引言
管路構(gòu)件作為起著介質(zhì)傳輸和結(jié)構(gòu)承載等重要作用的典型構(gòu)件,被廣泛應(yīng)用于航空、航天、汽車、核電、醫(yī)療以及日常生活中等諸多領(lǐng)域,也被稱為“工業(yè)動脈”[1,2]。特別是在航空航天等高端裝備領(lǐng)域,管路構(gòu)件被應(yīng)用于液壓、氣動和燃油等核心系統(tǒng)中起流體動力傳輸?shù)汝P(guān)鍵功效(如圖 1 所示),材料和規(guī)格種類繁多且量大面廣,被譽為航空航天飛行器的“血管類”零件和生命控制線[3,4]。這類構(gòu)件在服役過程中往往長期處于高/低溫、高壓、振動或油氣侵蝕等惡劣的環(huán)境當(dāng)中,其性能的優(yōu)劣將直接影響飛行器的安全和適航
性能。當(dāng)前先進飛行器和發(fā)動機裝備的換代發(fā)展,對高性能管材耐高壓、高可靠和長壽命等提出了更高要求,迫切需要采用具有輕質(zhì)高強、抗疲勞以及耐腐蝕優(yōu)異特點的新型鈦合金等材料并提升管材精確成形制造能力,從而全面提升飛行器的綜合指標和性能。
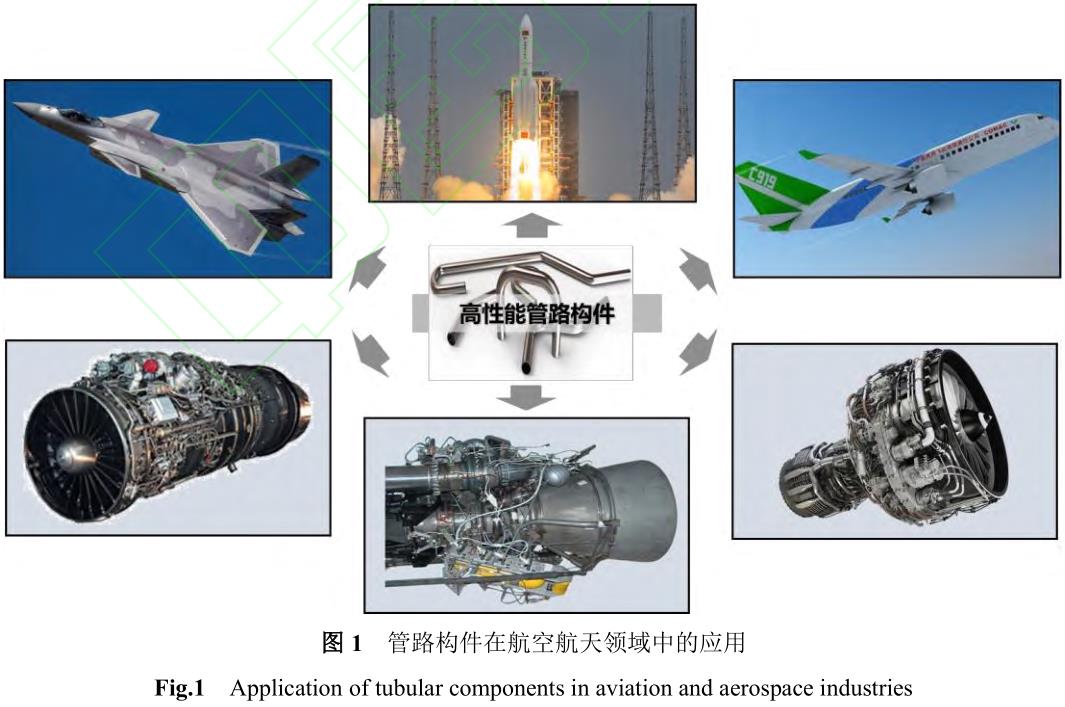
在眾多管材制備工藝中,皮爾格冷軋過程中管材經(jīng)歷了壓應(yīng)力主導(dǎo)的增量局部加載作用,具有道次變形量大、尺寸精度高、表面質(zhì)量好、生產(chǎn)效率高等優(yōu)點,已成為薄壁難變形管材制造的優(yōu)選工藝[5-7]。然而,皮爾格冷軋涉及局部加載下多行程和非穩(wěn)態(tài)成形過程,管材在冷軋過程中經(jīng)歷了復(fù)雜的加載路徑[8-10],同時對于鈦合金和鋯合金等難變形材料來說,成形過程往往要經(jīng)歷多道次冷軋結(jié)合中間和最終熱處理來完成,加之此類材料密排六方非對稱晶體結(jié)構(gòu)特征,導(dǎo)致管材在冷軋中極易發(fā)生顯著不均勻變形,使得管材微觀織構(gòu)演變規(guī)律復(fù)雜并導(dǎo)致分布的不確定性,進而嚴重影響管材的力學(xué)性能、后續(xù)成形性能以及最終服役性能[11,12],諸如管坯初始織構(gòu)、道次變形分配、中間及最終退火工藝以及模具和工藝參數(shù)等設(shè)計稍有不慎都會嚴重影響冷軋過程微觀織構(gòu)分布,進而造成管材性能的波動,給管材形性精確調(diào)控帶來嚴峻的挑戰(zhàn)。因此,深入系統(tǒng)研究難變形管材皮爾格冷軋成形全過程微觀織構(gòu)演變規(guī)律與機理,建立微觀織構(gòu)有效調(diào)控方法,是實現(xiàn)其高性能精確成形制造的關(guān)鍵所在。
本文首先對無縫管材皮爾格冷軋成形技術(shù)進行概述,并對難變形管材多道次皮爾格冷軋成形全過程特點進行分析;詳細綜述分析了管材皮爾格冷軋成形過程宏觀不均勻變形與微觀織構(gòu)演變預(yù)測建模及管材冷軋過程微觀織構(gòu)演變規(guī)律與調(diào)控方法方面的國內(nèi)外研究現(xiàn)狀,在此基礎(chǔ)上針對目前研究中存在不足,探討了難變形管材多道次冷軋全過程微觀織構(gòu)精準調(diào)控及高性能制備尚待解決的問題及未來可能的發(fā)展方向。
1、 管材多道次皮爾格冷軋成形特點
無縫管材的典型制備工藝主要包括擠壓、拉拔和軋制成形,如表 1 所示。其中,擠壓成形技術(shù)保證了管材在成形過程中受到壓應(yīng)力為主的作用,但是屬于一次成形,而高強度管材成形過程中變形抗力極大,因此管材擠壓成形普遍采用熱擠壓的方式進行,從而導(dǎo)致成品管材尺寸精度較低、成形過程材料損失嚴重以及組織性能不均勻等缺陷,熱擠壓主要應(yīng)用于厚壁管坯的制備。拉拔成形得到的制品雖然尺寸精度高且表面質(zhì)量好,但由于管材在成形過程中受到拉應(yīng)力為主的作用且同樣屬于一次成形,導(dǎo)致其每道次加工率小、能量消耗較大以及生產(chǎn)效率較低,因此只適合制備強度低且直徑很小的管材。周期式冷軋技術(shù)在 19 世紀 80 年代首次被提出并逐漸改進發(fā)展為現(xiàn)今的二輥皮爾格冷軋成形技術(shù),與前述兩種無縫管材成形制備工藝相比,整個二輥皮爾格冷軋過程中管材經(jīng)歷了以壓應(yīng)力為主導(dǎo)的增量局部加載作用,這也使得其具有道次變形量大、尺寸精度高、表面質(zhì)量好、生產(chǎn)效率高等優(yōu)點,是眾多管材制備工藝中尤其是對于難變形薄壁管材最有效的一種高精度制備工藝[13-15]。
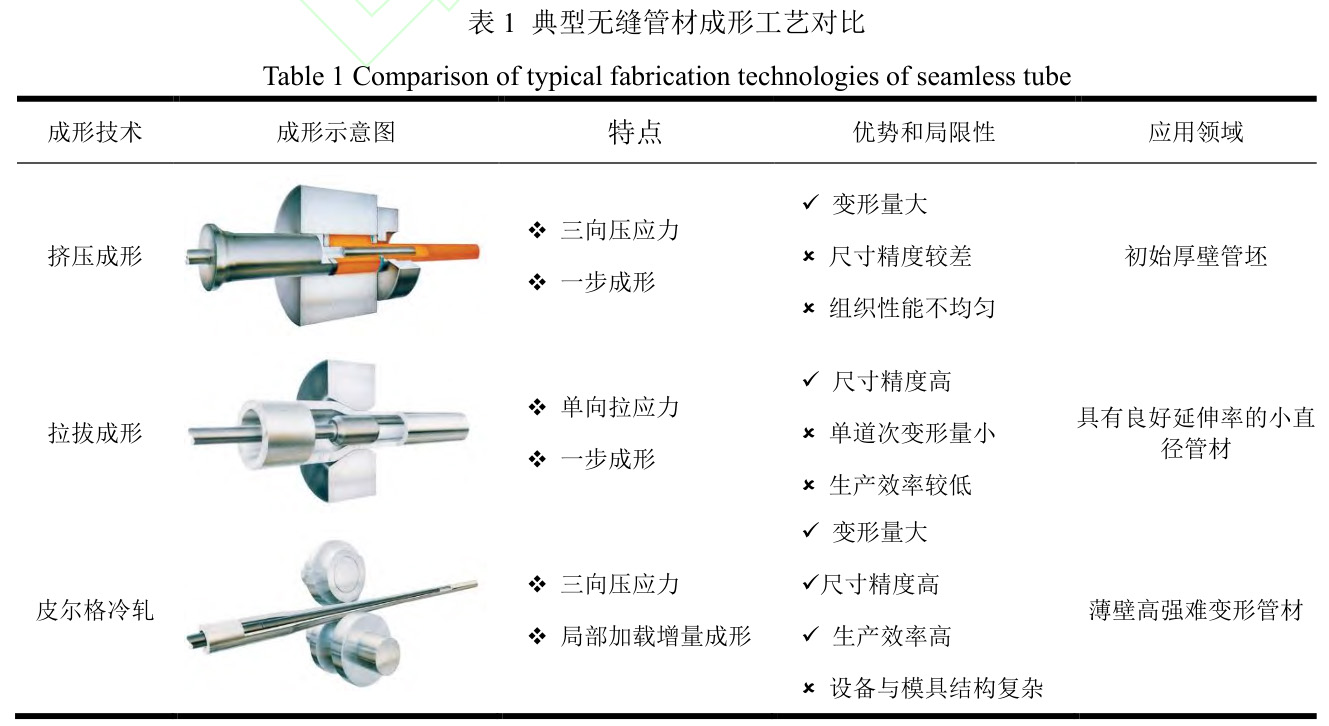
如圖 2 所示,二輥皮爾格冷軋模具主要由上下軋輥和芯棒組成,軋輥圓周上開有截面直徑不斷變化的凹槽,芯棒直徑沿軋制方向呈不斷減小的趨勢,軋輥凹槽與芯棒之間的環(huán)形間隙構(gòu)成了軋制孔型,管材在上下軋輥和芯棒的作用下持續(xù)變形。在軋制過程中管材和芯棒在卡盤的限制下無法移動,軋輥從后極限位置移動到前極限位置的過程稱為正行程,軋輥從前極限位置移動到后極限位置的過程稱為反行程,軋輥如此重復(fù)往返從而實現(xiàn)管材周期軋制過程。皮爾格冷軋過程也可以分為前回轉(zhuǎn)段、工作段(減徑段和壁厚壓下段)、定徑段和后回轉(zhuǎn)段四個不同的階段,前、后回轉(zhuǎn)段的作用主要是為了順利實現(xiàn)管材的回轉(zhuǎn)送進,在工作段管材發(fā)生減徑減壁變形的同時長度伸長,而定徑段主要對管材的內(nèi)外徑和圓度起到精整作用[16,17]。
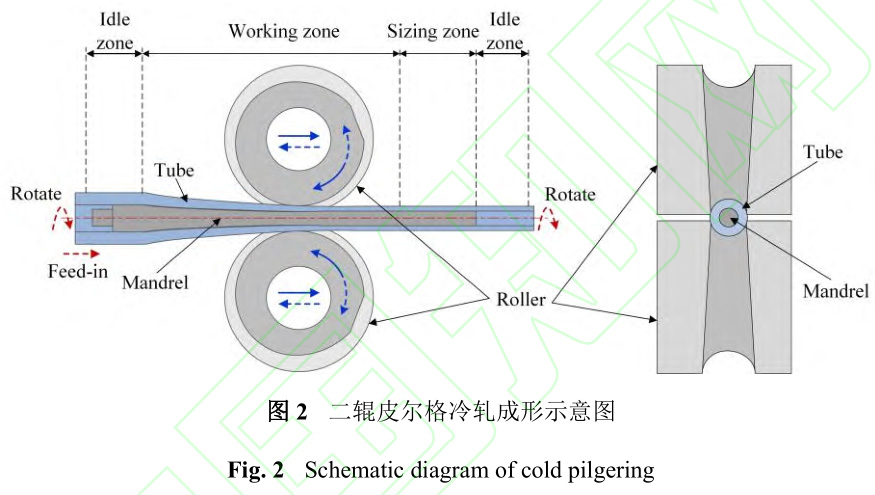
對于強度高且塑性相對較差的難變形管材來說,從初始管坯到目標規(guī)格的成品管材往往要經(jīng)歷多道次冷軋成形,并且在每道次冷軋中間需要對管材進行再結(jié)晶退火恢復(fù)管材塑性以便于下一道次軋制的進行,最終道次冷軋結(jié)束后還需要對管材進行去應(yīng)力退火以消除內(nèi)應(yīng)力的同時保留冷作硬化效果。圖 3 所示為難變形鈦合金管材皮爾格多道次冷軋全過程示意圖,冷軋過程中諸如初始管坯織構(gòu)、道次軋制規(guī)格相關(guān)的冷軋變形模式與變形量、孔型與工藝參數(shù)、以及退火工藝都會對最終管材的織構(gòu)分布帶來顯著影響。多道次冷軋過程中由于成形過程的復(fù)雜性以及工藝參數(shù)的波動將會顯著引起管材微觀織構(gòu)分布的不確定性,進而嚴重影響管材力學(xué)性能、彎曲等成形性能以及疲勞等服役性能,這也是制約管路構(gòu)件高性能制備的關(guān)鍵問題。
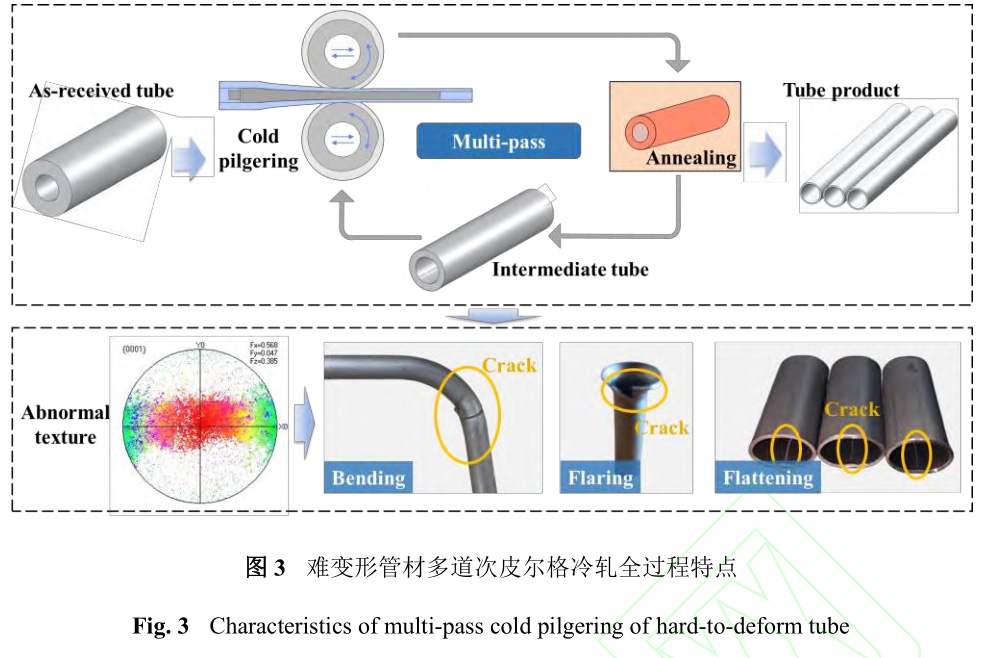
2 、管材冷軋過程變形與微觀織構(gòu)演變預(yù)測建模
2.1 管材冷軋過程宏觀變形預(yù)測建模
由于皮爾格冷軋成形工藝以及模具孔型幾何形狀的復(fù)雜性,導(dǎo)致管材皮爾格冷軋實驗成本高且周期長,同時實驗研究難以準確全面的獲得冷軋過程管材變形行為,而數(shù)值模擬可以獲得豐富的信息,能夠考慮多因素和復(fù)雜邊界的影響,是皮爾格冷軋成形管材宏觀變形行為研究重要的手段[18-20]。
Mulot 等[21]建立了鋯管皮爾格冷軋過程的 3D 有限元模型,分析了一個軋制行程的應(yīng)力和應(yīng)變,得到了沿軋制方向的應(yīng)力和應(yīng)變分布狀態(tài)。Montmitonnet 等[22]以 FORGE3 為平臺,針對鋯合金管皮爾格軋制建立了三維彈塑性有限元模型,該模型將周期循環(huán)運動直接作用在軋輥上,從而簡化了管材皮爾格軋制中的曲柄-連桿-齒輪機構(gòu),分析了皮爾格軋制一個行程中管材的應(yīng)力應(yīng)變分布狀態(tài),并得到了皮爾格軋制多行程中管材上一點的應(yīng)力應(yīng)變變化規(guī)律以及材料流動軌跡,提出在皮爾格軋制過程中,管材上一點的應(yīng)力變化規(guī)
律為正負應(yīng)力交替循環(huán),極易導(dǎo)致低周疲勞和產(chǎn)生表面裂紋,而管材上一點的流動軌跡為螺旋式前進。不同于單一行程的有限元模擬和分析,黃亮等[23]建立了鈦合金管材多行程皮爾格軋制三維有限元模型,模型主要由管材、上下軋輥、芯棒以及推塊構(gòu)成,研究了管材冷軋過程不同方向應(yīng)變變化規(guī)律。楚志兵等[24]以不銹鋼管為對象,建立了一個道次完整軋制過程的三維有限元模型,并利用兩輥軋機進行軋制試驗驗證了回彈預(yù)測模型的可靠性與正確性。
為了提高有限元模擬計算效率和精度,有關(guān)學(xué)者對皮爾格冷軋建模關(guān)鍵技術(shù)進行了改進,Lodej 等[25]以皮爾格冷軋鋯管為研究對象,根據(jù)孔型曲線預(yù)制管材變形段并用于模擬計算,待少量幾個軋制行程后管材變形即趨于穩(wěn)定,并且認為此時的應(yīng)力應(yīng)變狀態(tài)與實際結(jié)果基本吻合,從而提高了計算效率。Strickner 等[26]基于 SIMUFACT 有限元軟件,建立了無縫不銹鋼管冷軋的三維彈塑性有限元模型,該模型通過編寫子程序并嵌入有限元軟件中來精確控制軋輥周期式的循環(huán)運動,并且根據(jù)管材延伸率及送進量,計算出每一行程
軋輥運動的前極限位置,該方法簡化了管材軋制運動過程,縮短了計算時間,提高了計算效率。Deng 等[27]以 Zr-4 管為研究對象,建立材料模型時考慮了應(yīng)變速率和溫度對材料硬化行為的影響,并對試驗和模擬得到的軋制力和管材尺寸進行對比,結(jié)果驗證了該模型的可靠性。Azizoglu 等研究發(fā)現(xiàn)軋輥的變形對接觸區(qū)長度、軋制力以及成品管精度有顯著影響,在有限元建模時將軋輥設(shè)置為彈性體并劃分網(wǎng)格[28],此外,學(xué)者還通過充分考慮管材冷軋過程中與模具和空氣之間的熱輻射實現(xiàn)了不銹鋼管冷軋過程溫度演變的預(yù)測[29],所建立模型如圖 4 所示,并通過試驗對比驗證了上述模型在皮爾格冷軋成形過程軋制力、應(yīng)力應(yīng)變、溫度分布預(yù)測方面的準確性和可靠性。Chung 等[30]在建立不銹鋼管冷軋仿真模型時考慮了管材初始壁厚的不均勻性以及芯棒的彈性變形,模擬結(jié)果表明冷軋過程顯著的塑性變形可以明顯改善管材厚度的均勻性,同時芯棒的振動是導(dǎo)致其末端產(chǎn)生疲勞裂紋的因素之一。
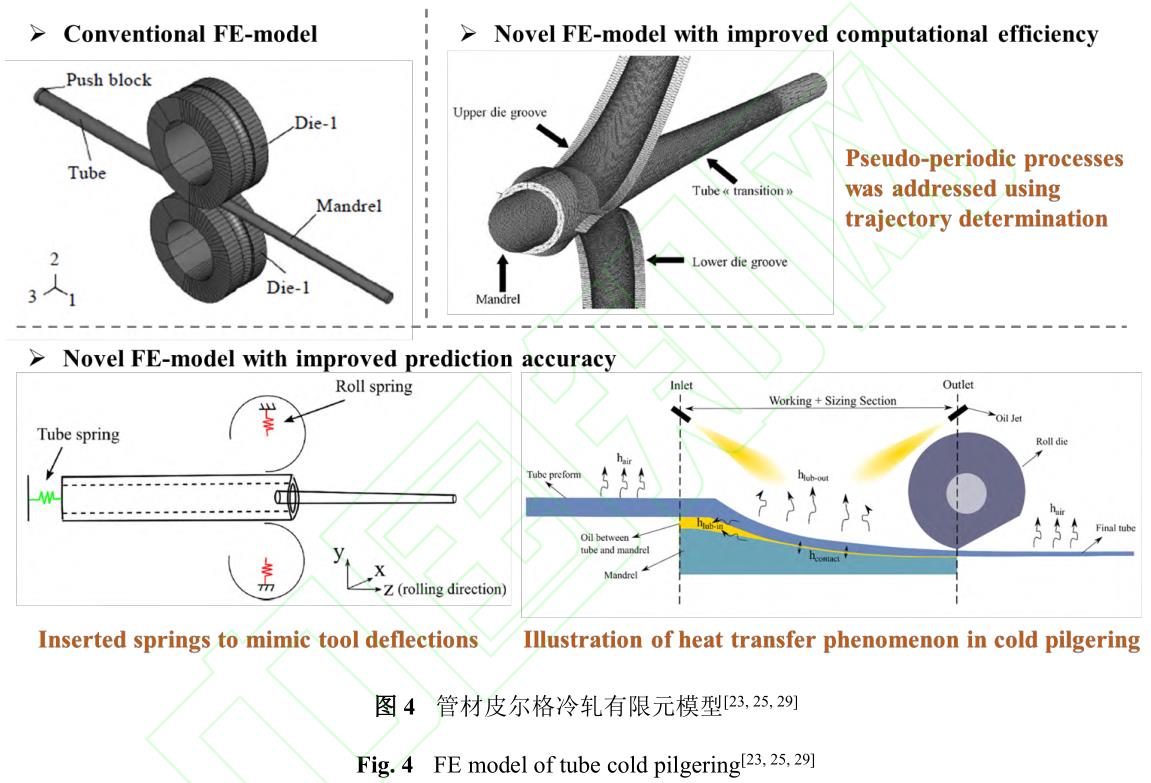
2.2 管材冷軋過程微觀織構(gòu)演變預(yù)測建模
成形過程中織構(gòu)的產(chǎn)生對材料的各向異性以及成形性能等具有顯著的影響,為了能準確預(yù)測材料成形過程中的織構(gòu)演變,以及降低實驗成本和提高效率,大量學(xué)者開始利用晶體塑性模型來模擬成形過程中的織構(gòu)演變規(guī)律。Molinari 等[31]首次建立了多晶體自洽本構(gòu)模型,并應(yīng)用于金屬的大塑性變形過程的織構(gòu)模擬預(yù)測,在此基礎(chǔ)上,Lebensohn 等[32]提出了粘塑性自洽(Viscoplastic Self-consistent, VPSC)模型,該模型考慮了材料的各向異性,引入滑移和孿生兩種金屬塑性變形機制,并采用了 PTR(Predominant Twin Reorientation)晶粒旋轉(zhuǎn)計算方法和 VFT(Volume Fraction Transfer)晶粒取向體積分數(shù)計算方法,已經(jīng)被廣泛應(yīng)用于定量預(yù)測材料塑性變形過程中晶粒取向的轉(zhuǎn)變以及織構(gòu)演變[33-45]。
Lebensohn 等[36]通過引入靜態(tài)速度梯度,首次將 VPSC 模型用于 Zr-4 鋯合金管材皮爾格冷軋成形的織構(gòu)模擬預(yù)測,并與實驗結(jié)果對比,兩者吻合較好。然而,采用靜態(tài)速度梯度無法表征整個軋制過程中的變形特征,因而無法揭示整個軋制過程中的織構(gòu)演化規(guī)律。張海芹[37]和 Li 等[38]在前述研究基礎(chǔ)上,通過耦合有限元模型和 VPSC 模型,建立了高強 TA18 鈦管皮爾格兩輥冷軋過程織構(gòu)預(yù)測平臺,研究了高強 TA18 鈦管的在不同外部載荷下織構(gòu)演化與變形機制的關(guān)聯(lián)關(guān)系,分析了二輥皮爾格冷軋過程中管材的織構(gòu)演變規(guī)律。Wei 等[39]以高強 TA18 鈦管為研究對象,在管材再結(jié)晶退火過程微觀織構(gòu)遺傳特性的基礎(chǔ)上,采用 VPSC 模型迭代每道次模擬中管材力學(xué)性能,并耦合有限元模型和 VPSC 模型建立了高強 TA18 鈦管多道次冷軋全過程宏細觀數(shù)值預(yù)測模型,如圖 5 所示,并通過 3 道次冷軋實驗和表征驗證了模型的可靠性。此外,VPSC 模型也被廣泛應(yīng)用于材料各向異性變形行為以及變形機制的研究[40-42],其中 Yang 等[41]結(jié)合實驗與 VPSC 模擬,探究了純鈦材料熱力加載條件下溫度相關(guān)的各向異性與拉壓非對稱性變形行為及變形機制。Deng 等[42]基于 VPSC 模型,對皮爾格冷軋后的 Zr-4 鋯合金管變形行為與織構(gòu)演變進行了研究。
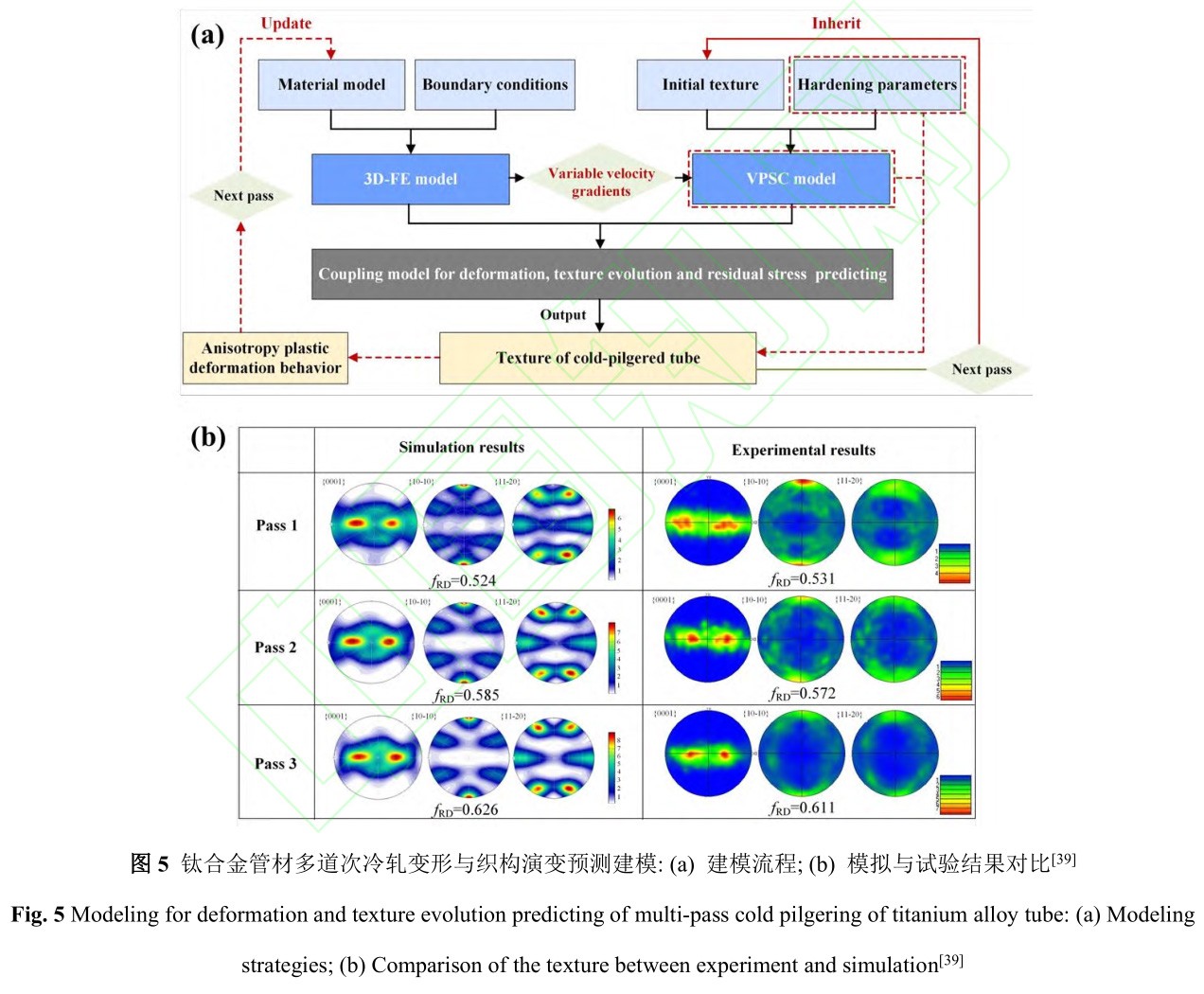
3 、管材冷軋過程微觀織構(gòu)演變機制與調(diào)控方法
3.1 管材冷軋過程微觀織構(gòu)演變規(guī)律與機制
由于管材皮爾格冷軋成形屬于局部加載的增量成形過程,成形過程中應(yīng)變路徑的變化對管材織構(gòu)的演變具有重要影響?;跀?shù)值模擬,國內(nèi)外學(xué)者對管材皮爾格冷軋不同階段管材變形特征進行了深入分析,圖6(a)所示為鈦合金管材冷軋過程不同變形階段圓周應(yīng)力分布特征,從圖中可以看出冷軋不同變形階段管材圓周同一位置應(yīng)力狀態(tài)基本是一致的,并且管材圓周應(yīng)力呈中心對稱分布。在孔型側(cè)壁和孔型開口區(qū)域,管材主要受到三向壓應(yīng)力的作用,而在孔型開口區(qū)域,管材受到徑向和周向壓應(yīng)力以及軸向拉應(yīng)力的作用。冷軋
過程中管材在圓周不同位置應(yīng)力大小具有顯著差別,孔型側(cè)壁區(qū)域所受到的徑向和周向壓應(yīng)力相對較大,這主要是由于冷軋孔型為橢圓形,管材在上一行程軋制后被壓扁,在下一行程軋制時經(jīng)過回轉(zhuǎn)工藝轉(zhuǎn)到孔型側(cè)壁區(qū)域,因此導(dǎo)致了側(cè)壁區(qū)域的相對變形量較大。此外,也可以發(fā)現(xiàn)除圓周應(yīng)力分布不均勻外,管材在壁厚方向應(yīng)力也具有不均勻分布的特征。隨著軋制的進行,管材在圓周以及壁厚方向變形逐漸趨于均勻,不同位置應(yīng)力大小之間的差異也逐漸減小。圖 6(b)為鈦管冷軋過程不同變形階段管材圓周應(yīng)變分布特征,從圖中可以明顯的看出管材在皮爾格冷軋成形過程中經(jīng)歷了顯著的不均勻變形。在減徑段管材圓周方向為壓應(yīng)變,而徑向和軸向均為拉應(yīng)變,這里管材徑向發(fā)生拉應(yīng)變的主要原因是由于冷軋前期管材內(nèi)表面與芯棒之間存在較大的間隙,當(dāng)軋輥對管材外表面進行壓下時,部分金屬流向管材壁厚方向進而導(dǎo)致了管材壁厚的增厚。當(dāng)冷軋進入到中后期,管材內(nèi)壁與芯棒發(fā)生接觸,管材呈現(xiàn)出了軸向為拉應(yīng)變而徑向和周向均為壓應(yīng)變的特征[44]。此外,冷軋過程包括 Q 值、送進量、回轉(zhuǎn)角度及孔型開口大小等工藝參數(shù)的變化也被證實會
引起管材變形行為的差異[17, 20, 45]。
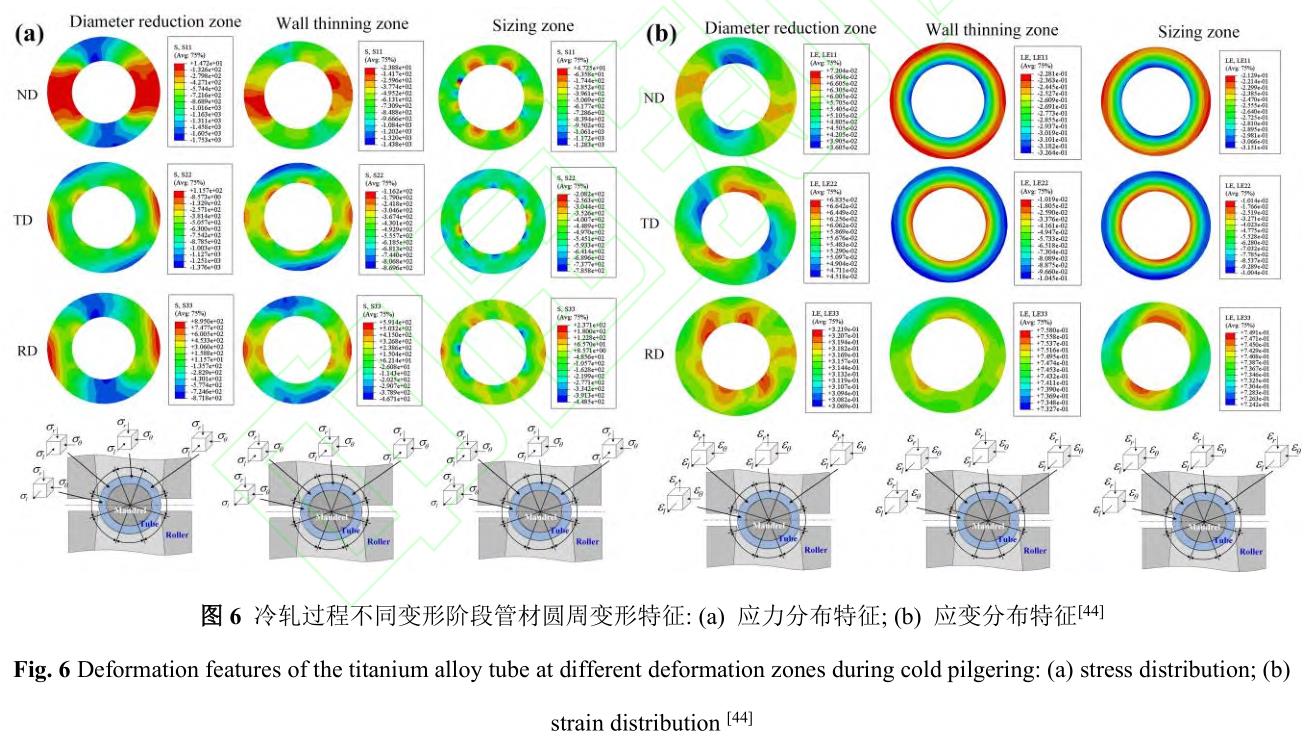
準確揭示和掌握冷軋過程中的微觀織構(gòu)演變規(guī)律,是冷軋工藝和模具優(yōu)化設(shè)計以及織構(gòu)調(diào)控的前提[45,46]。國內(nèi)外學(xué)者對此做了大量的相關(guān)研究工作,Li 等[47]分析了高強鈦管皮爾格冷軋過程中管材的織構(gòu)演變規(guī)律,以應(yīng)變比來表征管材在軋制過程中的變形模式并揭示了織構(gòu)演變與應(yīng)變比 α 之間的關(guān)系,其中應(yīng)變比反映了管材周向與徑向變形的差異,如圖 7(a)所示,結(jié)果表明管材晶粒 c 軸在軋制過程中向最大壓應(yīng)變方向擇優(yōu)排列,管材在減徑區(qū)、減徑減壁區(qū)和定徑區(qū)的應(yīng)變比 α 的變化各不相同,在減徑區(qū)應(yīng)變比 α 約為-64o,在減徑減壁區(qū)和定徑區(qū)應(yīng)變比 α 在 10o~64o 范圍變化,管材經(jīng)歷了由周向織構(gòu)向徑向織構(gòu)轉(zhuǎn)變。Deng等[48]通過電子背散射衍射(Electron Back-Scattered Diffraction, EBSD)手段對 Zircaloy-4 管皮爾格冷軋不同變形階段組織與織構(gòu)演變進行了表征,如圖 7(b)所示,并結(jié)合 VPSC 模擬對冷軋過程變形機制進行了分析,發(fā)現(xiàn)冷軋過程管材變形以{10-10}柱面滑移為主。Davies 等[49]采用 X 射線衍射(XRD)方法對不同送進量下鈦合金管材皮爾格冷軋過程微觀織構(gòu)演變進行了測試對比,其中微觀織構(gòu)強度采用 Kearns-f 因子進行定量描述。
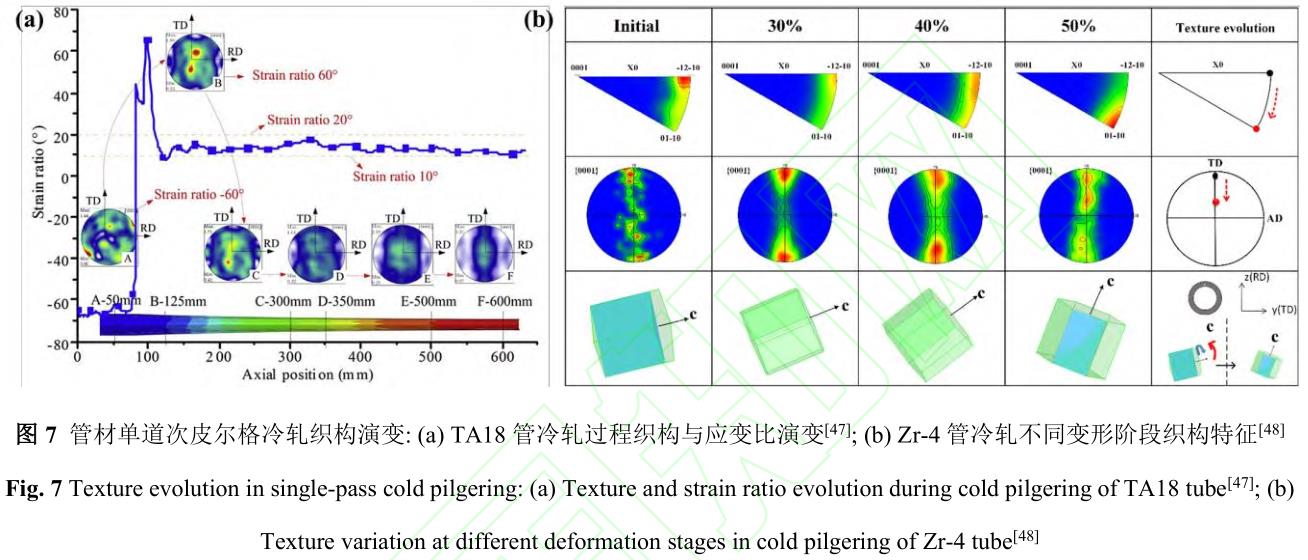
Wu 等[50]采用 EBSD 手段對不同 Ti-2Al-2.5Zr 鈦管軋制過程不同變形階段微觀織構(gòu)演變進行了表征分析,結(jié)果表明柱面滑移和{10-12}孿晶是最容易激活的兩種變形機制,同時{10-12}孿晶的產(chǎn)生使得晶粒在軸向上的位向從<10-10>轉(zhuǎn)向<11-20>。
上述研究均以管材某一層的織構(gòu)作為反映管材整體織構(gòu)分布的指標,并未考慮軋制過程管材沿壁厚方向顯著不均勻變形及梯度織構(gòu)分布特征。魏棟等[51]以不銹鋼管冷軋過程為對象,基于有限元模擬分析了管材冷軋過程內(nèi)外側(cè)變形演變特征,結(jié)果表明冷軋不同階段管材壁厚方向內(nèi)外側(cè)均表現(xiàn)出明顯的變形程度差異。Kumar 等[52]結(jié)合實驗表征和有限元模擬,揭示了鋯合金管材冷軋過程微觀組織與織構(gòu)的梯度分布特征,同時表明管材壁厚不同位置的等效應(yīng)變的差異引起管材壁厚方向梯度組織和織構(gòu)形成的關(guān)鍵因素。Juarez 等
通過中子衍射和高能同步輻射 X 射線衍射的先進技術(shù)手段結(jié)合 VPSC 建模仿真,揭示了 Zircaloy-4 鋯合金管材軋制過程局部織構(gòu)演變規(guī)律與機理,如圖 8 所示,結(jié)果表明管材在軋制全過程中管材壁厚方向均呈現(xiàn)出顯著的梯度織構(gòu)分布特征,且靠近內(nèi)表面徑向織構(gòu)強度要明顯高于外表面處徑向織構(gòu)強度,并且<11-20>//軸向的纖維織構(gòu)得到增強同時晶粒 c 軸向管材徑向偏轉(zhuǎn)[53]。
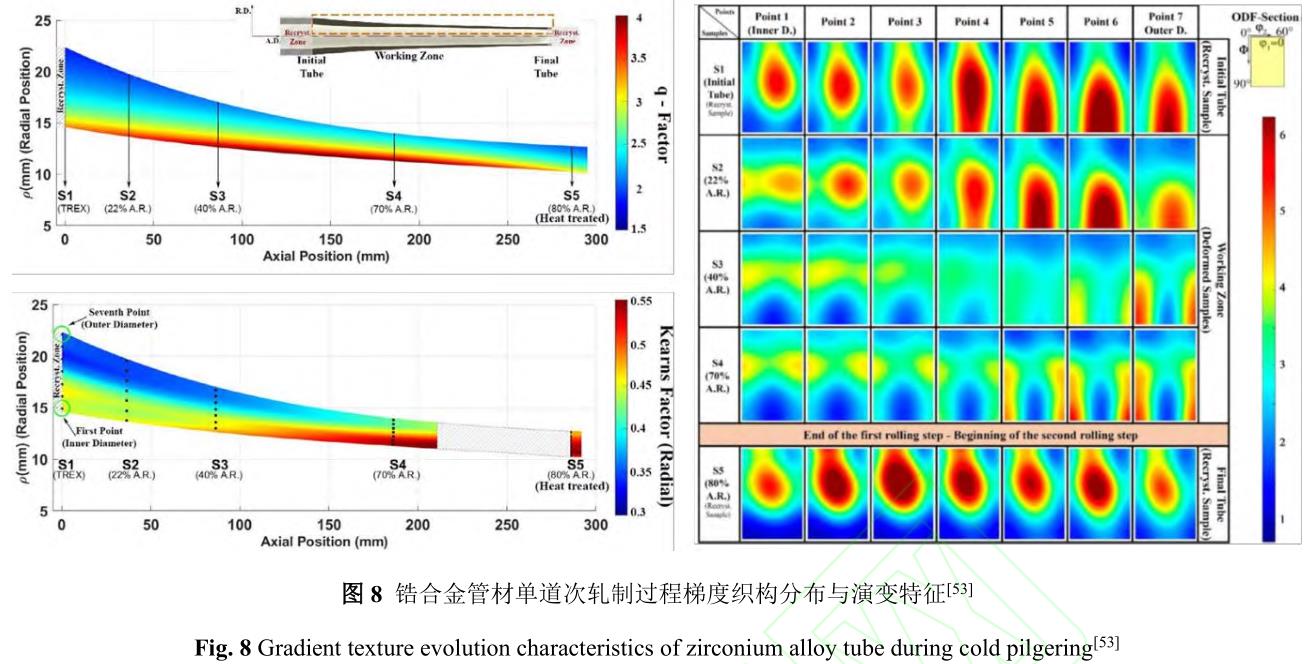
對于高強 TA18 等強度高且塑性相對較差的管材,往往需要進行多道次冷軋才能滿足尺寸要求。為了揭示多道次冷軋過程中管材織構(gòu)演變規(guī)律以及為織構(gòu)預(yù)測和調(diào)控提供理論依據(jù),Cook 等[54]以冷軋鋯合金管為對象,發(fā)現(xiàn)在對軋后管材織構(gòu)強度預(yù)測時,采用最后三道次的 Q 值的總和相比僅用最終道次的 Q 值在預(yù)測管材徑向織構(gòu)強度時更為準確。Saibaba[55]對比了三道次和二道次冷軋后鋯合金管材織構(gòu)強度,結(jié)果表明相比于三道次軋制,兩道次軋制時由于每道次具有更大的變形量和 Q 值,使得軋后管材具有更高的徑向織構(gòu)強度。Krishna 等[56]研究揭示了 Zr-4 管在三道次冷軋過程中的織構(gòu)演變,如圖 9(a)所示,研究結(jié)果還表明相對較大的晶粒的取向在冷軋和退火過程中對織構(gòu)演變的貢獻也相對更大。Mukherjee 等[57]和 Gurao 等[58]均針對 Zr-4 管兩道次冷軋過程中的織構(gòu)演變進行了表征,研究結(jié)果發(fā)現(xiàn)冷軋過程中產(chǎn)生的殘余應(yīng)力對滑移變形與織構(gòu)演變也具有一定的影響。Vakhitova 等[59]對比了 ODS 鋼管兩道次冷軋兩種工藝方案對管材織構(gòu)的影響,如圖 9(b)所示,結(jié)果表明,增加中間去應(yīng)力退火的方案最終管材<111>取向有一定增強,但晶粒細化效果不如無中間去應(yīng)力退火的方案。鄧偲瀛[60]通過對每道次初始管織構(gòu)進行測試,基于 VPSC 模型模擬了鋯管 3 道次和 4 道次冷軋過程織構(gòu)演變規(guī)律。此外大量學(xué)者對于 HCP 結(jié)構(gòu)金屬退火過程織構(gòu)演變進行了探究,結(jié)果表明再結(jié)晶退火并不能消除冷變形形成的織構(gòu),相反<10-10>和(0001)織構(gòu)由于晶粒定向形核和長大的原因,導(dǎo)致其在退火過程中得到強化,而再結(jié)晶退火過程中材料僅發(fā)生完全再結(jié)晶但晶粒并未明顯長大時,材料的織構(gòu)特別是{0001}取向強度變化不顯著[61-65]。
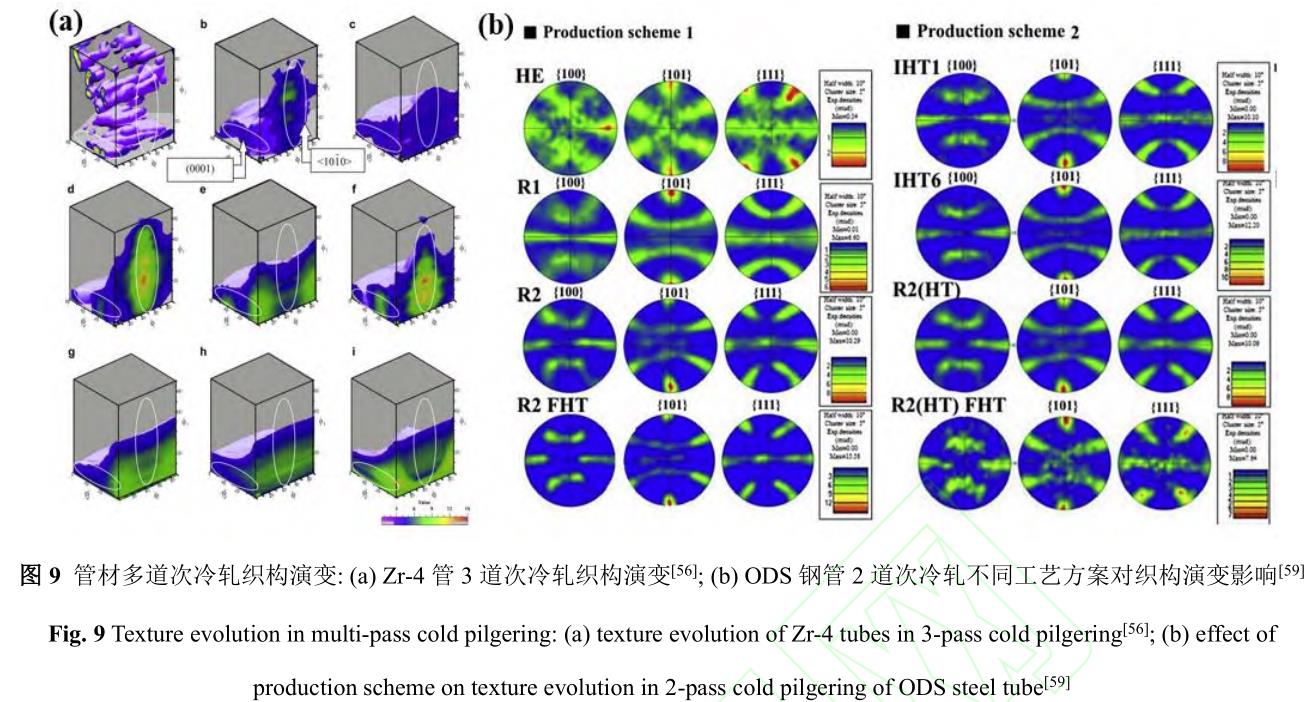
3.2 管材冷軋過程微觀織構(gòu)調(diào)控方法
針對管材冷軋過程微觀織構(gòu)調(diào)控,大量學(xué)者研究了成形參數(shù)對管材織構(gòu)的影響。其中,Q 值被廣泛認為是皮爾格冷軋過程中表征管材變形模式以及影響織構(gòu)演變最重要的指標,其表示管材相對減壁量與相對減徑量的比值。基于大量研究人員針對鋯合金、鈦合金等不同材料的管材皮爾格冷軋成形 Q 值對織構(gòu)演變的影響規(guī)律研究結(jié)果[66-69],如圖 10 所示,可以得出以初始隨機管材織構(gòu)為對象,當(dāng) Q>1 時,管材以減壁變形為主導(dǎo),冷軋過程中大部分晶粒 c 軸向管材徑向偏轉(zhuǎn)從而使管材呈現(xiàn)徑向織構(gòu),而當(dāng) Q<1 時,管材以減徑變形為主導(dǎo),大部分晶粒 c 軸向管材周向偏轉(zhuǎn)從而使管材呈現(xiàn)周向織構(gòu)。陳勝川等[70]通過研究不同 Q 值對小規(guī)格鋯管織構(gòu)和性能的影響,提出了 Q 值越大,晶粒纖維化和取向就越明顯,當(dāng) Q 值在 1.54~2.46 的范圍內(nèi),軋后管材具有良好的綜合性能。
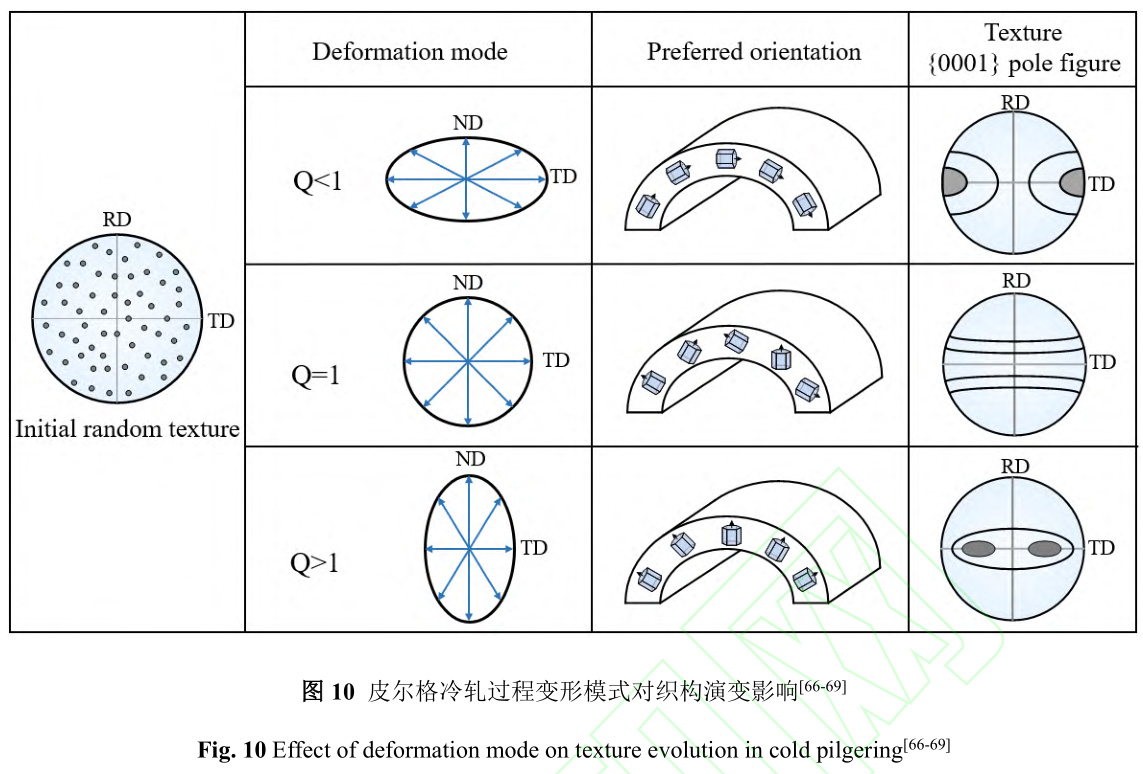
除變形模式之外,Girard 等[70]、廖強[72]和 Wang 等[73]以皮爾格冷軋 Zr-4 管、TA18 鈦管和 GH4145 管為研究對象,發(fā)現(xiàn)變形程度即冷軋變形量對管材織構(gòu)變化也具有重要影響。相比于軋制規(guī)格相關(guān)的整體變形模式與變形程度,由于皮爾格冷軋成形模具孔型的特殊性,其孔型設(shè)計對冷軋過程應(yīng)變路徑也具有顯著影響[74,75],進而引起管材織構(gòu)的波動。Zhang 等[76]以皮爾格冷軋鋯合金為對象,針對不同的孔型設(shè)計方案對冷軋過程管材變形行為、瞬時 Q 值以及應(yīng)變比 α 的變化進行了模擬分析,如圖 11(a)所示,結(jié)果表明孔型曲線的變化對冷軋過程瞬時 Q 值和應(yīng)變比 α 的演變具有顯著影響,進而會引起管材織構(gòu)的變化。Ubhi 等[77]通過改變減徑量和減壁量的分配設(shè)計了不同的孔型曲線,分析了 TA18 鈦管皮爾格冷軋織構(gòu)演變規(guī)律,如圖 11(b)所示,結(jié)果表明冷軋過程中可以通過改變模具設(shè)計來改變變形路徑以增加徑向織構(gòu)密度。Wei 等[39]結(jié)合仿真模擬和實驗研究闡明了初始織構(gòu)、變形模式 Q 值和截面變形量對微觀織構(gòu)演變的交互作用機制,如圖 12 所示,結(jié)果表明對于不同的初始織構(gòu)管材,隨著 Q 值與截面變形量的變化,拉伸孿晶 Tt 和錐面滑移 Py<c+a>激活程度的改變顯著影響冷軋過程中管材的晶粒轉(zhuǎn)動和取向變化;為提高軋后管材徑向織構(gòu)強度,Q 值和截面變形量存在對應(yīng)的閾值,且該閾值隨著初始管材 fND 值的升高不斷增大,同時建立了高強 TA18 鈦管冷軋成形參數(shù)與徑向織構(gòu)強度 Kearns-fND 值之間的定量關(guān)系,相比傳統(tǒng)僅考慮 Q 值和變形量影響的 Kearns-fND值預(yù)測公式,其多元非線性回歸結(jié)果 R 達到了 0.948。此外在多道次冷軋過程中,采用初始徑向織構(gòu)管坯以及 Q 值遞增的道次變形分配設(shè)計方案,更有利于成品管材徑向織構(gòu)強度的提高。
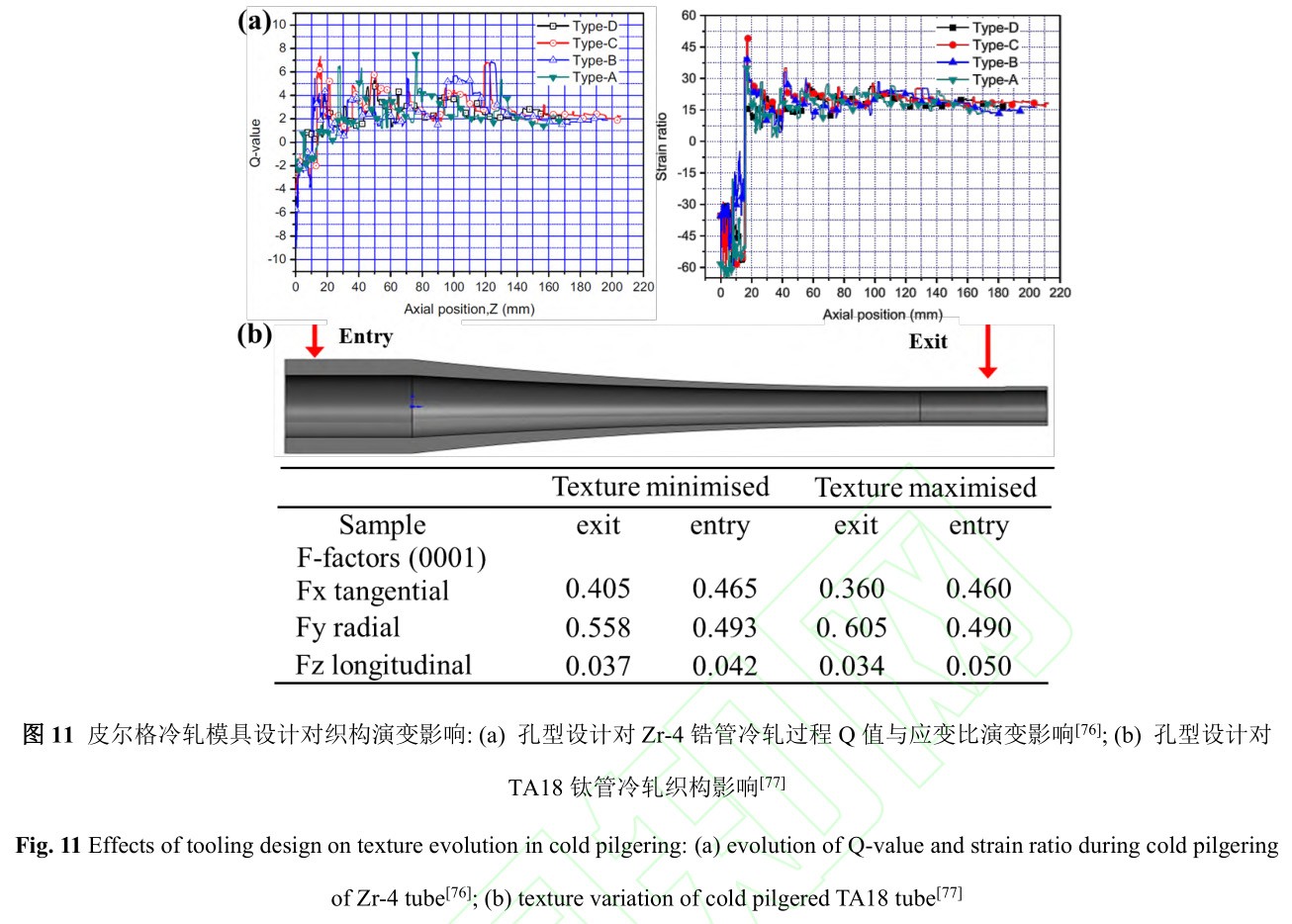
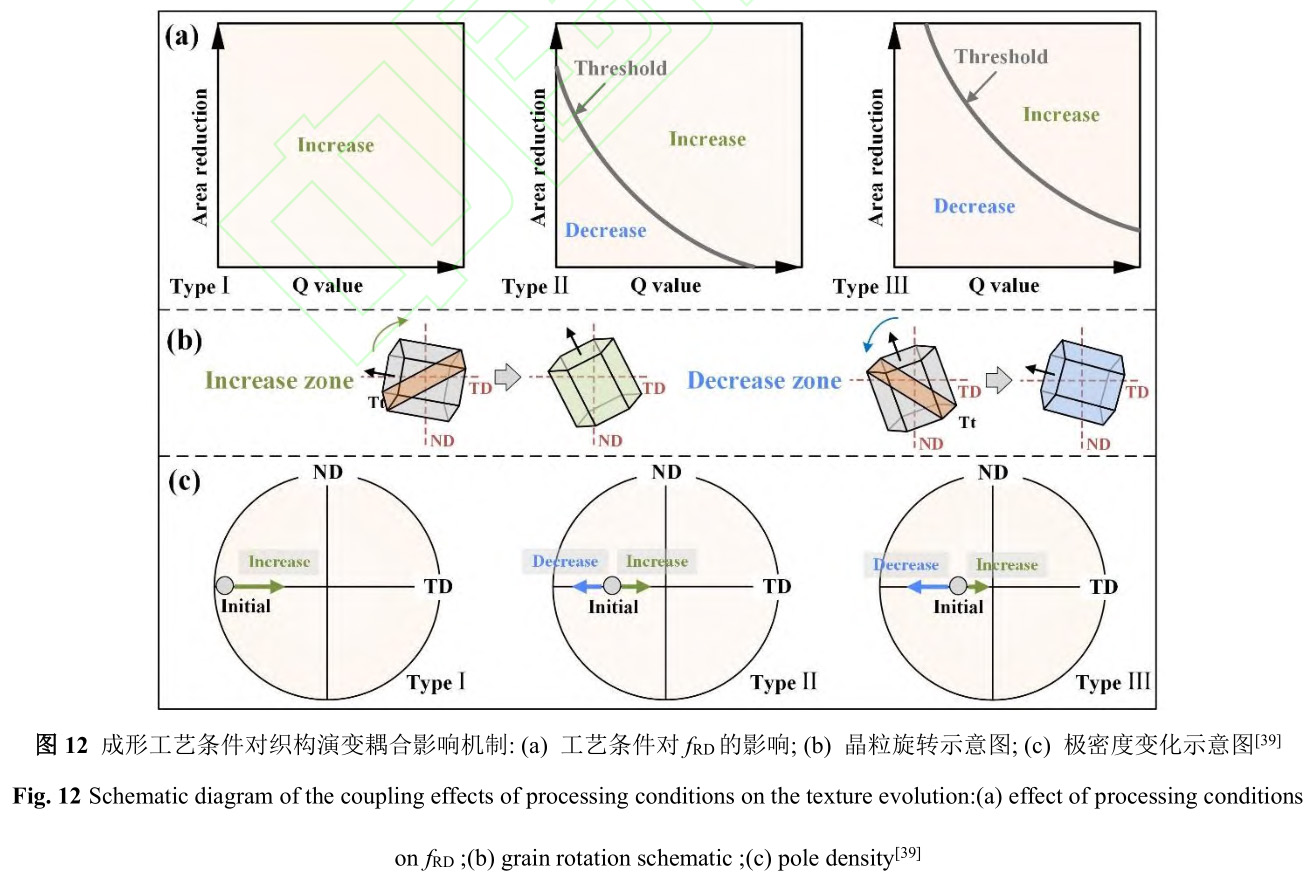
皮爾格冷軋后管材呈現(xiàn)出明顯的微觀織構(gòu)分布從而導(dǎo)致管材表現(xiàn)出顯著的各向異性,尤其對于密排六方(HCP)結(jié)構(gòu)材料,織構(gòu)對管材的后續(xù)成形性能和服役性能起著至關(guān)重要的作用[78, 79]。山特維克公司[80]對所生產(chǎn)的不同批次 TA18 管材進行了大量試驗,并采用 CSR 值作為表征管材織構(gòu)的指標,CSR>1.0 代表徑向織構(gòu),而 CSR<1.0 則代表周向織構(gòu)。He 等[81]以冷軋制備獲得的近 α 鈦合金管材為對象進行不同方向單向拉伸試驗,發(fā)現(xiàn)管材軋后微觀織構(gòu)分布顯著影響其在不同方向拉伸變形過程中各滑移機制的激活程度,進而導(dǎo)致管材表現(xiàn)出顯著的各向拉伸變形行為。張旺峰等[82]對具有不同微觀織構(gòu)和 CSR 值的高強 TA18 鈦管單向拉伸試驗測試分析,結(jié)果表明具有徑向織構(gòu)管材在變形過程中趨向于縮徑變形,而周向織構(gòu)管材變形以壁厚減薄為主,CSR 值的增大對于管材屈強比和延伸率的提高具有促進作用。Wang[83]等研究也發(fā)現(xiàn)對于近 α 鈦合金管材,徑向織構(gòu)強度的增強對于{10-10}<11-20>和{10-11}<11-20>滑移系 Schmid 因子的提升以及管材強度的增強起著至關(guān)重要的作用。此外,Wang 等[84]以具有初始周向微觀織構(gòu)分布特征的 Ti-2Al-2.5Zr鈦管為對象,對壓扁過程中管材不同變形區(qū)域復(fù)雜應(yīng)力狀態(tài)與變形行為進行了研究,并揭示了包括柱面和基面滑移以及拉伸孿晶在內(nèi)的變形機制。Choi 等[85]通過試驗發(fā)現(xiàn)鋯合金管的抗腐蝕性能也取決于管材的織構(gòu)分布情況,并且當(dāng)徑向織構(gòu)具有一定程度的增強時,管材的抗腐蝕性能也相應(yīng)的增強。此外,盛澤民等[86]利用 XRD 技術(shù)對軋制鈦合金管材沿壁厚方向不同位置的微觀織構(gòu)進行了定量表征,結(jié)果表明軋后管材微觀織構(gòu)強度沿壁厚方向呈現(xiàn)出較為顯著的梯度變化特征,并且非理想周向織構(gòu)強度分布比例的增大將引起管材 CSR 值的下降。Li 等[87]結(jié)合試驗與數(shù)值模擬,對比分析了高強 TA18 鈦管不同微觀織構(gòu)分布特征對數(shù)控彎曲成形質(zhì)量的影響,如圖 13 所示,結(jié)果表明具有雙峰織構(gòu)分布特征的管材相比于近徑向織構(gòu)和近周向織構(gòu),包括壁厚減薄、截面畸變以及回彈在內(nèi)的彎曲成形指標均更為優(yōu)異。
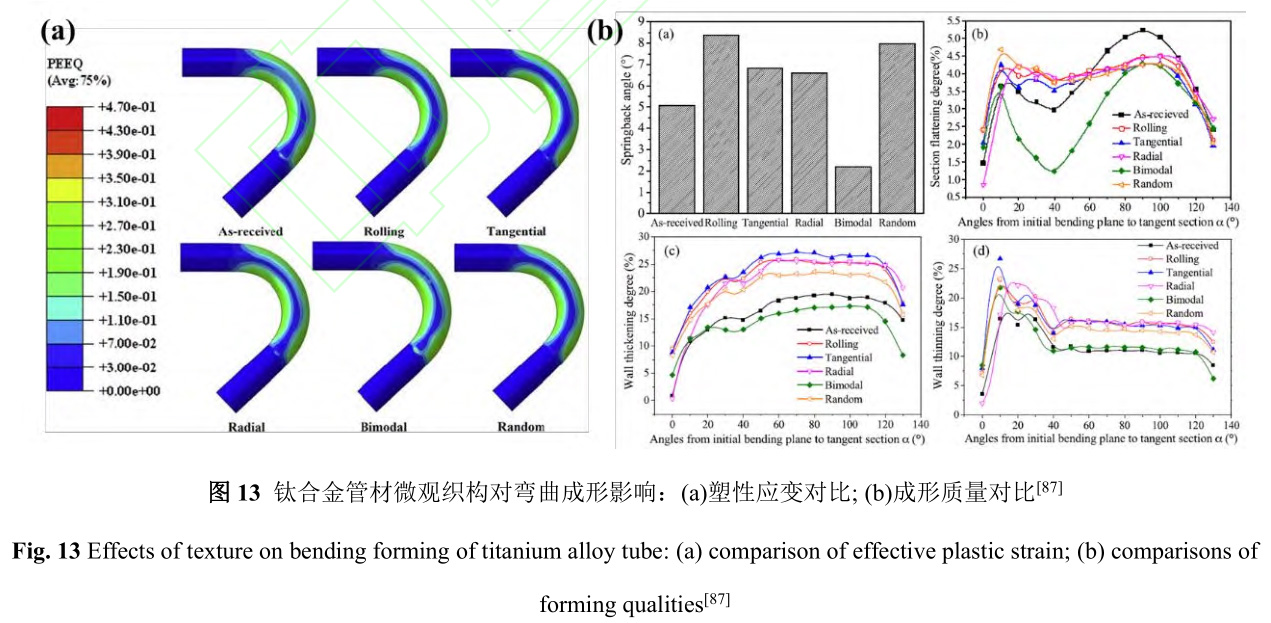
4、 結(jié)語與展望
高性能管材冷軋全過程復(fù)雜的外部加載路徑、管材非線性力學(xué)響應(yīng)以及顯著的不均勻變形導(dǎo)致了管材微觀織構(gòu)演變規(guī)律復(fù)雜、難以精確控制,進而嚴重影響管材性能。目前針對高性能管材皮爾格冷軋成形過程微觀織構(gòu)預(yù)測建模、演變機制及調(diào)控方法等方面,國內(nèi)外學(xué)者和相關(guān)企業(yè)已取得了重要的進展和成果。其中,基于有限元模型和晶體塑性模型的單道次冷軋宏細觀數(shù)值模擬已取得了長足的發(fā)展,并且計算效率和預(yù)測精度也在隨著模型的改進不斷提高。此外,在先進數(shù)值模擬方法及試驗表征手段快速發(fā)展的有利加持下,對管材冷軋全過程不均勻變形行為及整體微觀織構(gòu)演變規(guī)律與機制也有了更深入和準確的認識。在此基礎(chǔ)上,明晰了管材冷軋過程包括初始織構(gòu)、Q 值、變形量、孔型參數(shù)及退火溫度等對微觀織構(gòu)演變的耦合作用規(guī)律,建立了有效的微觀織構(gòu)調(diào)控方法。但仍然存在一定的局限性和不足,面臨以下問題需要解決:
(1) 目前關(guān)于管材冷軋成形宏觀變形特征和微觀織構(gòu)演變數(shù)值預(yù)測模型主要針對于單道次冷軋過程,建立能夠準確預(yù)測管材多道次冷軋全過程的宏細觀數(shù)值模型,有望為深入探究冷軋全過程微觀織構(gòu)演變機制及其調(diào)控方法提供重要的定量分析手段。
(2) 當(dāng)前對于管材冷軋過程織構(gòu)演變與調(diào)控的研究主要考慮的是管材整體織構(gòu)分布特征和強度,而冷軋過程中局部加載下壁厚方向顯著不均勻變形誘導(dǎo)的變形機制的差別勢必會引起梯度織構(gòu)的形成,進一步明晰多道次冷軋中梯度織構(gòu)的形成與演變機制,是實現(xiàn)織構(gòu)與性能穩(wěn)定控制的基礎(chǔ)。
(3) 微觀織構(gòu)是引起管材各向異性和拉壓非對稱性力學(xué)行為差異的關(guān)鍵因素,進而影響管材的力學(xué)性能、后續(xù)成形性能及疲勞服役等性能。面向管材綜合性能協(xié)同提升目標,闡明微觀織構(gòu)對管材性能影響并建立關(guān)聯(lián)關(guān)系,為微觀織構(gòu)調(diào)控提供基礎(chǔ)和依據(jù)對突破管材全流程形性一體化設(shè)計制造瓶頸具有重要意義。
參考文獻
1 Cao C X. Rare Metals Letters, 2006, 25, 17-21. (in Chinese).
曹春曉. 稀有金屬快報, 2006, 25, 17-21.
2 Li Y, Zhao Y Q, Zeng W D. Materials Reports, 2020, 34(S1), 28-282.
李毅, 趙永慶, 曾衛(wèi)東. 材料導(dǎo)報, 2020, 34(S1), 28-282.
3 Zhang W F, Li Y, Wang Y H, et al. Materials Reports, 2011, 25(23), 133-137.
張旺峰, 李艷, 王玉會, 等. 材料導(dǎo)報, 2011, 25(23), 133-137.
4 Yang H, Li H, M J, et al. International Journal of Machine Tools and Manufacture, 2021, 166, 103742.
5 Furugen M, Hayashi C. Journal of Mechanical Working Technology, 1984, 10, 273-286.
6 Stinnertz H. Tube Pipe Technologies, 1988, 2, 27-31.
7 Ragger K S, Primig S, Daniel R, et al. Materials Characterization, 2017, 128: 257-268.
8 H. Abe, T. Nomura, Y. Kubota. Journal of Materials Processing Technology, 2014, 214, 1627-1637.
9 Wei D, Chen Y Y, Li H, et al. International Journal of Mechanical Science, 2022, 225, 107366.
10 Musazadeh M H, Vafaei R, Sharifi E M, et al. Metallurgical and Materials Transactions B, 2018, 49, 3030-3042.
11 Meredith S E, Schemel J H. International Journal of Fatigue, 1990. 12, 528-528.
12 Deng S Y, Wang S W, Chen S F, et al. Journal of Nuclear Materials, 2024, 589, 154846.
13 Li H, Fu M W. Elsevier, 2019, 307-311.
14 Hsiang S, Lin Y W. Journal of Materials Processing Technology, 2007, 192-193, 292-299.
15 Liu F, Chen C, Niu J, et al. Materials Science and Engineering C, 2015, 48, 400-407.
16 Chu Z B, Wei D, Jiang L Y, et al. Journal of Iron Steel Research International, 2018, 25, 398-408.
17 Chu Z B, Xue Z Y, Zhang D, et al. Journal of Iron Steel Research International, 2019, 26, 593-601.
18 Huml P, Fogelholm R. Journal of Materials Processing Technology, 1994, 42, 167-173.
19 Pociecha D, Boryczko B, Osika J, et al. Archives of Civil and Mechanical Engineering, 2014, 14, 376-382.
20 Liu J L, Zeng W D, Du Z L, et al. Titanium Industry Progress, 2015, 32, 21-25. (in Chinese).
劉江林, 曾衛(wèi)東, 杜子龍, 等. 鈦工業(yè)進展, 2015, 32, 21-25.
21 Mulot S, Hacquin A, Montmitonnet P, et al. Journal of Materials Processing Technology, 1996, 60, 505-512.
22 Montmitonnet P, Logé R, Hamery M, et al. Journal of Materials Processing Technology, 2002, 125, 814-820.
23 Huang L, Xu Z, Dai C, et al. Rare Metal Materials and Engineering, 2013, 42, 524-529.
黃亮, 徐哲, 代春, 等. 稀有金屬材料與工程, 2013, 42, 524-529.
24 Chu Z B, Lv Y Y. Huang Q X, et al. Journal of Sichuan University (Engineering Science Edition), 2015, 47,165-171. (in Chinese).
楚志兵, 呂陽陽, 黃慶學(xué), 等. 四川大學(xué)學(xué)報(工程科學(xué)版), 2015, 47, 165-171.
25 Lodej B, Niang K, Montmitonnet P, et al. Journal of Materials Processing Technology, 2006, 177, 188-191.
26 Strickner G, Ragger K S, Hatzenbichler T, et al. Steel Research International, 2012, 71-74.
27 Deng S, Song H, Zheng C, et al. International Journal of Material Forming, 2019, 12, 321-329.
28 Azizoglu Y, Gardsback M, Sjoberg B, et al. International Conference on the Technology of Plasticity, UK, 2017,2370-2375.
29 Azizoglu Y, Sjoberg B, Lindgren L. Journal of Manufacturing Processes, 2024, 112, 112-125.
30 Chung S H, Jeong S W, Chung W J, et al. Journal of Manufacturing Processes, 2023, 95, 217-228.
31 Molinari A, Canova G R, Ahzi S. Acta Metallurgica, 1987, 35, 2983-2994.
32 Lebensohn R A, Tome C N. Acta Metallurgica et Materialia, 1993, 41, 2611-2624.
33 Knezevic M, Lebensohn R A, Cazacu O, et al. Materials Science and Engineering A, 2013, 564, 116-126.
34 Zhang H, Sheng Z M, Zhang W F, et al. Journal of Materials Engineering and Performance, 2015, 24, 2312-2318.
35 Gupta A, Khatirkar R K, Dandekar T, et al. Journal of Alloys and Compounds, 2021, 850, 156824.
36 Lebensohn R A. González M I, Tomé C N. et al. Journal of Nuclear Materials, 1996, 229, 57-64.
37 Zhang H Q. Master’s thesis, Northwestern Polytechnical University, 2015. (in Chinese).
張海芹. 碩士學(xué)位論文, 西北工業(yè)大學(xué), 2015.
38 Li H, Wei D, Zhang H Q, et al. Journal of Materials Processing Technology, 2020, 279: 116520.
39 Wei D, Chen Y Y, Yang H, et al. Journal of Alloys and Compounds, 2024, 997:174835.
40 Kaushik L, Kim M S, Singh J, et al. International Journal of Plasticity, 2021, 141, 102989.
41 Yang H, Li H, Ma J, et al. International Journal of Plasticity, 2020. 127, 102650.
42 Deng S, Song H, Liu H, et al. International Journal of Solids and Structures, 2021, 213, 63-76.
43 Wei D. P.h.D. Thesis, Northwestern Polytechnical University, 2022. (in Chinese).
魏棟. 博士學(xué)位論文, 西北工業(yè)大學(xué), 2022.
44 Chu Z B, Wei D. Yang Y L, et al. Chinese Journal of Engineering, 2017, 39(5), 747-755. (in Chinese).
楚志兵, 魏棟, 楊彥龍, 等. 工程科學(xué)學(xué)報, 2017, 39(5), 747-755.
45 Abe H, Furugen M. Journal of Materials Processing Technology, 2012, 210, 1687-1693.
46 Singh J, Mahesh S, Kumar G, et al. Metallurgical and Materials Transactions A, 2015, 46, 1927-1947.
47 Li H, Zhang H Q, Yang H, et al. International Journal of Plasticity, 2017, 90, 177-211.
48 Deng S, Song H, Zheng C, et al. Materials Science and Engineering A, 2019, 764: 138280.
49 Davies R W, Khaleel M A, Kinsel W C, et al. Journal of Engineering Materials and Technology, 2002, 124,125-134.
50 Wu J, Wang L, Liu X, et al. Rare Metal Materials and Engineering, 2022, 51(04), 1145-1151.
51 Wei D, Chu Z B, Huang Q X, et al. Journal of Plasticity Engineering, 2016, 23(5), 89-95. (in Chinese).
魏棟, 楚志兵, 黃慶學(xué), 等. 塑性工程學(xué)報, 2016, 23(5), 89-95.
52 Kumar G, Balo S, Dhoble A, et al. Metallurgical and Materials Transactions A, 2017, 48, 2844-2857.
53 Juarez G, Alvarez M A V, Santisteban J, et al. Journal of Nuclear Materials, 2022, 558, 153382.
54 Cook C S, Sabol G P, Sekera K P, et al. ASTM International, 1991, 80-98.
55 Saibaba N. Journal of Nuclear Materials, 2008, 383, 63-70.
56 Krishna K V M, Sahoo S K , Samajdar I, et al. Journal of Nuclear Materials, 2008, 383, 78-85.
57 Mukherjee P, Gayathri N, Chowdhury P S, et al. Journal of Nuclear Materials, 2013, 434, 24-30.
58 Gurao N P, Akhiani H, Szpunar J A. Journal of Nuclear Materials, 2014, 453, 158-168.
59 Vakhitova E, Sornin D, Barcelo F, et al. Journal of Nuclear Materials, 2017, 494, 20-28.
60 Deng S Y. P.h.D. Thesis, University of Science and Technology of China, 2020. (in Chinese).
鄧偲瀛. 博士學(xué)位論文, 中國科學(xué)技術(shù)大學(xué), 2020.
61 Haq A J, Banerjee S. Bulletin of Materials Science, 1992, 15: 289-296.
62 Zhu K Y, Chaubet D, Bacroix B, et al. Acta Materialia, 2005, 53(19), 5131-5140.
63 Gerspach F, Bozzolo N, Wagner F. Scripta Materialia, 2009, 60, 203-206.
64 Liu C, Li G, Chu L, et al. Materials Science and Engineering A, 2018, 719, 147-154.
65 Wang Y, He W, Liu N, et al. Materials Characterization, 2018, 136, 1-11.
66 Murty K L, Charit I. Progress in Nuclear Energy, 2006, 48: 325-359.
67 Hong Q, Qi L Y, Zhao B, et al. Titanium Industry Progress, 2016, 33, 16-19. (in Chinese).
洪權(quán), 戚運蓮, 趙彬, 等. 鈦工業(yè)進展, 2016, 33, 16-19.
68 Singh J, Mahesh S, Roy S, et al. Journal of Materials Processing Technology, 2016, 237, 126-138.
69 Yang Q, Hui S, Ye W, et al. Materials. 2022, 15, 817.
70 Chen S C, Zhu B H, Yuan H J, et al. Titanium Industry Progress, 2016, 33: 25-29. (in Chinese).
陳勝川, 朱寶輝, 袁紅軍, 等. 鈦工業(yè)進展, 2016, 33: 25-29.
71 Girard E, Guillen R, Weisbecker P, et al. Journal of Nuclear Materials, 2001, 294, 330-338.
72 Liao Q, Qu H L, Yang Y S, et al. Titanium Industry Progress, 2012, 29, 26-28. (in Chinese).
廖強, 曲恒磊, 楊亞社, 等. 鈦工業(yè)進展, 2012, 29, 26-28.
73 Wang L, Liu J, Wang Z, et al. Materials Science and Engineering A, 2022, 832, 142464.
74 Lee S K, Lee K H. Applied Science, 2021, 11, 11265.
75 Wang Q, Huang P, Yin Y. The International Journal of Advanced Manufacturing Technology, 2021, 112, 803-818.
76 Zhang H Q, Wang X F, Wei B L, et al. The International Journal of Advanced Manufacturing Technology, 2017,92, 2169-2183.
77 Ubhi H S, Houghton A, Saithala J. Materials Science Forum, 2011, 702-703, 643-646.
78 Toualbi L, Cayron C, Olier P, et al. Journal of Nuclear Materials, 2013, 442, 410-416.
79 Guo W, Li G, Han F, et al. International Journal of Fatigue. 2022, 163, 107046.
80 Forney C E, Meredith S E. Sandvik Special Metals, 1990, 25-38.
81 He S, Zeng W, Zhao Z, et al. Journal of Alloys and Compounds. 2022, 909, 164785.
82 Zhang W F, Zhang H, Yan M Q, et al. Titanium Industry Progress, 2018, 35: 22-25. (in Chinese).
張旺峰, 張暉, 顏孟奇, 等. 鈦工業(yè)進展, 2018, 35: 22-25.
83 Wang W R, Yuan L H, Zhang H, et al. Journal of Alloys and Compounds, 2023, 931, 167558.
84 Wang S, Jin G, Wu Y, et al. Journal of Materials Science and Technology. 2021, 90,108-120.
85 Choi Y, Shin E J, Inoue H. Physica B. 2006, 385-386, 529-531.
86 Sheng Z M, Zhang H, Zhang W F, et al. Rare Metal Materials and Engineering, 2017, 46(10), 3073-3076. (in Chinese).
盛澤民, 張暉, 張旺峰, 等. 稀有金屬材料與工程, 2017, 46(10), 3073-3076.
87 Li H, Hu X, Yang H, et al. International Journal of Plasticity, 2016, 82, 127-158.
相關(guān)鏈接