程為正交幾何銑削,將剪切平面盡可能地做薄,并在該平面上切斷切屑,在計算過程中將切屑的滑動摩擦系數(shù)取平均值。 銑削過程產(chǎn)生能量的計算式為

式中,F(xiàn)t表示銑削過程中的切向銑削力;v表示銑削速度。
針對銑削過程中主要變形區(qū)的銑削深度來說,每單位的銑削深度所產(chǎn)生的熱量為

式中,F(xiàn)s表示剪切力;Vs表示銑削速度在剪切力方向的分速度;κ 表示摩擦系數(shù)的平均值;h表示發(fā)生形變之前的銑削厚度;αn表示刀具前角;φn表示剪切角。
對于第Ⅱ變形區(qū)的銑削深度來說,單位銑削深度產(chǎn)生的熱量為

式中,βn表示刀具銑削后角度的改變。
在TC4鈦合金工件的銑削過程中,各個變形區(qū)所產(chǎn)生的總熱量為

產(chǎn)生的熱量從主變形區(qū)、第Ⅰ變形區(qū)和第Ⅱ變形區(qū)散失,導致刀具溫度升高,影響刀具在傾斜面的溫度分布。 刀具在傾斜面上的溫度變化也是熱量混合的結果,根據(jù)TC4鈦合金材料的參數(shù),得到如圖 2所示TC4鈦合金銑削速度與溫度之間的變化模型。
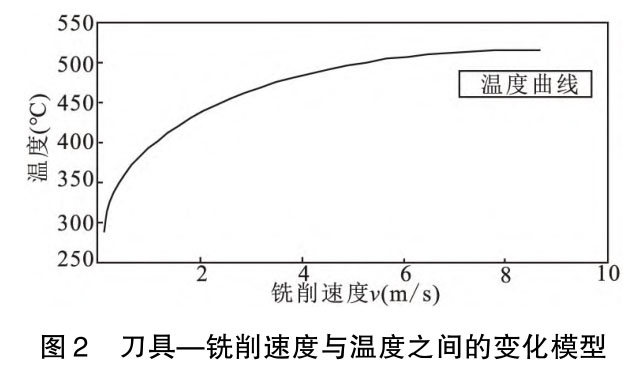
從銑削熱模型變化走勢來看,隨著銑削速度的提高,最高溫度的變化逐漸增加,可以將銑削溫度的變化作為自適應控制的依據(jù),完成TC4鈦合金銑削溫度熱模型的建立。
2.2 基于熱焓修正復合神經(jīng)網(wǎng)絡的銑削溫度控制
根據(jù)銑削溫度熱模型,在銑削區(qū)域能夠?qū)崪y出銑削前后的溫度,因此計算時需要將溫度以及熱焓進行換算。 已知TC4鈦合金工件的熱焓以及奧氏體相變率,通過公式計算出TC4鈦合金工件的溫度。 結合實際的TC4鈦合金工件銑削溫度控制,考慮外部干擾對控制精度的影響,采用熱焓修正復合神經(jīng)網(wǎng)絡作為自適應溫度控制的重要部分,本文設計的熱焓修正復合神經(jīng)網(wǎng)絡主要由兩部分構成:自適應線性神經(jīng)網(wǎng)絡,主要用于實現(xiàn)鈦合金銑削溫度的控制;徑向基神經(jīng)網(wǎng)絡,主要用于銑削過程中工件溫度的感知[5] 。 在這兩個網(wǎng)絡進行復合之后得到如圖 3 所示的熱焓修正復合神經(jīng)網(wǎng)絡結構。
RBF 網(wǎng)絡是構建虛擬全局模型參數(shù)層別空間的重要部分,利用徑向基神經(jīng)網(wǎng)絡部分體現(xiàn)出局部銑削過程的溫度變化適應范圍。 在自適應實際控制過程中,外部環(huán)境對于溫度所產(chǎn)生的干擾難以控制和界定,如果增大范圍值會導致控制過程中的抖振劇烈。 因此在自適應控制的過程中,將系統(tǒng)參數(shù)進行賦值,計算式為

式中,f(X,t)和 g(X,t)均為系統(tǒng)參數(shù);f^ (X,t)和 ^g(X,t)分別表示其標稱部分;Δf(X,t)和 Δg(X,t)分別表示參數(shù)中的變化部分。
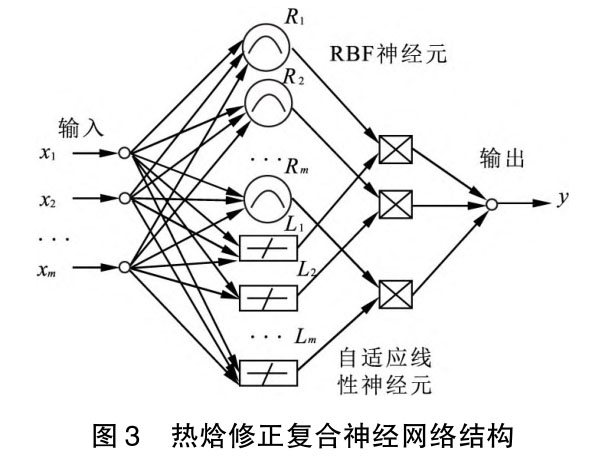
控制過程的主要目的是為了降低抖振和提高速度,設計的自適應控制過程見圖 4。
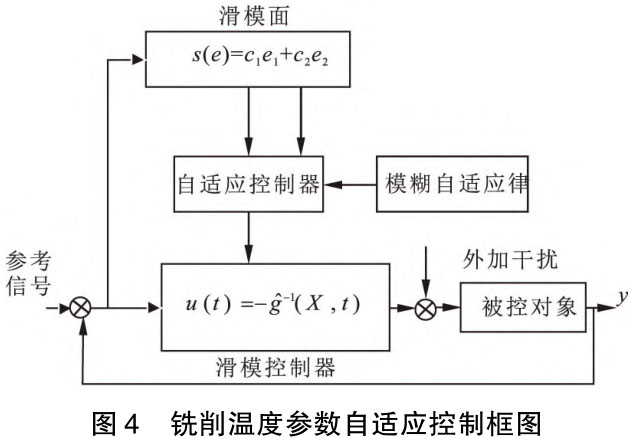
在自適應控制框圖中,設定銑削溫度范圍,確定控制框圖中的跟蹤誤差,將非線性不確定的系統(tǒng)階次進行定級。 將系統(tǒng)參數(shù)的標稱部分作為銑削參數(shù)自適應控制系統(tǒng)中的非線性連續(xù)函數(shù),并將其中不可質(zhì)控的控制增益設置一個模糊的逼近值。 將銑削前后的實際溫度差輸入到自適應控制函數(shù)中,將所得到的切換函數(shù)以及變化率輸入到銑削溫度參數(shù)自適應控制框圖中,在結合之后實現(xiàn)控制過程中的參數(shù)模糊逼近。 在自適應控制系統(tǒng)中,令模糊自適應控制系統(tǒng)的輸出隨著銑削溫度的變化而變化。 定義的自適應模糊逼近調(diào)節(jié)規(guī)則如表 1 所示。
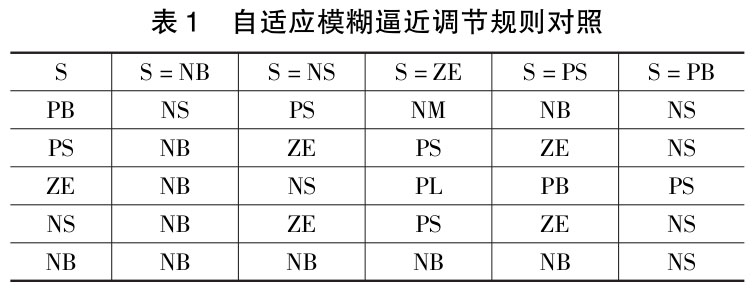
根據(jù)自適應模糊逼近調(diào)節(jié)規(guī)則對照表,在利用成績推理機以及模糊器反解自適應模糊變量的同時能夠得到自適應控制器的輸出情況,表達公式為
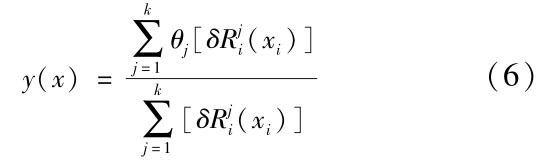
式中,Rji(xi)表示自適應隸屬函數(shù);δ 表示模糊奇函數(shù)中的參數(shù);k 表示自適應規(guī)則的數(shù)量。
在可調(diào)參數(shù)矢量的指引下,將模糊奇函數(shù)矢量與控制器的輸入數(shù)量作為實際的輸入值,其中各項參數(shù)需要按照表中的自適應律進行變化。 在控制過程中定義控制的最小逼近誤差以及最優(yōu)的參數(shù)向量,根據(jù)控制過程中的模糊逼近原理,在各種集合中必定會存在控制器穩(wěn)定分析控制律變。 由自適應控制理論可知,在自適應與模糊理論控制過程中,能夠在緊密集級別以上的任意精度中設置任意連續(xù)函數(shù),并根據(jù)函數(shù)的走勢逐漸逼近。 在自適應模糊規(guī)則的限制下,TC4鈦合金實際銑削過程中避免產(chǎn)生較大誤差。 因此本文在實際控制中結合自適應控制與模糊控制,使模糊系統(tǒng)輸出隨著拱頂溫度變化進行實時調(diào)節(jié),完成TC4鈦合金銑削溫度參數(shù)自適應控制方法的研究。
3、性能分析
3.1 測溫方法設計
為了驗證本文設計的TC4鈦合金銑削溫度參數(shù)自適應控制方法的有效性,需要進行切削溫度自適應控制測試。 實驗選擇 CHS6442 數(shù)控車床,TC4鈦合金棒料,銑削刀片使用 HSD -3214e 硬質(zhì)刀片,83 - ER512 型號的數(shù)控刀桿,其他的實驗裝置還包括熱電偶測溫系統(tǒng)。 實驗過程中在墊片上切出一個寬0. 44mm、深3mm的槽,用于安裝刀片以測定刀具工作溫度,將熱電偶測量系統(tǒng)中的愷式熱電偶安裝于該溝槽的下方,并在刀屑接觸區(qū)下方約 2mm處設定一熱節(jié)點,作為溫度檢測區(qū)域。 選用的TC4鈦合金的主要化學成分如表 2 所示。

以TC4鈦合金銑削熱模型的溫度空間表達式作為實驗對象,并轉換為傳遞函數(shù)形式,得到的銑削溫度熱模型表達式為

在實驗環(huán)境下,分別對本文設計的TC4鈦合金銑削溫度參數(shù)自適應控制方法的抗干擾性能以及魯棒性進行測試,并對實驗結果進行分析。
3.2 抗干擾性能分析
在抗干擾性能分析的過程中,將傳統(tǒng)的 PID 控制方法和本文提出的TC4鈦合金銑削溫度參數(shù)自適應控制方法進行對比,在控制過程中加入階躍信號,設置銑削溫度為 560℃,并在運行 25s 時加入 15%干擾,得到的溫度階躍響應輸出變化情況見圖5。
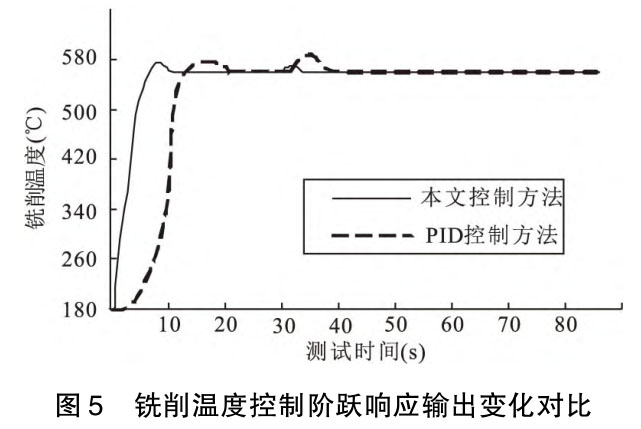
從變化曲線可以看出,在加入干擾階躍之前,傳統(tǒng)的銑削溫度 PID 控制方法在對溫度進行控制的過程匯總,從測試開始到溫度控制穩(wěn)定的過程中,總時間為 21s,在此期間,本文所設計方法的控制穩(wěn)定時間為 8s。 在兩種方法都穩(wěn)定控制后,加入 15% 的階躍干擾,傳統(tǒng) PID 控制方法的調(diào)節(jié)時間為 15s,此時與設定溫度之間所存在的超調(diào)量比例最大達到了10.6%;在階躍干擾下,本文設計的控制方法超調(diào)量比例最大為2.8%,受到階躍干擾到控制穩(wěn)定之間產(chǎn)生的時間為6s。
分析數(shù)據(jù)可以得知,本文設計的TC4鈦合金銑削溫度參數(shù)自適應控制方法比傳統(tǒng)的 PID 控制方法抗干擾能力更好,在受到外界干擾時,能更快的消除抖振,響應速度較快,優(yōu)化控制效果。
3.3 魯棒性分析
為了進一步驗證本文方法的魯棒性,在實驗條件下向測試系統(tǒng)中施加一個 sin(πt)的連續(xù)干擾信號,分別使用本文方法和傳統(tǒng)的 PID 控制方法進行測試,并對比不同測試時間段下的銑削溫度跟隨結果,得到的干擾下不同方法的銑削溫度跟隨結果如圖 6 所示。
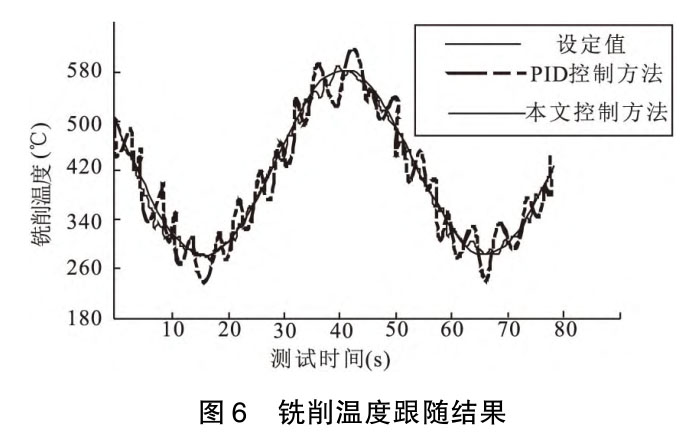
從曲線結果可以看出,在相同的干擾信號下,本文控制方法的輸出銑削溫度的跟蹤誤差大約能夠控制在 ±2%左右,但是傳統(tǒng) PID 控制方法的跟蹤誤差達到了 ±32%,因此本文設計的自適應控制方法跟隨誤差更小,即魯棒性更強,在實際的應用中可以更好的實現(xiàn)TC4鈦合金銑削溫度的高精度控制,減少外部干擾。
4、結語
本文以TC4鈦合金為研究對象,通過建立 TC4鈦合金銑削溫度熱模型,設計了基于熱焓修正復合神經(jīng)網(wǎng)絡的銑削溫度控制過程,對整個溫度參數(shù)的自適應控制方法進行優(yōu)化,并在性能測試中得到了良好的結果,說明本文方法在控制效果中得到的了一定的優(yōu)化。
該方法雖然取得了一定的成績與進展,但僅考慮二維自由銑削,沒有對三維銑削的情況進行驗證,在今后的工作過程中還需要進行改進。
參考文獻
[1]徐建明,趙帥. 工業(yè)機器人動力學參數(shù)辨識與自適應控制方法研究[J]. 浙江工業(yè)大學學報,2020,48(4):375 -383,391.
[2]潘洪坤,關薇,田江平. 基于反饋型自適應魯棒控制的伺服泵直接驅(qū)動電液系統(tǒng)精確運動控制研究[J]. 機床與液壓,2021,49(21):136 -141.
[3]秦長江,胡自化,袁彪,等. - 50℃ 冷風條件下拋光硬質(zhì)合金刀片加工TC4鈦合金的表面粗糙度分析[J]. 表面技術,2020,49(4):364 -371.
[4]李體仁,王心玉,馬超超. 方肩銑刀高速銑削TC4鈦合金試驗研究及參數(shù)優(yōu)化[J]. 機床與液壓,2020,48(8):40-44.
[5]孫鵬程,許小雷,張征,等. 鈦合金TC4高速銑削參數(shù)對銑削力的影響研究[J]. 機床與液壓,2020,48(14):37 -40.
作者:劉浩,副教授,衡水學院機電研究所,053099 河北省衡水市
Author:Liu Hao,Associate Professor,Institute of Mechanicaland Electrical Engineering,Hengshui Uniersity,Hengshui,Hebei053099,China
相關鏈接