為了滿足高功率下的穩(wěn)定濺射,目前先進(jìn)制程用的高純鈦濺射靶材都選取銅合金作為背板材料,并采用擴(kuò)散焊接進(jìn)行綁定。為了保證焊接結(jié)合有足夠的強(qiáng)度,通常還需要在硬度較高的銅合金背板表面加工端面螺紋以增大材料間的接觸面積[2-4]。經(jīng)機(jī)械加工的材料表面極易殘留切削液、潤滑油等臟污,雖然業(yè)內(nèi)對焊接前材料的表面都會做清洗,但清洗的效果、殘留臟污對焊接的影響等,目前都鮮有報(bào)道和研究。本文以純度大于99.995%的高純Ti和CuCr合金為材料,探究不同表面清洗工藝下的擴(kuò)散焊接效果,為制備大尺寸高性能鈦靶材提供依據(jù)。
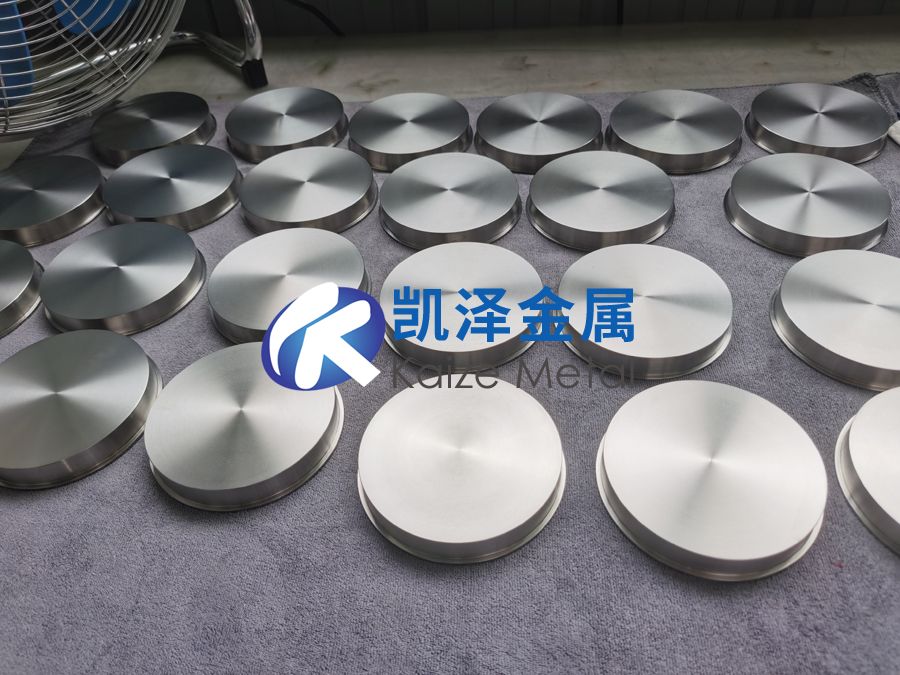
1、實(shí)驗(yàn)材料和方法
實(shí)驗(yàn)材料選取純度大于99.995%的高純Ti和Cr元素含量為1%左右的CuCr合金。Ti樣品和CuCr合金樣品的直徑為φ150mm,CuCr合金樣品焊接面車端面螺紋,尺寸如圖1所示。樣品焊接裝配前分別用表1所示三種清洗方案處理。
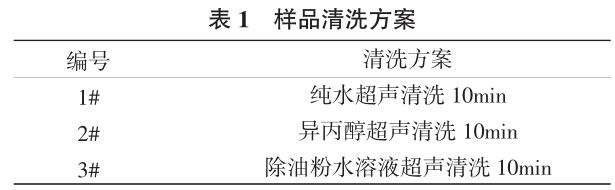
用SITA表面清潔度儀測試焊接面清潔度,每個(gè)樣品測試9個(gè)點(diǎn),測試結(jié)果以RFU值表示,RFU值越低,表面越清潔。實(shí)驗(yàn)采用熱等靜壓(HIP)方式進(jìn)行擴(kuò)散焊接。Ti樣品和CuCr合金樣品裝配后用鋁制包套真空密封,隨后置于熱等靜壓設(shè)備中,熱等靜壓的工藝為500℃/150MPa保溫3h。
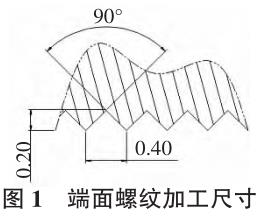
焊接樣品經(jīng)機(jī)械方法拋光后,用10%硝酸溶液腐蝕,使用ZeissAxioObsever5m顯微鏡觀察微觀形貌。用HitachiSU3500掃描電子顯微鏡分析界面狀態(tài)及擴(kuò)散情況。用萬辰CMT電子萬能試驗(yàn)機(jī)測試焊接結(jié)合強(qiáng)度。
2、實(shí)驗(yàn)結(jié)果和分析
2.1清洗效果分析
Ti樣品的清潔度結(jié)果如表2所示。除油粉水溶液對油污有乳化和皂化作用[5],其清洗效果最佳;異丙醇對油污有一定溶解能力,對光滑表面的Ti樣品也有良好的清潔能力,略遜于除油粉水溶液;純水在超聲波輔助下表現(xiàn)出一定清潔能力,但效果在3種方法中是最差的。

CuCr合金樣品的清潔度如表3所示。CuCr合金焊接端面的螺紋和上面細(xì)小的加工缺陷極易吸附大量油污,機(jī)加后的清潔度遠(yuǎn)差于Ti樣品。3種清洗方案對CuCr合金樣品都表現(xiàn)出一定清潔能力,其中除油粉水溶液清洗的樣品最干凈,表面清潔度一致性較好;純水清洗的樣品最臟,檢測點(diǎn)間的清潔度差異較大;異丙醇的清洗效果居上述兩種方案之間,但因?yàn)镃uCr合金表面螺紋影響,效果不及清洗光滑表面的Ti樣品。
2.2焊接界面分析
通過不同清洗方案獲得表面清潔度不同的材料,對這些材料進(jìn)行組合焊接來探究表面清潔度對焊接的影響,具體組合方案如表4所示。
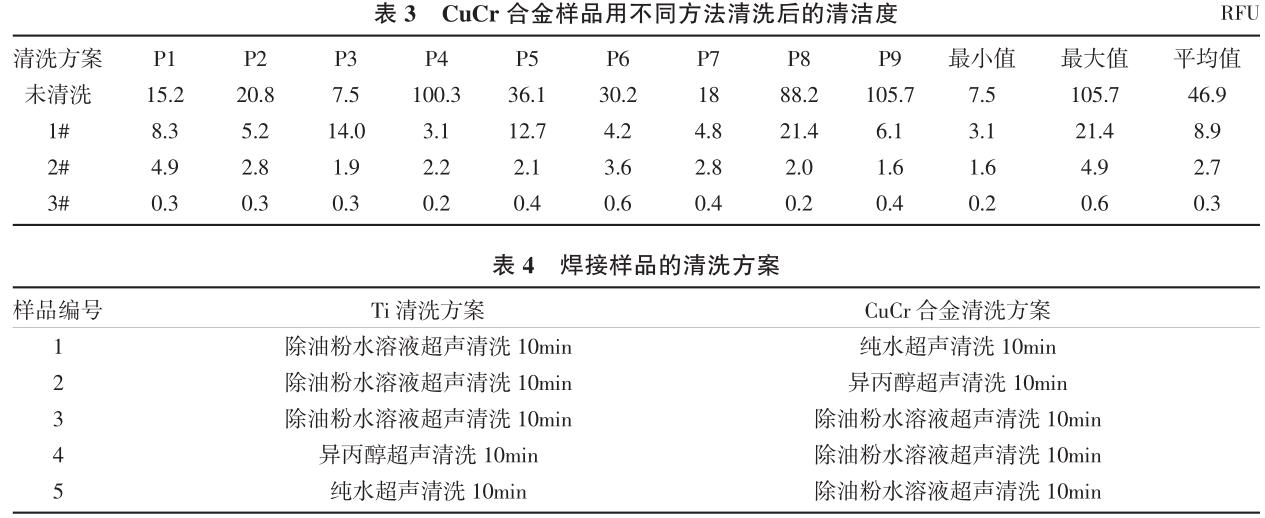
圖3所示,5個(gè)樣品的CuCr合金背板上的螺牙均完整咬入Ti基體,但因咬入過程中受到Ti材料擠壓牙形有輕微變形,5個(gè)樣品的螺牙尺寸無明顯差異。用顯微鏡400倍對每個(gè)樣品觀測一段長度15mm的界面,典型形貌如圖4所示,1號、2號和5號樣品的螺牙底部和牙斜面都發(fā)現(xiàn)有微小的間隙,3號和4號樣品僅在螺牙底部發(fā)現(xiàn)有間隙。隨著螺牙咬入深度增加,Ti基體局部塑性變形難度加大,實(shí)驗(yàn)焊接條件下螺牙咬入深度已到極限,因此5個(gè)樣品的螺牙底部都存在間隙。根據(jù)清洗后材料表面的清潔度推斷1號、2號和5號樣品牙斜面的間隙是界面殘留的臟污阻礙材料相互接觸造成的,而3號和4號樣品焊接面的清潔度高,因此牙斜面處無臟污阻隔,兩種材料貼合良好。間隙處材料無法形成擴(kuò)散,理論上間隙存在的面積越大,焊接結(jié)合強(qiáng)度越小。用掃描電子顯微鏡能譜分析線掃3號樣品螺牙斜面界面,結(jié)果如圖5所示,Ti/Cu元素在界面有擴(kuò)散現(xiàn)象,擴(kuò)散深度約4μm,說明實(shí)驗(yàn)焊接條件下材料間可以形成擴(kuò)散結(jié)合。
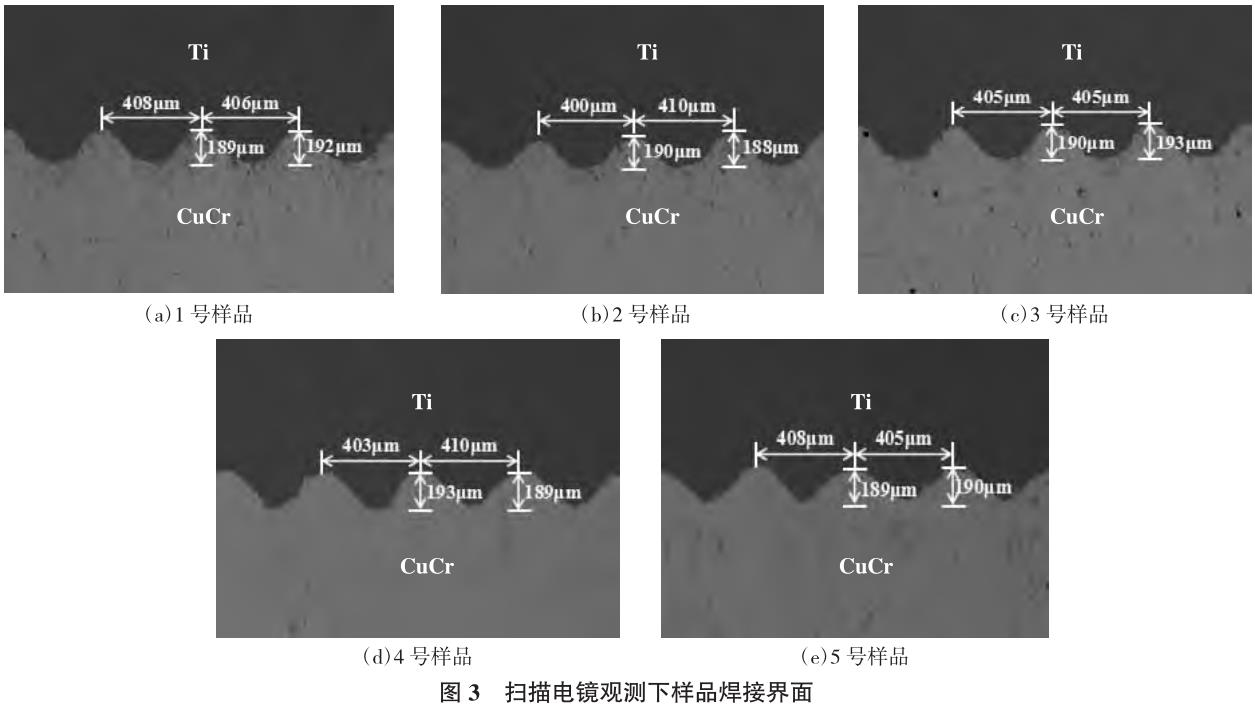
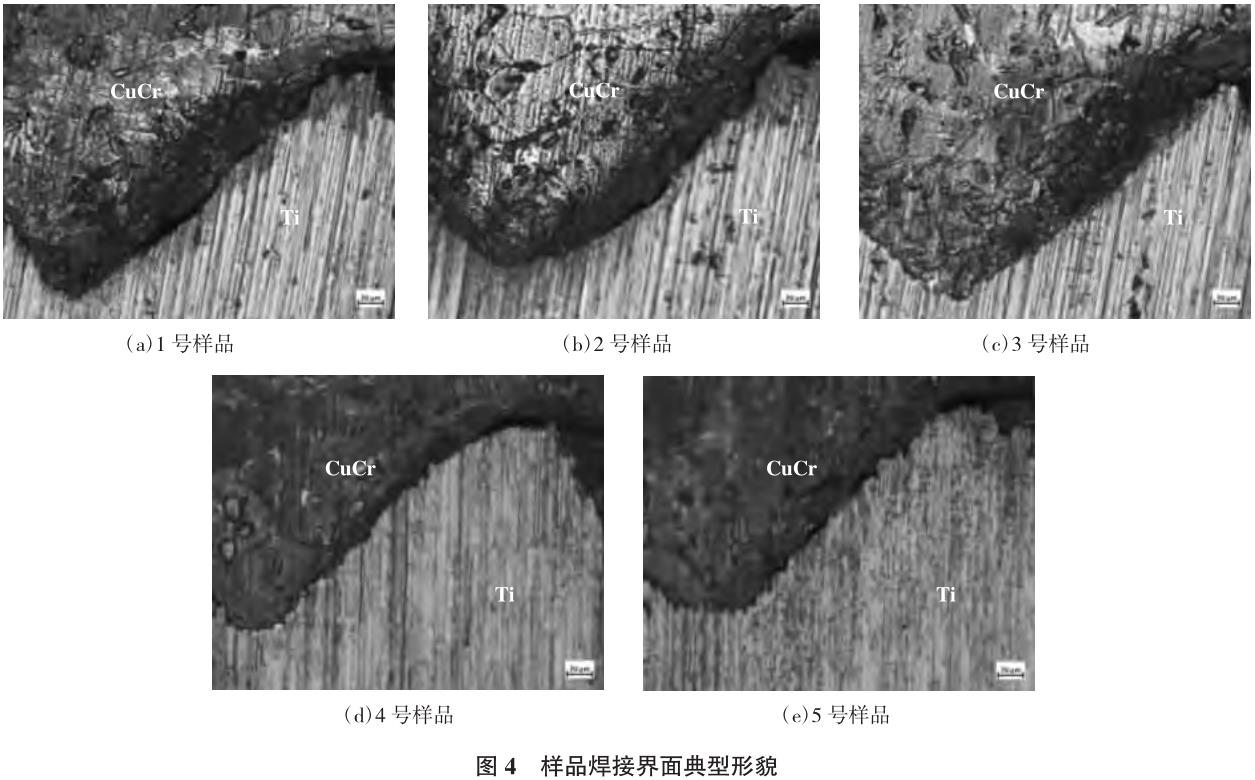
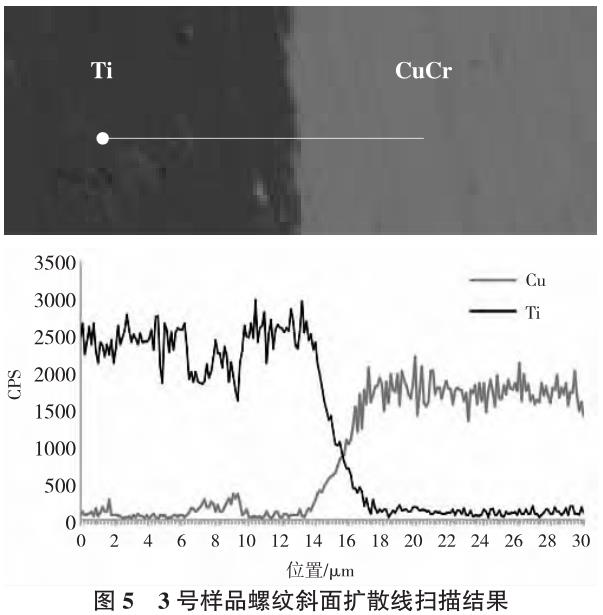
2.3焊接強(qiáng)度分析
大結(jié)合面積和擴(kuò)散結(jié)合是保證高焊接強(qiáng)度的必要條件,通過焊接強(qiáng)度可以進(jìn)一步確認(rèn)界面清潔度對焊接的影響。按圖6所示,加工焊接結(jié)合強(qiáng)度測試樣,測得樣品焊接結(jié)合強(qiáng)度按編號依次為85、183、260、238和177MPa。因?yàn)?號樣品背板的清潔度檢測數(shù)值遠(yuǎn)高于其他幾組,判斷其焊接材料間能形成擴(kuò)散結(jié)合的面積最小,致使強(qiáng)度最低。隨著焊接面清潔度的提升,焊接強(qiáng)度明顯提高;2號和5號樣品的焊接面清潔度接近,均好于1號樣品,它們的焊接強(qiáng)度也相近,遠(yuǎn)高于1號樣品;3號樣品焊接面的清潔度最好,材料間能夠形成擴(kuò)散結(jié)合的面積最大,其焊接強(qiáng)度最高;4號樣品材料界面的清潔度和3號樣品在同一量級,兩者焊接強(qiáng)度無明顯差異。
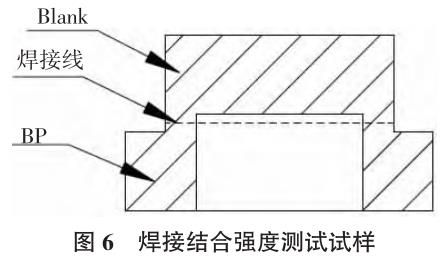
3、結(jié)論
(1)表面清潔度對焊接有很大的影響,焊接界面殘留的臟污阻礙材料間的擴(kuò)散結(jié)合,材料清潔度越高,結(jié)合效果越好,焊接結(jié)合強(qiáng)度越大。
(2)高純Ti和CuCr合金經(jīng)除油粉水溶液超聲清洗10min后表面潔凈度高,兩者在500℃/150MPa保溫3h條件下熱等靜壓焊接,結(jié)合強(qiáng)度可以達(dá)到260MPa以上,界面實(shí)現(xiàn)擴(kuò)散結(jié)合。
參考文獻(xiàn)
[1]董亭義,戶赫龍,于文軍,等.集成電路用鈦靶材和銅鉻合金背板擴(kuò)散焊接技術(shù)研究[J].金屬功能材料,2017,24(6):23-27.
[2]徐國進(jìn),張巧霞,羅俊鋒,等.高純稀土釔靶材焊接技術(shù)[J].焊接,2021,(3):35-38.
[3]徐清鋒.高純金屬銅與銅基合金固相連接研究[D].哈爾濱:哈爾濱工業(yè)大學(xué),2018.
[4]楊衛(wèi)英,伍智.電真空用金屬零件的去油方法[J].真空,2012,49(6):79-82.
相關(guān)鏈接