引言
鈦基材料因具有耐腐蝕性能好、密度低、比強(qiáng)度高等優(yōu)良的物理性質(zhì),在真空鍍膜領(lǐng)域中常被用做靶材來制備鈦基復(fù)合材料,從而提高基材性能和使用壽命,不僅可以合理的利用資源,降低生產(chǎn)成本,也促進(jìn)了鈦材在工業(yè)領(lǐng)域的應(yīng)用[1-2]。在眾多的鍍膜技術(shù)中,磁控濺射技術(shù)具有基片溫升慢、沉積速率快等優(yōu)點(diǎn),能夠有效提高薄膜附著力和均勻性,而且?guī)缀跛械慕饘俣伎梢宰鳛闉R射靶,因此廣泛應(yīng)用于各種工業(yè)薄膜制備領(lǐng)域中。高純鈦材作為一種昂貴的金屬靶材,其冶煉過程復(fù)雜,制造成本較高,作為濺射鍍膜過程中的核心部件,其特性直接影響到膜層質(zhì)量以及鍍膜成本,因此,提高鈦靶的利用率和穩(wěn)定性尤為重要[3-4]。
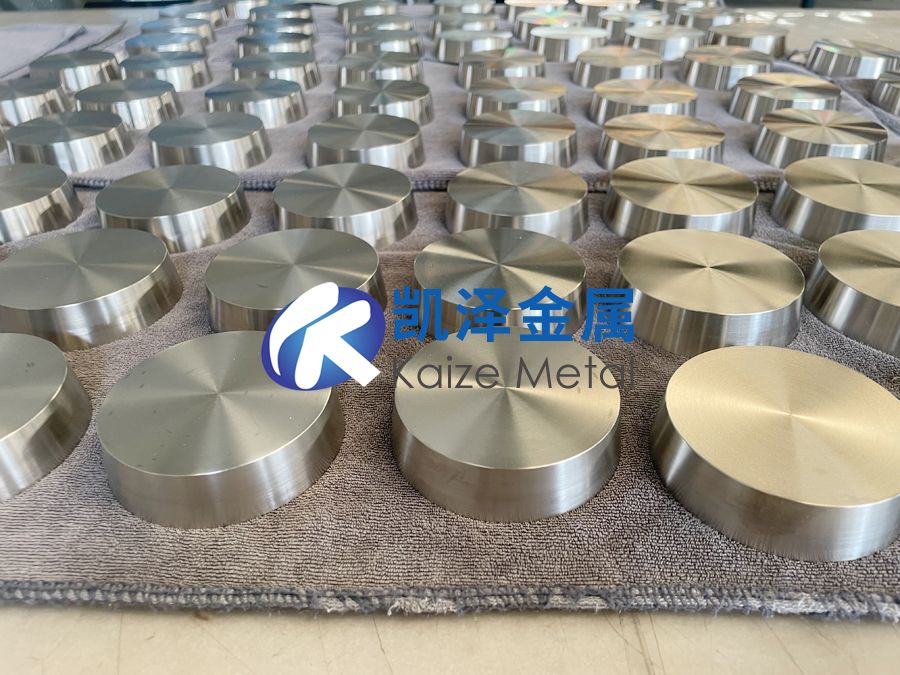
在磁控濺射鍍膜過程中,濺射靶的功率密度受到靶熱負(fù)荷的限制,其中80%的電能都會(huì)轉(zhuǎn)化為熱量,導(dǎo)致鈦靶急劇升溫[5-6]。當(dāng)濺射電流較大時(shí),過多陽離子對(duì)靶進(jìn)行轟擊會(huì)使濺射靶過熱而燒毀,或因熱應(yīng)力過大使表面出現(xiàn)裂紋,進(jìn)而導(dǎo)致薄膜出現(xiàn)大量斑點(diǎn)缺陷,使用壽命遠(yuǎn)遠(yuǎn)達(dá)不到正常水平[7]。
對(duì)于造價(jià)較高的靶材,如氚鈦靶而言,靶溫過高還會(huì)造成氚氣釋放,影響靶的熱穩(wěn)定性及使用壽命[8-9]。因此,磁控濺射靶都會(huì)設(shè)置冷卻系統(tǒng),通過冷卻水帶走離子轟擊靶材產(chǎn)生能量的約70%[10],從而保證濺射過程的穩(wěn)定性。目前針對(duì)鈦靶制造工藝的研究很多,但對(duì)鈦靶磁控濺射鍍膜過程中的冷卻研究卻很少,因?yàn)闇y(cè)量靶面溫度本身就存在難度[11-13]。隨著計(jì)算機(jī)相關(guān)軟件的開發(fā)和應(yīng)用,為鈦靶的冷卻模擬提供了平臺(tái)。本研究基于FLUENT軟件對(duì)磁控濺射過程中鈦靶的冷卻系統(tǒng)進(jìn)行模擬,通過改變水流入口速度和水流通道結(jié)構(gòu),對(duì)冷卻系統(tǒng)進(jìn)行優(yōu)化,以達(dá)到控制鈦靶溫度、提高鈦靶壽命及磁控濺射穩(wěn)定性的目的。
1、鈦靶冷卻系統(tǒng)的建立與仿真
1.1物理模型的建立
圖1為鈦靶冷卻系統(tǒng)的物理模型,鈦靶(r=75mm,t=8mm)和銅背板(r=100mm,t=14mm)組成。其中銅背板內(nèi)部刻有蛇形冷卻通道結(jié)構(gòu),如圖1a所示。冷卻水進(jìn)出口(截面尺寸為20mm×5mm)分布在同一側(cè),水流進(jìn)入背板后,經(jīng)過三次轉(zhuǎn)折流出背板,設(shè)計(jì)該結(jié)構(gòu)的目的是為了增加水流的湍流效果,增強(qiáng)換熱效率。整個(gè)冷卻系統(tǒng)在LUENT的前處理器GAMBIT中進(jìn)行建模并劃分網(wǎng)格[14],圖1b為簡(jiǎn)化后的鈦靶磁控濺射冷卻系統(tǒng)計(jì)算模型。
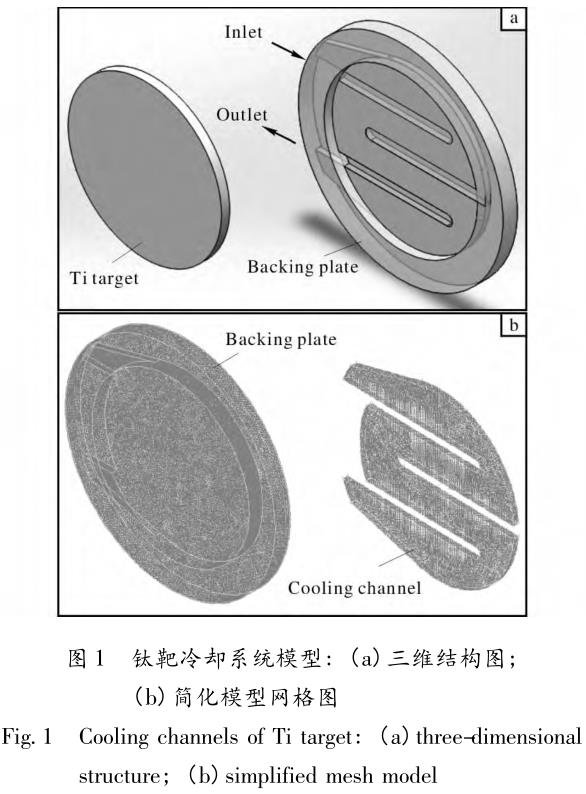
1.2邊界條件設(shè)置
鈦靶冷卻系統(tǒng)的建模包括三部分:銅背板、鈦靶和冷卻水,在FLUENT中進(jìn)行計(jì)算之前,需要設(shè)置合適的邊界條件來保證計(jì)算結(jié)果的正確性。假設(shè)在冷卻過程中,流體流動(dòng)為穩(wěn)態(tài)流動(dòng),流體設(shè)為湍流模型,即雷若數(shù)介于2530~5050之間,選擇標(biāo)準(zhǔn)的k-ε模型。在流體換熱的過程中,由于鈦靶表面局部溫度會(huì)高達(dá)幾百攝氏度,所以會(huì)有很少一部分液體形成蒸汽,但在模擬過程中,為了簡(jiǎn)化計(jì)算模型,這部分相變產(chǎn)生的蒸汽忽略不計(jì)[15]。流體入口設(shè)為VELOCITY-INLET,溫度設(shè)為288K,速度為0.5、1.0、1.5m/s,出口設(shè)為OUTFLOW。在磁控濺射過程中,大部分的電能都通過離子轟擊作用轉(zhuǎn)化為靶材的熱能,故將鈦靶表面設(shè)置為一個(gè)發(fā)熱壁面(HEATWALL),熱流密度為100kW/m2。
由于背板對(duì)鈦材換熱影響較小,設(shè)置為WALL,所有的壁面都為無滑移邊界條件[16],具體的設(shè)置如表1所示。
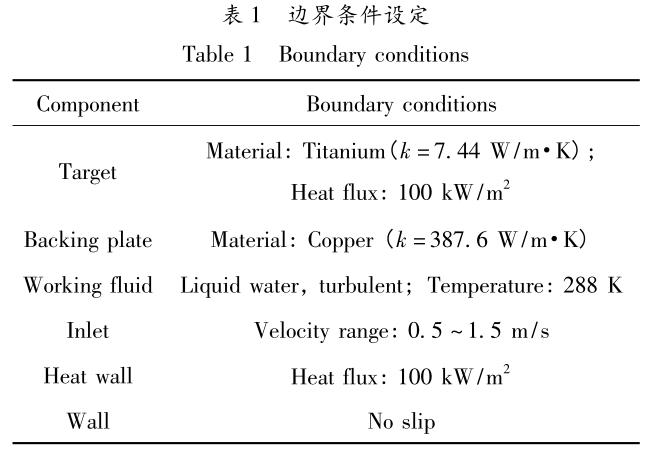
1.3模擬結(jié)果分析
圖2為蛇形冷卻通道的鈦靶表面溫度分布云圖以及水流速度分布云圖。由圖2a可知,當(dāng)水流入口速度為0.5m/s時(shí),在冷卻通道的空白處對(duì)應(yīng)的鈦靶表面換熱效果比較差,熱量聚集在此處無法被有效轉(zhuǎn)移,靶面局部最高溫度可以達(dá)到530K;當(dāng)水流入口速度分別增加到1.0m/s和1.5m/s時(shí),鈦靶表面最高溫度分別為492K和477K。為了便于比較,將三種水流入口速度對(duì)應(yīng)的溫度分布圖放在同一個(gè)溫度刻度表內(nèi)進(jìn)行比較。通過對(duì)比可知:隨著入口水流速度的增加,鈦靶表面整體溫度有明顯的下降,說明水流入口流速在很大程度上影響著換熱效果[17]。
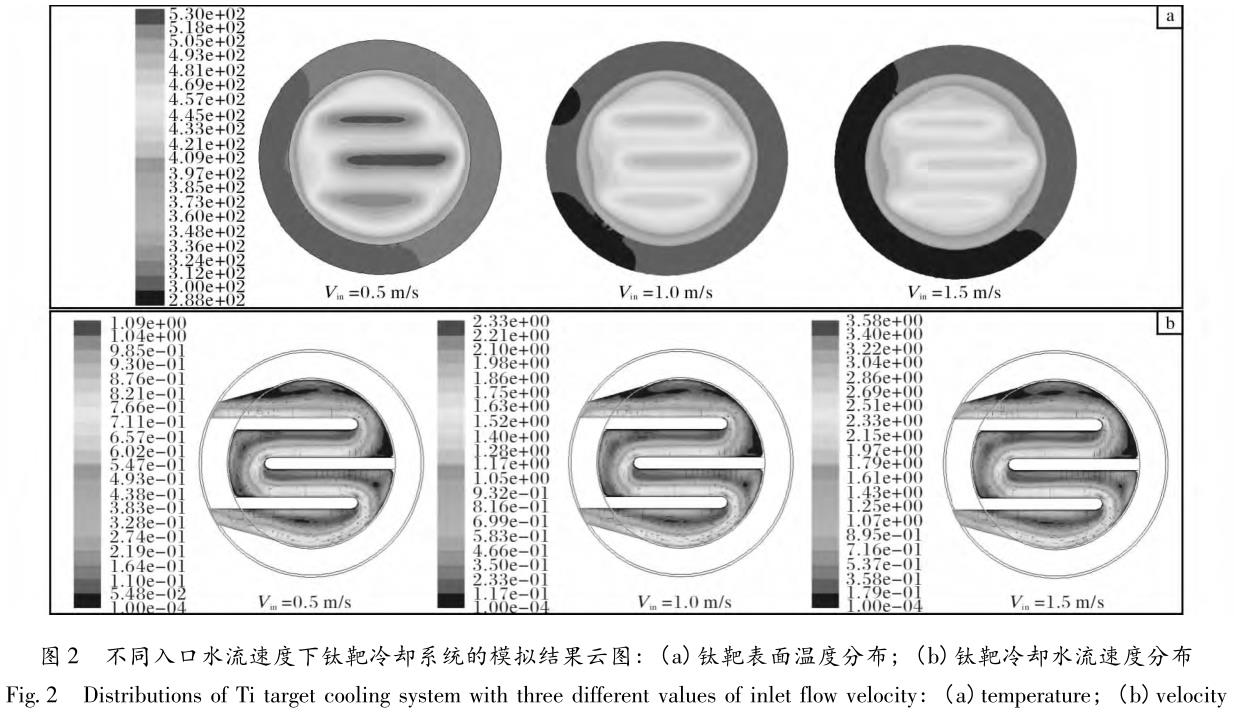
圖2b為蛇形冷卻通道的水流速度分布情況。在結(jié)構(gòu)的限制下,水流發(fā)生強(qiáng)制轉(zhuǎn)折,故湍流效果較明顯,水流的流動(dòng)軌跡大致成“M”形狀,但湍流效果隨著水流速度的增加效果沒有太大的變化。
2、鈦靶冷卻系統(tǒng)優(yōu)化設(shè)計(jì)與分析
2.1鈦靶冷卻通道結(jié)構(gòu)的改進(jìn)
針對(duì)上述模擬結(jié)果提出的問題,提出了如下優(yōu)化結(jié)構(gòu),如圖3所示。
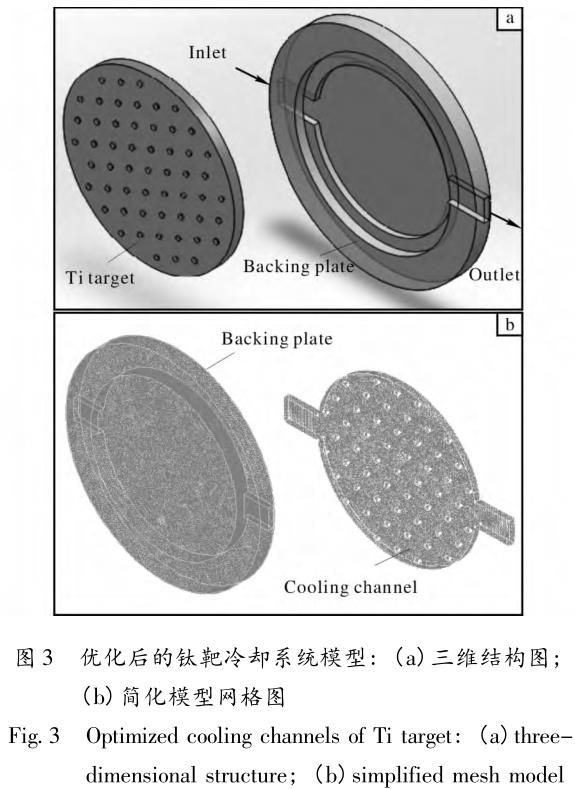
優(yōu)化結(jié)構(gòu)的冷卻通道為平面結(jié)構(gòu),該結(jié)構(gòu)較蛇形結(jié)構(gòu)簡(jiǎn)單,冷卻水的進(jìn)出口(截面尺寸為20mm×5mm)位于同一軸線上。該結(jié)構(gòu)的設(shè)計(jì)目的是增大水流換熱面積,增強(qiáng)換熱效率,同時(shí)通過在鈦靶表面上增加均勻分布的小圓柱體結(jié)構(gòu)(r=5mm,H=2mm)來加強(qiáng)水流的湍流效果。圖3b為簡(jiǎn)化后的計(jì)算模型,分別為背板和水流通道模型。在冷卻模擬的過程中,邊界條件的設(shè)置與上文相同,分別取入口水流速度為0.5、1.0、1.5m/s,模擬結(jié)果如圖4所示,其中圖4a為鈦靶冷卻系統(tǒng)的溫度分布云圖,圖4b為水流速度分布云圖。由圖4a可以看出,當(dāng)水流入口速度為0.5m/s時(shí),鈦靶表面最高溫度達(dá)到464K,與優(yōu)化前相比降低63K,說明優(yōu)化后的結(jié)構(gòu)有利于提高冷卻系統(tǒng)的換熱效率。隨著入口水流速度的增加,鈦靶表面溫度分布有所改善,高溫區(qū)域逐漸減少,并在入口水流速度為1.5m/s時(shí)最好。
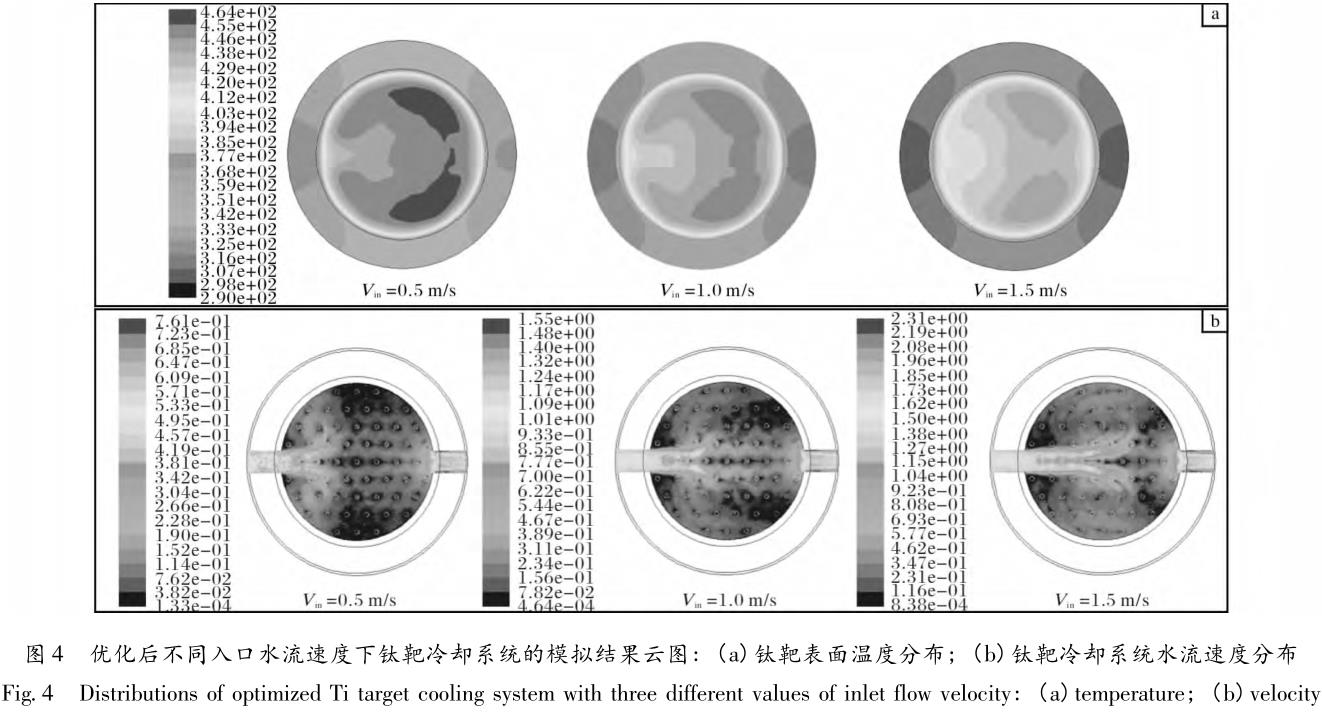
結(jié)合冷卻系統(tǒng)的水流速度分布云圖(圖4b)可知,隨著水流入口速度的增加,湍流效果顯著增強(qiáng),水流的速度分布在進(jìn)出口軸線的兩側(cè)形成漩渦,冷卻水與鈦靶表面之間的換熱增強(qiáng),因此鈦靶表面的平均溫度降低。但該結(jié)構(gòu)仍然存在弊端,整個(gè)鈦靶表面的溫度分布并不均勻,在水流出口處兩側(cè)形成了半圓環(huán)狀的高溫區(qū)域。
在鈦靶表面建立半徑為50mm的環(huán)形(鈦靶表面高溫環(huán)形區(qū)域),其溫度變化趨勢(shì)圖如圖5所示。
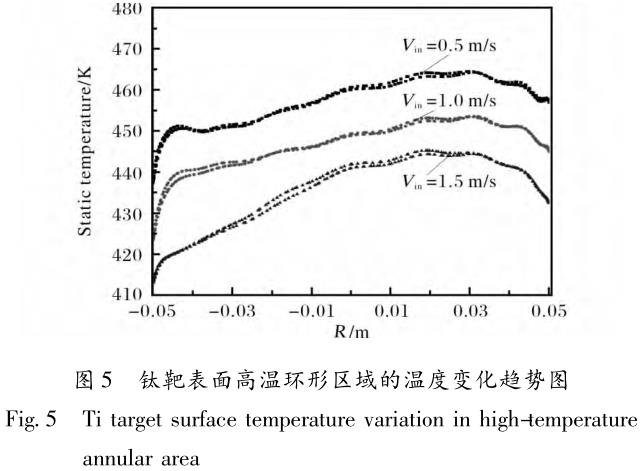
從冷卻水的入口到出口方向看,鈦靶表面環(huán)形區(qū)域溫度整體呈現(xiàn)遞增的趨勢(shì),溫度值波動(dòng)較大造成鈦靶表面溫度分布不均,所以有必要對(duì)冷卻系統(tǒng)結(jié)構(gòu)進(jìn)行進(jìn)一步的優(yōu)化。
鑒于以上分析結(jié)果,結(jié)合冷卻通道本身是圓柱形內(nèi)腔,如果水流沿著內(nèi)腔切向方向進(jìn)入,水流流動(dòng)的阻力就會(huì)大大減小,所以在上述平面冷卻通道結(jié)構(gòu)的基礎(chǔ)上,將進(jìn)出口改為沿內(nèi)壁切向,并研究不同進(jìn)出口夾角對(duì)冷卻效果的影響。
2.2水流進(jìn)出口方向?qū)︹伆袚Q熱效率的影響
水流進(jìn)出口方向沿著冷卻內(nèi)墻壁切向的結(jié)構(gòu)如圖6所示,分別是夾角α為135°、150°、180°時(shí)的三種背板結(jié)構(gòu)。在冷卻模擬的過程中,邊界條件的設(shè)置與上文相同,將三種不同的冷卻系統(tǒng)結(jié)構(gòu)分別導(dǎo)入FLUENT中進(jìn)行冷卻模擬,其中水流進(jìn)口速度均設(shè)置為1.5m/s,經(jīng)過100次迭代后計(jì)算結(jié)果已經(jīng)收斂。模擬結(jié)果如圖7所示,其中圖7a為進(jìn)出口水流速度矢量夾角α為135°、150°、180°時(shí)冷卻系統(tǒng)的水流速度分布云圖,圖7b為冷卻水流動(dòng)軌跡圖。
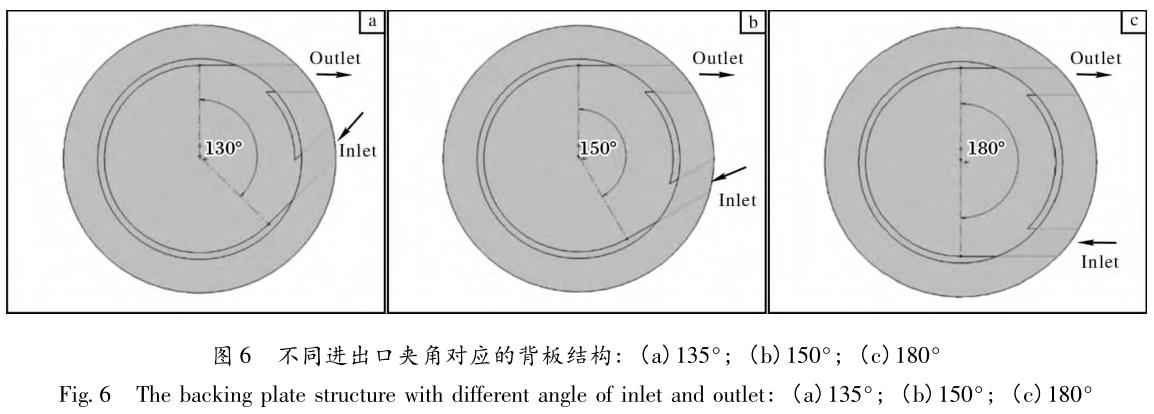
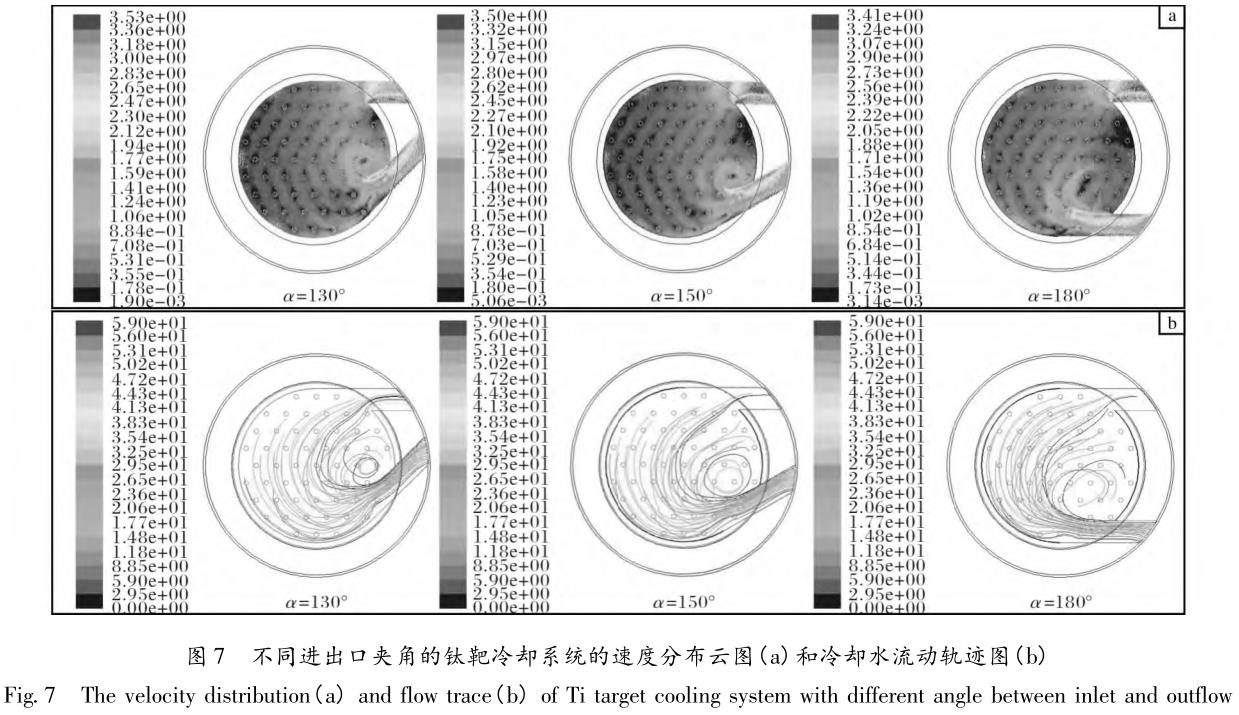
由圖7a可以看出,冷卻水沿著內(nèi)腔切線的流入方式能有效改善速度分布情況,更符合內(nèi)腔本身的結(jié)構(gòu)特點(diǎn)。水流速度在進(jìn)出口附近比較大,這是由于在進(jìn)出口與內(nèi)腔的連接處水流截面面積發(fā)生突增,導(dǎo)致速度突降,但水流速度的降低勢(shì)必會(huì)影響冷卻水與鈦靶的換熱效率,這也是在鈦靶表面均勻布置凸起小圓柱體的原因。通過在鈦靶表面均勻布置凸起的小圓柱體,能有效增強(qiáng)水流湍流效果,增加冷卻水與鈦靶表面的碰撞強(qiáng)度,在流動(dòng)過程中將熱量進(jìn)行有效轉(zhuǎn)移,提高冷卻系統(tǒng)的換熱效率。由圖7a還可以看出,隨著進(jìn)出口距離的增大,冷卻內(nèi)腔速度分布更加均勻,并在進(jìn)出口呈相對(duì)平行布置時(shí)效果達(dá)到最佳,這對(duì)鈦靶表面的溫度分布有一定程度的改善。
由圖7b可以明顯看出水流進(jìn)入冷卻系統(tǒng)后,入口附近的流線分布較密集,而且在進(jìn)出口之間會(huì)形成完整的漩渦,尤其在α角比較小時(shí)更為明顯。在冷卻系統(tǒng)內(nèi)腔結(jié)構(gòu)的限制下,水流軌跡從入口到出口形成了一定半徑的圓弧,且距離進(jìn)出口越遠(yuǎn),圓弧軌跡半徑越大,同時(shí)流線分布也越稀疏。這是因?yàn)榫嚯x進(jìn)出口越遠(yuǎn)的區(qū)域水流速度越小,能量相對(duì)較弱,因此會(huì)出現(xiàn)流線稀疏的現(xiàn)象,甚至在出口附近會(huì)形成空白。但隨著α角的增大,流線的整體分布情況會(huì)有所改善,在進(jìn)出口呈相對(duì)平行布置時(shí)的流線分布較為理想。
為了更加直觀地呈現(xiàn)不同進(jìn)出口布置下鈦靶表面的溫度分布情況,在FLUENT后處理中,將鈦靶表面溫度數(shù)據(jù)導(dǎo)出并通過origin進(jìn)行數(shù)值分析,得出如圖8所示的鈦靶表面溫度分布云圖。
由圖8a可知,當(dāng)夾角α為135°時(shí),鈦靶表面的高溫區(qū)域集中在距離進(jìn)出口較遠(yuǎn)的區(qū)域,最高溫度值達(dá)到447K。由圖8b、c可以看出,隨著α角的增大,高溫區(qū)域逐漸減小,并在進(jìn)出口呈平行布置時(shí)最小,且鈦靶表面最高溫度為440K。數(shù)值分析結(jié)果與上述流場(chǎng)分析結(jié)果一致,證明了當(dāng)冷卻水的入口速度保持不變時(shí),水流進(jìn)出口速度矢量夾角對(duì)鈦靶表面冷卻效果具有較大的影響,當(dāng)夾角增加至180°,即進(jìn)出口呈平行布置時(shí),鈦靶表面冷卻效果最好。
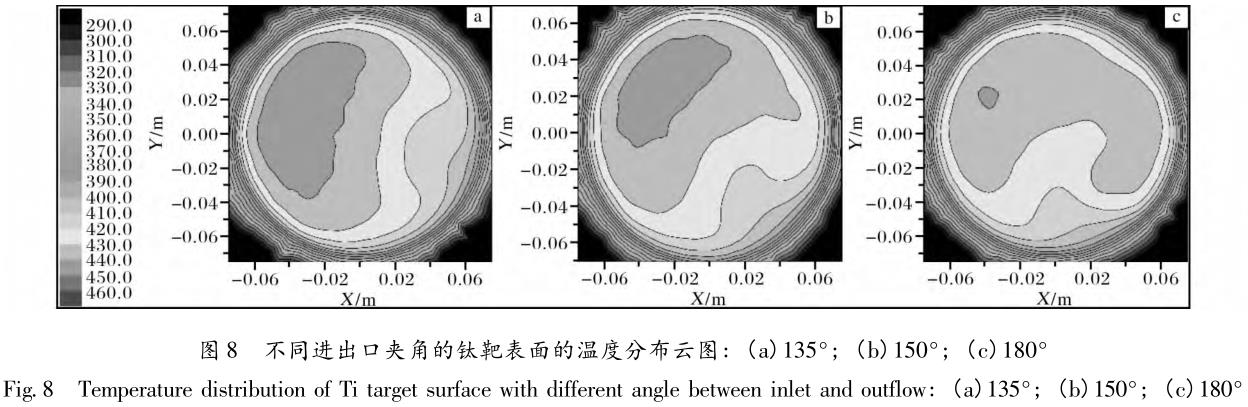
圖9為當(dāng)水流流速為1.5m/s且進(jìn)出口呈相對(duì)平行(α=180°)時(shí)水流分別沿著圖3和圖6c所示的進(jìn)出口方向流入冷卻系統(tǒng)時(shí)的鈦靶表面溫度分布情況。從圖中可以明顯看出優(yōu)化后的鈦靶表面溫度分布更均勻,且平均溫度也有所降低,也進(jìn)一步的說明優(yōu)化后的結(jié)構(gòu)是合理的。
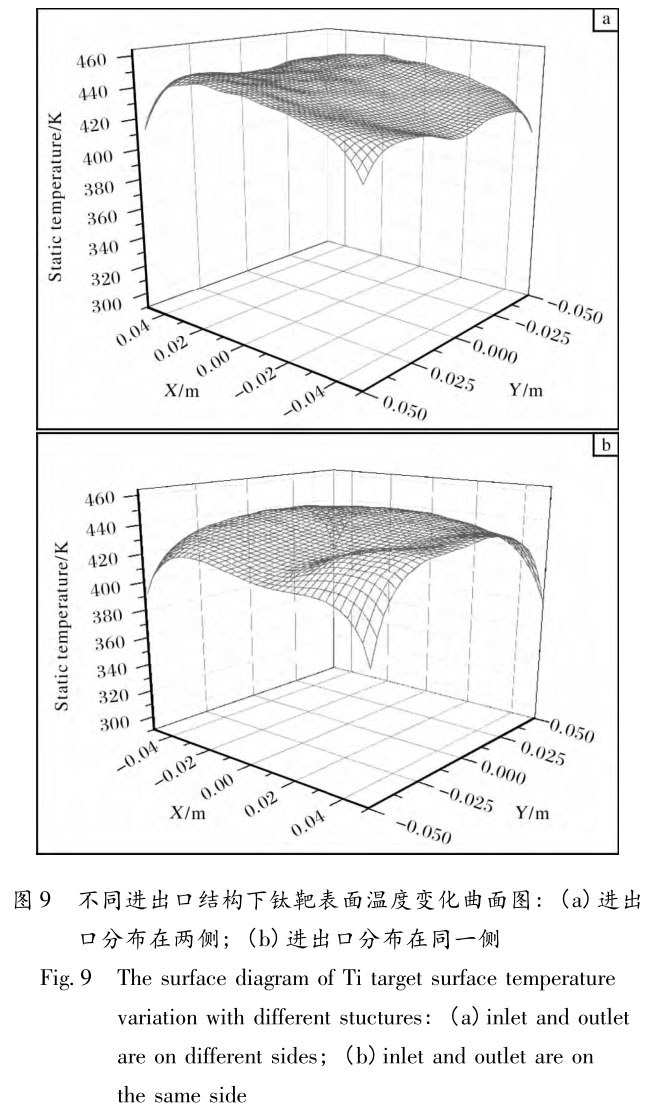
3、結(jié)論
基于FLUENT軟件對(duì)鈦靶的冷卻系統(tǒng)進(jìn)行仿真并做出合理優(yōu)化,得到的主要結(jié)論如下:
(1)平面冷卻通道結(jié)構(gòu)的換熱效果優(yōu)于蛇形冷卻通道結(jié)構(gòu),同時(shí)水流入口速度對(duì)冷卻系統(tǒng)的換熱效率有較大的影響,隨著水流入口速度的增加,靶面整體溫度顯著降低。
(2)提高冷卻系統(tǒng)的換熱效率應(yīng)兼顧換熱面積最大化以及冷卻水的湍流效果,針對(duì)平面冷卻通道而言,靶面均布凸起小圓柱體結(jié)構(gòu)能有效增加水的湍流效果,提高冷卻水與靶材的換熱效率。
(3)冷卻水沿著內(nèi)腔的切線進(jìn)出更符合冷卻系統(tǒng)結(jié)構(gòu)本身的特點(diǎn),流體軌跡在腔體內(nèi)呈旋轉(zhuǎn)狀,流體湍流效果較好,系統(tǒng)的冷卻效率明顯提高。且當(dāng)水流進(jìn)出口呈相對(duì)平行時(shí)靶面最高溫度最小,整個(gè)靶面溫度分布也更均勻。
參考文獻(xiàn)
[1]楊江.采用磁控濺射法在鋼材表面鍍鈦膜研究[D].成都:西華大學(xué),2012.
[2]楊江,鄒敏,賴奇,等.真空鍍膜技術(shù)制備鈦基復(fù)合材料研究現(xiàn)狀[J].攀枝花學(xué)院學(xué)報(bào):綜合版,2011,28(6):4-8.
[3]張以忱.真空鍍膜技術(shù)與設(shè)備[M].北京:冶金工業(yè)出版社,2014:33-43.
[4]張以忱.真空鍍膜設(shè)備[M].北京:冶金工業(yè)出版社,2015:157-160.
[5]BrauerG,SzyszkaB,VerghlM,etal.Magnetronsputte-ring-Milestonesof30years[J].Vacuum,2010,84(12):1354-1359.
[6]李希平.高功率復(fù)合脈沖磁控濺射等離子體特性及TiN薄膜制備[D].哈爾濱:哈爾濱工業(yè)大學(xué),2008.
[7]張之圣,白天,王秀宇.薄膜電阻器用磁控濺射高阻靶材[J].壓電與聲光,2009,31(4):525-527.
[8]曹文鋼,展亮,曹昌勝,等.氚鈦靶系統(tǒng)靶溫升瞬態(tài)分析的方法研究[J].真空科學(xué)與技術(shù)學(xué)報(bào),2014,34(6):575-578.
[9]姚澤恩,陳尚文,蘇桐齡,等.高速旋轉(zhuǎn)氚鈦靶系統(tǒng)設(shè)計(jì)和靶溫度的數(shù)值模擬[J].核技術(shù),2004,27(10):787-791.
[10]余東海,王成勇,成曉玲,等.磁控濺射鍍膜技術(shù)的發(fā)展[J].真空,2009,46(2):19-25.
[11]吳全興.高純鈦靶表面處理技術(shù)開發(fā)[J].稀有金屬快報(bào),2004,23(12):40-41.
[12]劉正紅,陳志強(qiáng).高純鈦的應(yīng)用及其生產(chǎn)方法[J].稀有金屬快報(bào),2008,27(2):1-8.
[13]關(guān)亞蘭,崔秀清,刁訓(xùn)剛,等.TX1800磁控濺射鍍膜機(jī)冷卻系統(tǒng)的改進(jìn)[J].真空,2012,49(5):62-64.
[14]李鵬飛.精通CFD工程仿真與案例實(shí)戰(zhàn)[M].北京:人民郵電出版社,2011.
[15]BaikJS,KimYJ.Astudyontheheattransferenhance-mentinmagnetronsputteringsystem[C]//ASME/JSME2007ThermalEngineeringHeatTransferSummerConfer-encecollocatedwiththeASME2007InterPACKConfer-ence.Vancouver:ASME,2007:315-320.
[16]王德志.圓平面磁控濺射靶的優(yōu)化研究[D].沈陽:東北大學(xué),2011.
[17]王偉明,王保華,李大永,等.等離子槍體中冷卻水流動(dòng)與換熱的數(shù)值模擬[J].計(jì)算物理,2005,22(1):83-87
相關(guān)鏈接