材料、能源、和信息技術(shù)被譽為現(xiàn)代科學(xué)技術(shù)的三大支柱,尤其是材料科學(xué)技術(shù),其發(fā)展更是得到了廣泛的高度關(guān)注。世界各工業(yè)發(fā)達(dá)國家都十分重視材料技術(shù)的發(fā)展,尤其是先進(jìn)材料的研宄與發(fā)展。而薄膜材料因其獨有的特性在工業(yè)生產(chǎn)各個方面都起到至關(guān)重要的作用。薄膜技術(shù)起始于17世紀(jì),現(xiàn)已成為現(xiàn)代材料科學(xué)的一個重要組成部分。薄膜是在機械鎖和、化學(xué)吸附、物理吸附和擴散結(jié)合等因素綜合的作用下才能夠附著在基體上。目前使用較為廣泛的薄膜制備技術(shù)有很多類別,包括氣相生長法、液相生長法、外延生長法、氧化法、擴散與涂布法、電鍍法、濺射法等等。近年來,薄膜技術(shù)已經(jīng)滲透到現(xiàn)代科學(xué)技術(shù)和國民經(jīng)濟(jì)發(fā)展的多個重要領(lǐng)域,包括但不限于航天航空、光學(xué)、能源、交通、通信等領(lǐng)域。此外,在高新技術(shù)產(chǎn)業(yè),薄膜材料和技術(shù)也占據(jù)其獨有的重要地位,例如在電子技術(shù)、集成光學(xué)、激光技術(shù)、紅外技術(shù)、航天技術(shù)以及光學(xué)儀器等多個領(lǐng)域都得到了廣泛的開發(fā)和應(yīng)用。
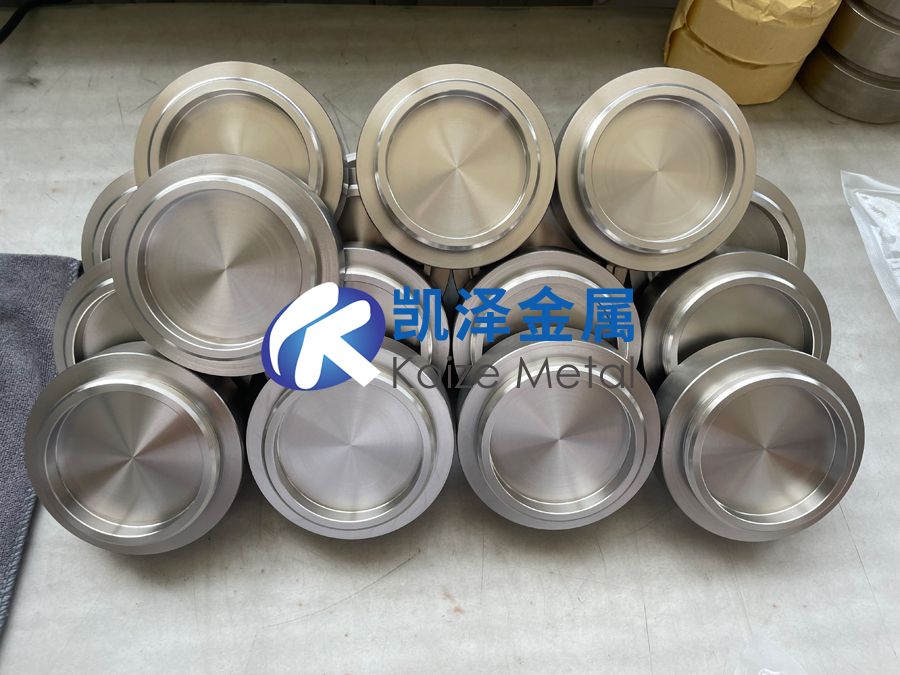
金屬鉬具有高熔點,高的高溫強度、硬度及剛度,優(yōu)良的導(dǎo)熱導(dǎo)電性以及抗熱震性等優(yōu)異的性能,因而已經(jīng)在機械工業(yè)、制造業(yè)、國防工業(yè)以及交通業(yè)等方面得到了廣泛的應(yīng)用。Mo層狀材料的具有可調(diào)節(jié)的熱膨脹系數(shù)和彈性模量,因而在薄膜領(lǐng)域的應(yīng)用較多。Mo薄膜也因具有良好的導(dǎo)電性、穩(wěn)定性和高紅外反射率而被廣泛用于太陽能薄膜電池的背電極材料,液晶顯示器薄膜晶體管的電極、或布線材料,以及太陽能選擇性吸收涂層;Mo薄膜在集成電路中可作低電阻布線材料,與傳統(tǒng)A1薄膜相比,其老化速率明顯降低,使用壽命更長;磁控濺射法沉積制備Mo薄膜也常常被作為散射層材料,在激光等離子體技術(shù)中起到了很大的作用;磁控濺射Mo薄膜也可以做結(jié)構(gòu)良好且活化能較低,整體比較穩(wěn)定的納米級含能薄膜。采用合理的工藝在鉬中摻雜金屬氧化物,進(jìn)而得到的金屬合金化薄膜具有表面光滑,晶粒細(xì)小,抗拉強度較高等特點。此外,在銅基底上鍍覆Mo薄膜可以作為導(dǎo)電率較高的梯度材料。目前,Mo在顯示領(lǐng)域應(yīng)用廣泛,而且和氧化物半導(dǎo)體的接觸良好,平面顯示器的薄膜多采用濺射成形,Mo薄膜已成為其中使用最為廣泛的電極材料,Mo薄膜的應(yīng)用不僅能夠提高液晶顯示屏的清晰度和對比度,而且能夠在很大程度上延長其使用周期。寧洪龍等制備了具有Cu-Mo結(jié)構(gòu)源漏電極的薄膜晶體管,Mo接觸層不僅能夠有效抑制Cu與有源層之間的擴散,而且有助于提高Cu電極與玻璃基底以及柵極絕緣層之間的結(jié)合強度。
1、薄膜制備技術(shù)
薄膜制備技術(shù)具有多種類別,主要包括以物理氣相沉積和化學(xué)氣相沉積為代表的氣相沉積法,以軋制和機械研磨拋光為代表的機械方法,以離子束刻蝕為代表的微細(xì)加工技術(shù),以真空蒸鍍?yōu)榇淼恼翦兎椒ǖ鹊取?/p>
1.1軋制
軋制方法是指金屬材料在上下轉(zhuǎn)動的柱狀軋輥之間通過,以此來不斷降低材料厚度,是利用金屬良好的延伸性和塑性變形性而獲得所需要薄膜材料的方法。
軋制前后材料的密度和化學(xué)成分均保持不變,是制備金屬薄膜常用的一種簡單高效的方法。軋制法制備的薄膜其優(yōu)點在于薄膜具有較高的密度和硬度。但是軋制法制得的薄膜中存在大量的缺陷,例如位錯、織構(gòu)取向、冷作硬化層等,此外,薄膜的表面粗糙度也略高。
1.2機械研磨拋光
機械研磨拋光法其實質(zhì)在于通過試樣表面與磨料和拋光細(xì)粉之間的相互滑動或滾動以達(dá)到減薄與拋光目的的方法,其優(yōu)點在于加工前后試樣的密度保持不變,薄膜表面粗糙度較低,加工精度較高。但是機械研磨拋光制備的薄膜厚度一致性較差,容易出現(xiàn)成分污染和表面硬化,其厚度難以小于10^m,因而有一定的局限性。
1.3化學(xué)氣相沉積法
化學(xué)氣相沉積是指氣體通過化學(xué)反應(yīng)在基底表面形成薄膜?;瘜W(xué)氣相沉積包括化學(xué)合成反應(yīng)和熱分解反應(yīng)兩種類型大多數(shù)化學(xué)沉積過程中都可能有兩種或兩種以上氣態(tài)反應(yīng)物在基片上發(fā)生反應(yīng);而熱分解反應(yīng)一般在有惰性氣體的保護(hù)或者在真空中,將基片加熱到所需的溫度,則反應(yīng)物氣體會發(fā)生熱分解,最后在基底的表面形成一層需要的薄膜。
化學(xué)氣相沉積法能夠制備的薄膜種類多,且薄膜的沉積速度也較快。此外,反應(yīng)前驅(qū)體良好的繞射性使薄膜能夠均勻覆蓋復(fù)雜形狀的表面、工件的細(xì)孔和深孔等。該方法制得的薄膜純度高、致密性好、表面光滑、薄膜的結(jié)晶性能良好、殘余應(yīng)力較小。但化學(xué)氣相沉積法制備薄膜反應(yīng)溫度較高,限制了對基底材料的選擇,而且采用該方法沉積的薄膜質(zhì)量不如物理氣相沉積的薄膜質(zhì)量高。
1.4離子鍍與離子束沉積法
離子束沉積是由DMMattox于1963年提出的,將離子束引入真空室中,進(jìn)而借助離子束的轟擊濺射出靶材原子,進(jìn)而沉積在基底上的過程。離子束濺射方法的優(yōu)點在于其制備薄膜的純度較高,且工作過程中基底溫升小,離子束的能量和方向是能夠被控制的。此外,離子束濺射中的靶材和基底都是可以根據(jù)需要任意選擇的,能夠在金屬和非金屬基底上獲得多種化合物薄膜。
但離子束濺射沉積的裝置復(fù)雜,薄膜沉積速率較低,不適用于大面積連續(xù)沉積薄膜。且離子束濺射過程中局部靶材會因高溫熔化產(chǎn)生小液滴,于膜層處生成大顆粒,薄膜表面較為粗糙。
1.5真空蒸鍍法
真空蒸鍍是指將裝有基底的真空室抽成真空,并使真空室的氣體壓強達(dá)到10-3Pa以下后采用不同的蒸發(fā)源加熱待蒸發(fā)材料,使得待蒸發(fā)材料表面的原子或者分子蒸發(fā)出來,形成蒸發(fā)氣流,最后沉積到基底表面凝固成薄膜。真空蒸發(fā)鍍膜成膜速度快,但膜基結(jié)合力較小。
目前比較常用的真空蒸鍍方法是電子束蒸發(fā)鍍膜法。其原理是電子在電場的加速下,獲得足夠大的能量轟擊到陽極的待蒸發(fā)靶材上,電子的動能轉(zhuǎn)化為靶材的熱能,蒸發(fā)材料獲得足夠能量后開始熔化進(jìn)而被蒸發(fā),最終沉積在基底薄膜形成純度較高的薄膜,能夠解決普通蒸發(fā)鍍膜法中沉積速率低、不容易控制加熱溫度的缺陷,但是采用電子束蒸發(fā)鍍膜法制備的薄膜致密度不夠高,且蒸發(fā)過程中會產(chǎn)生一定的熱輻射等等,這些不足之處均阻礙電子束蒸發(fā)技術(shù)發(fā)展。
1.6濺射鍍膜法
濺射過程是指帶有較高動能的粒子轟擊固體材料,材料表面的原子或分子能夠獲得足夠高的動能進(jìn)而脫離固體的束縛逸出到氣相中。而濺射鍍膜法就是把濺射到氣相中的材料收集起來,并使之沉積成膜。濺射鍍膜過程中靶材無相變,化合物的成分不容易發(fā)生變化。濺射原子能量高,沉積在基底處與基板發(fā)生能量轉(zhuǎn)換而產(chǎn)生熱量使膜與基板附著力好。濺射時基底處于等離子區(qū),附著不牢的沉積原子會被清洗,因此基底會得到凈化及活化。且濺射鍍膜的膜厚可控性和重復(fù)性好。因此,濺射鍍膜法在實際制備薄膜的過程中得到廣泛的應(yīng)用。
磁控濺射鍍膜法則是以二極濺射為基礎(chǔ)發(fā)展起來的,磁控濺射本質(zhì)上是在磁場和電場共同作用模式下的二極濺射,現(xiàn)已成為目前鍍膜工業(yè)生產(chǎn)中常用的主要方法之一。磁場可以使靶材附近區(qū)域更多的粒子發(fā)生電離,也可以約束電離后的粒子按照一定的軌跡運動,從而使得濺射鍍膜的效率大大提高。與其它薄膜制備技術(shù)相比較,磁控濺射鍍膜法的優(yōu)點在于其沉積速度快、對于基底溫度的要求較低,而且能夠濺射非金屬材料、進(jìn)而制備出性能不同的薄膜,具有非??捎^的發(fā)展前景。
濺射靶材在我國是一個較新的行業(yè),濺射靶材在技術(shù)及市場方面都取得了明顯的進(jìn)步。我國鍍膜研宄于20世紀(jì)60年代開始起步,在國家各相關(guān)部門均大力地支持下,鍍膜技術(shù)及鍍膜材料的開發(fā)與研宄得到了快速發(fā)展;近年來,我國已成功開發(fā)出應(yīng)用于不同領(lǐng)域的靶材,靶材的研發(fā)與發(fā)展已經(jīng)逐漸形成體系,并朝著產(chǎn)業(yè)化的方向快速發(fā)展。
此外,直流磁控濺射法和脈沖磁控濺射法制備的薄膜各有其優(yōu)異性。就Mo薄膜而言,采用直流磁控濺射法沉積制備Mo薄膜的沉積速率更快,薄膜的導(dǎo)電性更好,但是其反射率略有一點點不足,但與脈沖磁控濺射法制備Mo薄膜的光學(xué)反射率差異不是特別明顯。鑒于此,直流磁控濺射法已經(jīng)成為較為常用的制備Mo薄膜的方法。
2、直流磁控濺射法制備Mo薄膜的研究
近年來,以磁控濺射技術(shù)制備的Mo薄膜已廣泛地應(yīng)用于光學(xué),材料,半導(dǎo)體以及電子技術(shù)等各個領(lǐng)域。Mo薄膜是Cu(In,Ga)Se2太陽能電池結(jié)構(gòu)中最常用的背電極材料,Mo薄膜作為背接觸層不僅能夠與上層的光吸收層形成良好的歐姆接觸,還能夠在很大程度上阻礙鈉鈣玻璃基底中Na+向吸收層擴散。此外,Mo薄膜的表面形貌對其上沉積Cu膜等膜層的組織結(jié)構(gòu)和整個薄膜器件的性能有著直接的影響。此外,最原始的液晶顯示器中薄膜晶體管的柵電極材料多為Cr/Al,而相較于Cr薄膜,Mo薄膜的比阻抗和膜應(yīng)力均較小,且對環(huán)境的危害性較低,鑒于此,Mo薄膜替代Cr成為新一代的電極材料具有其獨有的優(yōu)勢。
采用磁控濺射沉積法制備Mo薄膜時薄膜的沉積速率大、均勻性好,尤其在對于制備大面積薄膜時其優(yōu)勢更加顯著。但是其濺射工藝參數(shù)對沉積薄膜的相結(jié)構(gòu)、微觀形貌及性能均有較大影響。其中在磁控濺射制備薄膜過程中影響較大的工藝參數(shù)主要有基底表面附著物及溫度、工作時間、工作氣壓、濺射功率、靶基距及后續(xù)熱處理等等。
2.1基底
沉積薄膜前需要對基底進(jìn)行徹底清潔,盡量減少基底表面污染物的種類和數(shù)量,最大程度地確?;妆砻娴臐崈舳取F渲饕蛟谟诨妆砻嫔细街?、氧化層等污染物的存在,以及基底表面較大的粗糙度均會增加薄膜中出現(xiàn)針孔及剝落等缺陷的可能性[41]。
尚政國等人[42]基底溫度對Mo薄膜的半波帶寬和(110)晶面衍射強度的影響,研宄發(fā)現(xiàn)在基底溫度為200°C時,Mo薄膜的半波帶寬最小,薄膜(110)晶面擇優(yōu)取向性最好。此外,王震東等則探宄了基底溫度對Mo薄膜擇優(yōu)取向性和電學(xué)性能的影響。在不同溫度的玻璃基底上采用直流磁控濺射法沉積制備Mo薄膜。僅僅當(dāng)基底溫度為150C時,薄膜的晶粒具有(211)晶面擇優(yōu)取向,而在其它溫度條件下沉積的Mo薄膜均呈現(xiàn)出(110)晶面擇優(yōu)取向。此外,在基底溫度為150C時沉積的薄膜表面粗糙度約為0.35nm,薄膜表面較為平整。此時薄膜電阻率為2.02X10—5Q*cm,低于在其他溫度的基底上沉積的Mo薄膜。
2.2靶材
近年來高速發(fā)展的信息產(chǎn)業(yè)對高端的液晶顯示屏的要求越來越高,因此,對顯示器薄膜晶體管中Mo薄膜電極的使用性能的要求也越來越高,尤其是在導(dǎo)電性和附著性方面。提高靶材致密度是提高濺射沉積制備Mo薄膜的使用性能的有效途徑,靶材致密度能夠影響薄膜的沉積速率,進(jìn)而能夠影響到薄膜的光電性能。靶材的致密度越高,濺射出的粒子密度越低,粒子在沉積到基底過程中的碰撞次數(shù)越少,放電現(xiàn)象越弱,因而沉積的薄膜性能越好。
Mo靶材加工工藝的不同會直接導(dǎo)致靶材的組織存在明顯差異,進(jìn)而影響到制備出的Mo薄膜的組織和性能。劉仁智等探宄了Mo靶材組織對磁控濺射法制備Mo薄膜的影響。實驗結(jié)果表明靶材組織對薄膜表面及截面形貌的影響較小。但當(dāng)靶材80%的晶粒尺寸不超過50pm時,薄膜沉積速率較快,因而薄膜厚度較為均勻,且方阻變化相對較小。此外,靶材組織的差異對濺射薄膜的結(jié)晶取向影響不夠明顯,具有不同組織的Mo靶材濺射沉積出的薄膜均呈現(xiàn)出強烈的(110)晶面擇優(yōu)取向性。張國君等對熱處理溫度在Mo靶材組織及性能的影響方面做了詳細(xì)的研宄,研宄結(jié)果表明Mo靶材晶粒尺寸隨著熱處理溫度的升高而增大,而靶材硬度隨之呈下降趨勢,且Mo靶材在1200C進(jìn)行1h熱處理,晶粒尺寸分布最均勻。
此外,靶材濺射面上的晶界密度隨著靶材晶粒的細(xì)化而增加,由于晶界處原子的能量較高,位于晶界上的原子在受到氣體離子的轟擊時更容易被濺射出來,進(jìn)而能夠大大提高革G材利用率。
2.3濺射時間
濺射時間的差異首先會影響到沉積制備Mo薄膜的顆粒形貌和晶粒尺寸大小等,進(jìn)而Mo薄膜的電學(xué)和光學(xué)性能等均會有所差異。目前,關(guān)于濺射時間不同所沉積薄膜的組織及性能差異方面的研宄也眾多。張艷霞等采用磁控濺射法濺射不同的時間(5-30min)在鈉鈣玻璃基底上沉積制備出厚度不同的Mo薄膜,并表征了Mo薄膜的表截面形貌及結(jié)晶取向,研宄分析了其中差異性和影響規(guī)律。分析結(jié)果表明,沉積時間的差異主要會影響Mo薄膜晶粒的結(jié)晶取向和晶帶組織。其中,當(dāng)濺射時間低于10min時,Mo薄膜呈現(xiàn)出強烈的(110)晶面擇優(yōu)取向性,晶帶組織為T型;但此時Mo薄膜內(nèi)存在大量組織缺陷如孔洞和間隙等使得薄膜的導(dǎo)電性大大降低。當(dāng)濺射時間增加至15min后,(211)晶面衍射峰高度開始增加。最后,隨著濺射時間繼續(xù)增加,甚至超過20min時,Mo薄膜的(211)晶面衍射峰高度進(jìn)一步增加,薄膜的結(jié)晶質(zhì)量也隨之提高。
朱曉剛等在塊狀金屬鉬基底上沉積制備出Mo薄膜,研宄分析了濺射時間分別為4h、6h和8h的薄膜結(jié)構(gòu)及熱疲勞性差異。探宄分析表明本試驗中制備的Mo薄膜均為柱狀晶生長,并呈現(xiàn)出明顯的(110)晶面,薄膜表面應(yīng)力呈現(xiàn)拉應(yīng)力,且隨這濺射沉積時間的增加,沉積制備Mo薄膜的表面殘余應(yīng)力逐漸減小;此外,薄膜內(nèi)的熱疲勞裂紋形式也發(fā)生轉(zhuǎn)變,由直線裂紋轉(zhuǎn)變?yōu)榍哿鸭y,薄膜內(nèi)發(fā)生疲勞開裂的可能性大大降低。
2.4濺射氣壓
采用磁控濺射法沉積制備Mo薄膜時,濺射氣壓的大小在很大程度上直接會影響到沉積制備薄膜的組織及性能差異。當(dāng)濺射氣壓不高時,從靶材中濺射出來的原子和氬氣分子之間發(fā)生碰撞的次數(shù)會降低,濺射原子因碰撞而損失的能量會大大減小,當(dāng)原子沉積到基底上時就具有較高的能量,靶材原子更容易在基底上擴散,進(jìn)而能夠有利于提高薄膜的附著性和致密性。但這并不是說濺射氣壓越小越好,因為當(dāng)濺射氣壓過小時,一定時間內(nèi)能夠被濺射出的靶材原子數(shù)目比較少,不能起輝或起輝不足現(xiàn)象發(fā)生的可能性會很大。隨著濺射氣壓的增加,起輝能力增強,隨后被濺射出的靶材粒子數(shù)目的增加,因而會很大程度上提高薄膜的沉積速率和濺射效率,進(jìn)而能夠提高沉積制備薄膜的致密度和膜基結(jié)合力。然而,濺射氣壓也不宜過大,過大的濺射氣壓會大大增加濺射出的靶材粒子與工作氣體離子的碰撞機率和次數(shù),靶材粒子中因碰撞而損失的能量會增加,最終當(dāng)靶材粒子沉積到基底上時其平均動能會減小,濺射粒子的擴散迀移能力大大降低,此時沉積薄膜的表面平整度和致密性都較低,薄膜的粘結(jié)性也降低。
周瓏等也通過多次試驗探宄并分析了濺射氣壓對磁控濺射沉積Mo薄膜的光學(xué)性能的影響。經(jīng)過多次對比分析發(fā)現(xiàn)使薄膜光學(xué)性能最佳的濺射氣壓0.7Pa。在此濺射條件下沉積的Mo薄膜的顆粒尺寸較小,表面光滑且紅外反射率達(dá)到最高。此外,本次實驗研宄還發(fā)現(xiàn)薄膜表面光潔度和紅外反射率隨著濺射氣壓增大而呈現(xiàn)出先增加后降低的趨勢。SilviaM.Deambrosis等人探宄了氣體種類及氣體壓強對沉積制備Mo薄膜的組織及電學(xué)性能的影響,研宄發(fā)現(xiàn)Ar工作環(huán)境中制備的Mo薄膜的組織形貌優(yōu)于Kr和Xe工作環(huán)境下沉積制備的Mo薄膜,但是粘結(jié)力略微低于后者。此外,在Ar工作條件下,低壓條件下沉積制備Mo薄膜的結(jié)晶尺寸更高,結(jié)晶性能更好,但是粘結(jié)力略有不足,因此,需要優(yōu)化濺射工藝,以達(dá)到平衡薄膜使用性能的目的。JayminRay等人也探宄了工作氣壓對Mo薄膜晶粒尺寸及光電性能的影響,其研宄結(jié)果表明在1.3~3.0Pa范圍內(nèi),薄膜的光學(xué)反射率及表面方塊電阻均隨著氣壓的升高而呈現(xiàn)降低的趨勢。鑒于此,通常選取的氬氣工作氣壓不宜過高。
2.5濺射功率
濺射功率的大小也會對沉積制備Mo薄膜的組織和性能產(chǎn)生較大的影響。較低的濺射功率不利于薄膜的成核與生長,所制備的薄膜結(jié)晶性能比較差,膜基結(jié)合力下降,在空氣中暴露一段時間后會極易出現(xiàn)局部脫皮等現(xiàn)象。荷能粒子的動能隨著濺射功率的增大而增加,靶材原子在受到轟擊時將會得到更多的能量,更容易被濺射出來。此外,隨著濺射氣體離子和成膜前驅(qū)體的能量增加,鉬薄膜的致密性也會得到提高,但同時薄膜內(nèi)部應(yīng)力得不到釋放便會留在薄膜內(nèi)。
此外,當(dāng)濺射功率足夠大時,濺射氣體離子和成膜先驅(qū)體的較高能量對Mo膜形成刻蝕作用,此時離子的刻蝕作用和因為濺射功率增加而升高的基底溫度均為Mo原子提供足夠的能量使其能夠在基底表面的較大范圍內(nèi)進(jìn)行橫向迀移,Mo薄膜的結(jié)構(gòu)也因此能夠得到調(diào)整;同時較高的基底溫度對Mo薄膜而言可以看做是一次退火處理,薄膜內(nèi)部應(yīng)力也因此得到釋放。但是濺射功率也不宜過高,當(dāng)濺射功率超過某一臨界值后,高能粒子會將能量傳遞給氣體使氣體溫度升高,薄膜質(zhì)量因此而降低,且靶材在較短時間內(nèi)獲得的大量熱能極易將靶材燒毀。
廖國等研宄了在20?100W區(qū)間內(nèi)濺射功率對沉積制備Mo薄膜表面形貌、晶型結(jié)構(gòu)、晶粒尺寸和應(yīng)力等的影響。研宄結(jié)果表明薄膜的表面粗糙度隨濺射功率的增加而增加,但均小于2nm。此外,通過XRD分析不難發(fā)現(xiàn),在不同濺射功率下制備的Mo膜均呈現(xiàn)立方多晶結(jié)構(gòu),且在濺射功率20W?40W范圍時晶粒尺寸變化不明顯,但是在40~100W區(qū)間時晶粒尺寸呈單調(diào)增加的趨勢,而薄膜應(yīng)力則呈現(xiàn)出先增加會減少的趨勢,且在40W時的應(yīng)力達(dá)到最大值2.383GPa。王天興等也探宄了不同的濺射功率對Mo薄膜的電學(xué)性能、表面形貌的影響。多次實驗結(jié)果表明,濺射功率在50?150W范圍內(nèi)沉積速率隨濺射功率的增加而趨近于線性增加。且當(dāng)濺射功率逐漸增加時,Mo薄膜的致密性也逐漸增加,其導(dǎo)電性也逐漸提高。SonVoung等人在100~250W范圍內(nèi)探宄了濺射功率對沉積制備Mo薄膜表面形貌及光學(xué)反射率的影響,研宄結(jié)果表明在150W工作功率下制備Mo薄膜具有較好的光學(xué)反射率,使用性能更佳。
2.6靶基距
在磁控濺射鍍膜過程中,靶基距的大小將會直接影響到薄膜的厚度均勻性和沉積速率。李陽平等使用SRIM軟件對靶材濺射及濺射原子輸運進(jìn)行計算機模擬,模擬結(jié)果表明濺射原子出射能量主要集中在幾到幾十電子伏范圍內(nèi),且主要以垂直于靶面方向出射,出射位置分布與離子射位置分布相似。且濺射原子的輸運主要受P(真空室氣壓)xd(靶基距)影響,Pxd愈大輸運到基底的濺射原子愈少,且能量愈小。徐均琪在磁控濺射陰極靶刻蝕數(shù)據(jù)的基礎(chǔ)上建立了靶材刻蝕速率的相關(guān)方程,并在此基礎(chǔ)上對膜厚均勻性進(jìn)行分析。研宄結(jié)果發(fā)現(xiàn),隨著靶基距的增加,膜厚均勻性得到提高,但薄膜的沉積速率會迅速下降,相同的結(jié)論在惠迎雪等的研宄中也有提及。
靶基距較小時,鍍膜區(qū)中等離子的密度比較高,而氣體散射的作用很小,因此沉積到基底上粒子的動能增大,在薄膜表面能夠進(jìn)行充分地擴散。如此一來,濺射出的粒子能夠在很大范圍內(nèi)進(jìn)行迀移,最終沉積到能量的最低點,因此薄膜表面的平整度增加,薄膜表面更加光滑,且薄膜的結(jié)晶性能也得到提高。而隨著靶基距的增加,濺射粒子在沉積過程中所經(jīng)的路徑增加,與氣體分子碰撞的幾率和碰撞次數(shù)增多,進(jìn)而降低薄膜的沉積速率。但靶基距也不能過于小,因為當(dāng)靶基距很小時,濺射粒子所蘊含的能量過高,后沉積的靶材原子會將先沉積的薄膜再次濺射出來,這將會直接造成薄膜表面粗糙度的增加。因此靶基距的大小在保證一定沉積速率的同時還要保證薄膜的均勻性。
2.7熱處理
對濺射沉積的薄膜進(jìn)行熱處理是提高薄膜實際使用性能和使用價值的有效途徑。鑒于磁控濺射法沉積制備的薄膜中常存在一定程度的內(nèi)應(yīng)力而影響到薄膜的使用性能,當(dāng)內(nèi)應(yīng)力大到一定程度時,極有可能使薄膜發(fā)生開裂而無法正常使用。因此,一般情況下常會對Mo薄膜進(jìn)行退火處理以降低薄膜內(nèi)部的應(yīng)力。但是退火溫度和退火時間的不同均有可能會對磁控濺射法沉積制備Mo薄膜的性能產(chǎn)生影響。經(jīng)高溫退火處理后Mo原子獲得更高的能量,其擴散能力和擴散速率均增加,因此薄膜顆粒之間的微畸變程度降低,而薄膜的結(jié)晶性能趨于良好。P.Chelvanathan等人探宄了350-500°C范圍內(nèi)熱處理溫度對薄膜的結(jié)晶性能和導(dǎo)電性能的影響,結(jié)果表明熱處理溫度會直接影響到Mo薄膜的晶格常數(shù)、應(yīng)變、表面形貌和體積電阻率,且在450C退火熱處理后Mo薄膜的導(dǎo)電性最佳,此時,薄膜的結(jié)晶性能也良好。
相關(guān)鏈接