1、引言
導(dǎo)孔是飛機(jī)制造工程中最常見的結(jié)構(gòu)特征之一,大量存在于框、梁、壁板等各類飛機(jī)結(jié)構(gòu)件上,主要用于飛機(jī)零部件之間的裝配連接。飛機(jī)結(jié)構(gòu)件上的導(dǎo)孔數(shù)目龐大,據(jù)統(tǒng)計(jì),一架大型飛機(jī)的各類結(jié)構(gòu)導(dǎo)孔數(shù)量多達(dá)300萬(wàn)種以上,某些單個(gè)零件上就有上千個(gè)導(dǎo)孔。因此,導(dǎo)孔加工技術(shù)是零件制造過程中的一項(xiàng)關(guān)鍵技術(shù),可靠的加工技術(shù)是導(dǎo)孔質(zhì)量?jī)?yōu)劣的有效保證。
2、導(dǎo)孔加工方法
2.1 鈦合金材料
鈦合金具有比強(qiáng)度(強(qiáng)度/密度)高、熱強(qiáng)度高、熱穩(wěn)定性好和抗蝕性好等優(yōu)點(diǎn),但其難加工性造成了實(shí)際生產(chǎn)中加工效率低、加工成本高及加工質(zhì)量不穩(wěn)定等問題。鈦合金材料的難加工性往往會(huì)導(dǎo)致銑削過程中刀具的快速磨損及失效,降低加工效率及加工穩(wěn)定性,具體原因包括:切屑變形系數(shù)小;導(dǎo)熱系數(shù)小,切削溫度高;化學(xué)活性大;單位面積上的
切削力大;粘刀現(xiàn)象嚴(yán)重等。
2.2 導(dǎo)孔加工方式
長(zhǎng)期以來,常采用人工手動(dòng)制導(dǎo)孔和使用數(shù)控機(jī)床加工導(dǎo)孔兩種方式。
(1)人工手動(dòng)制孔
工人手動(dòng)鉆導(dǎo)孔的加工方式一直存在于航空結(jié)構(gòu)件的加工中。
鉆孔主要依據(jù)按樣板或明膠板劃線、按尺寸劃線、制造鉆?;蛘咩@模板等。圖1為鉆模加工示意。
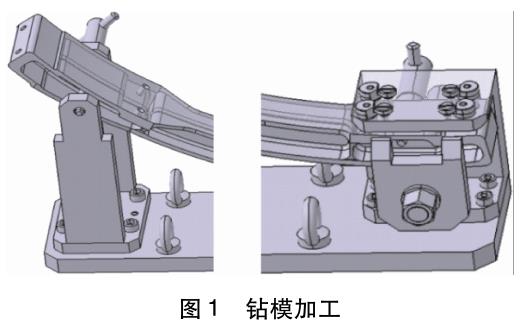
工人主要根據(jù)零件結(jié)構(gòu)特點(diǎn)、導(dǎo)孔精度、孔數(shù)量和加工表面的平整度等來選用鉆導(dǎo)孔。
大型的框、梁、壁板等零件導(dǎo)孔數(shù)量較多,多達(dá)上千個(gè),工人的鉆制依據(jù)是樣板或者明膠板。根據(jù)尺寸劃線鉆導(dǎo)孔主要針對(duì)尺寸較小、導(dǎo)孔數(shù)量很少、零件表面較規(guī)則的零件,否則對(duì)于劃線工人來說難度太大,操作適用性較差。當(dāng)導(dǎo)孔的位置精度或尺寸精度要求較高時(shí),特別是位置精度要求小于0.3mm時(shí),可采用鉆?;蛘咩@模板鉆導(dǎo)孔。因?yàn)椴捎脴影寤騽澗€的方式均無法確保導(dǎo)孔的位置精度在0.3mm以內(nèi),而鉆模可以準(zhǔn)確設(shè)計(jì)定位基準(zhǔn)和穩(wěn)定的裝夾,以保證位置精度。但鉆模僅適用于較少的孔,且還需設(shè)計(jì)并制造工裝,經(jīng)濟(jì)性較差,準(zhǔn)備周期長(zhǎng)。
工人手工鉆制導(dǎo)孔勞動(dòng)強(qiáng)度大,效率低,而且導(dǎo)孔質(zhì)量得不到保證,孔徑和孔位的精度完全依靠工人的操作熟練度,加工質(zhì)量問題頻現(xiàn),導(dǎo)致零件超差甚至報(bào)廢。導(dǎo)孔的加工質(zhì)量是影響飛機(jī)壽命和飛行安全的重要因素,如果導(dǎo)孔的孔徑或孔位有偏差,將影響連接功能,若強(qiáng)行裝配會(huì)導(dǎo)致扭曲變形,影響裝配精度及零件性能,甚至可能引起飛行質(zhì)量事故。
(2)數(shù)控制孔
意識(shí)到導(dǎo)孔制造問題的重要性,國(guó)內(nèi)外均在研究和試用先進(jìn)的導(dǎo)孔制造技術(shù),精密制孔技術(shù)應(yīng)運(yùn)而生,例如:角度頭鉆孔、機(jī)器人自動(dòng)鉆孔、柔性導(dǎo)軌自動(dòng)制孔、多軸數(shù)控制孔等。
其中數(shù)控多軸制孔在航空結(jié)構(gòu)件的加工過程中因適用性較強(qiáng)被廣泛應(yīng)用。
數(shù)控制孔是依據(jù)數(shù)字化模型制定加工方案,設(shè)計(jì)裝夾定位方式,編制數(shù)控加工程序,在多軸數(shù)控機(jī)床上進(jìn)行導(dǎo)孔加工。數(shù)控機(jī)床制造導(dǎo)孔,不僅可使加工效率提高數(shù)倍甚至數(shù)十倍,而且導(dǎo)孔質(zhì)量較高,導(dǎo)孔的孔徑和位置精度均可以保證在0.1mm以內(nèi),加工精度較高的機(jī)床可達(dá)到0.02mm。人工制孔與數(shù)控制孔相關(guān)因素的比較見表1。
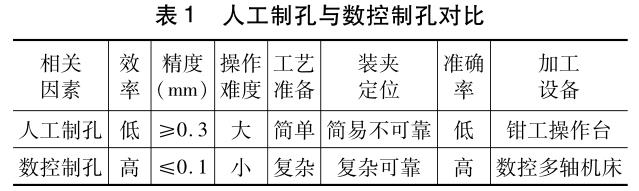
2.3 導(dǎo)孔檢測(cè)
導(dǎo)孔的檢測(cè)主要采用通用量具塞規(guī)、卡尺等檢測(cè)孔徑,采用專用樣板、明膠板、檢模等檢測(cè)導(dǎo)孔的位置,屬于人工對(duì)比式檢測(cè)。
因人工檢測(cè)操作工作量大,操作人員技能水平不同,檢測(cè)結(jié)果差異性大。受檢測(cè)精度和效率的影響,傳統(tǒng)的檢測(cè)方式已不能滿足質(zhì)量檢測(cè)要求,行業(yè)內(nèi)也在探究高效精準(zhǔn)的檢測(cè)方式,新的檢測(cè)方式層出不窮,如測(cè)量機(jī)檢測(cè)和影像檢測(cè)等。
3、數(shù)字化導(dǎo)孔加工方法
以某梁類零件為例研究數(shù)字化加工導(dǎo)孔方法。
加工工藝方案制定主要包括定位裝夾方式、加工流程、刀具及參數(shù)選擇和數(shù)控程序編制等。
3.1零件簡(jiǎn)介
實(shí)驗(yàn)零件為典型的細(xì)長(zhǎng)鈦合金梁類零件,材料牌號(hào)TA15M,雙面槽腔,外形為復(fù)雜雙曲面,緣條厚度最小處為3.5mm,最大處為20mm。
該零件存在較多的配合關(guān)系,在零件上遍布不同規(guī)格的導(dǎo)孔共432個(gè),尺寸精度及表面質(zhì)量要求嚴(yán)格。零件導(dǎo)孔如圖2所示。
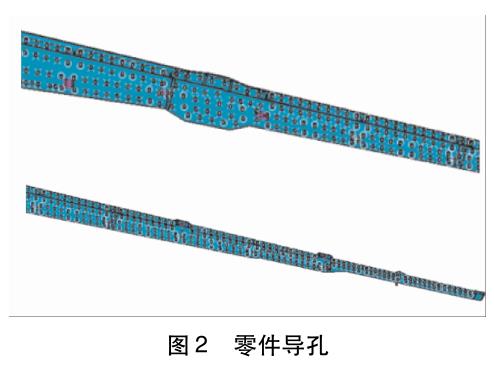
對(duì)零件導(dǎo)孔進(jìn)行工藝性分析,結(jié)果如下:導(dǎo)孔直徑分別為φ3.1,φ4,φ5,φ7,φ8,φ10;導(dǎo)孔分布于零件的緣條及筋條上;導(dǎo)孔的法向垂直于導(dǎo)孔所在表面,其95%以上為變角度曲面;零件為長(zhǎng)梁類零件,材料為模鍛件,緣高均為斜面;加工公差要求孔位±0.2、孔徑0.20、孔距±0.2;導(dǎo)孔所分布的壁厚從3.5~20mm不等。
根據(jù)上述信息分析出該零件導(dǎo)孔的加工難度主要集中在以下幾點(diǎn):導(dǎo)孔數(shù)量較大;導(dǎo)孔種類較多;導(dǎo)孔分布廣泛;導(dǎo)孔法向方向難以確定;裝夾定位難度大;導(dǎo)孔精度較高;導(dǎo)孔深度不均。從保證導(dǎo)孔精度和加工效率兩方面分析,該零件如果采用人工制導(dǎo)孔方式幾乎無法實(shí)現(xiàn),只有采用數(shù)控多軸制孔才能保證導(dǎo)孔的法向和精度,并顯著提高加工效率。
3.2定位裝夾方式
實(shí)驗(yàn)零件長(zhǎng)且細(xì),97%導(dǎo)孔集中在緣條,針對(duì)現(xiàn)有加工資源,采用緣條定位是較好的選擇。
由于該零件的緣條為斜緣條,采用斜緣條直接定位會(huì)大幅降低定位面的精度,對(duì)零件加工質(zhì)量影響較大。
因此在緣條高度上設(shè)置工藝凸臺(tái)來進(jìn)行定位,用以保證定位基準(zhǔn)精度。
確定定位面后,還需選擇兩個(gè)孔參與定位。
確定定位基準(zhǔn)后,根據(jù)定位基準(zhǔn)設(shè)計(jì)裝夾壓緊的工裝。定位方式盡量要與正反兩面加工時(shí)的定位方式一致,以保證數(shù)控導(dǎo)孔位置的準(zhǔn)確度。
然后需要考慮工裝的形式,該工位工裝壓緊零件的方式較難,因?yàn)樵诹慵木墬l上每一個(gè)位置都有導(dǎo)孔,壓板的位置會(huì)干涉導(dǎo)孔的鉆制。因此既要確保零件裝夾的穩(wěn)定性,還要考慮操作簡(jiǎn)單便捷、不干涉。該零件在腹板上有較多大直徑減輕孔,利用該特點(diǎn),可在工裝上采用穿螺栓、壓緊腹板的方式對(duì)零件進(jìn)行壓緊,不僅起到壓緊零件的作用,并有效避免了在鉆導(dǎo)孔時(shí)鉆頭與壓板的干涉,去除了工人在加工過程中倒壓板的工作,降低了勞動(dòng)強(qiáng)度。工裝設(shè)計(jì)見圖3。
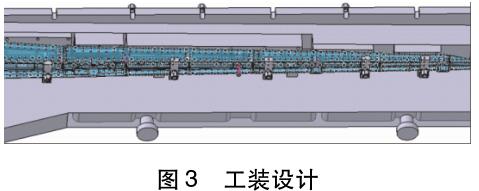
3.3 確定加工流程
加工流程的合理安排是零件導(dǎo)孔加工的重要環(huán)節(jié),合理的加工流程是導(dǎo)孔加工質(zhì)量和加工效率的有效保證。根據(jù)某梁類零件的結(jié)構(gòu)特點(diǎn)及現(xiàn)有的加工資源,采用數(shù)控導(dǎo)孔加工設(shè)計(jì)兩個(gè)工位,正反兩面加工,裝夾定位方式基本一致。
數(shù)控加工導(dǎo)孔采用中心鉆點(diǎn)孔位,避免鉆孔時(shí)鉆頭偏滑導(dǎo)致孔位置偏移或孔形狀橢圓。特別是斜面或變角度曲面必須在鉆孔前進(jìn)行點(diǎn)孔位,以便在使用鉆頭鉆孔時(shí)起定心作用。導(dǎo)孔的加工順序設(shè)定的主要原則是:加工精度高;防錯(cuò)級(jí)別最高;加工效率高;操作難度最小。
該零件的導(dǎo)孔鉆制順序是由少至多,相近規(guī)格交叉加工。
3.4刀具及切削參數(shù)選擇
數(shù)控加工中刀具的選用至關(guān)重要,刀具種類及切削參數(shù)直接影響零件的尺寸精度和加工效率等。由于零件結(jié)構(gòu)特異,且材料為難加工材料,因此對(duì)刀具的要求較高。某梁數(shù)控加工導(dǎo)孔的刀具均選用整體合金專用刀具,加工參數(shù)依據(jù)現(xiàn)有參數(shù)庫(kù)及零件實(shí)際加工情況來確定。加工參數(shù)選擇見表2。
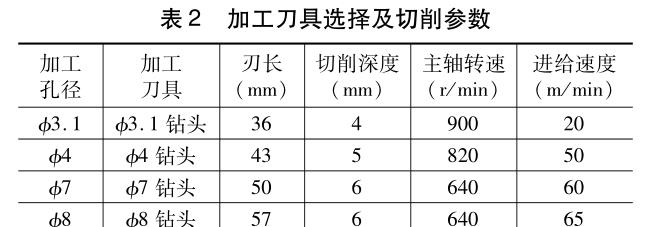
3.5 程序編制
數(shù)控導(dǎo)孔程序的編制使用CATIA軟件,零件在加工過程中盡可能地釋放應(yīng)力以及降低切削力,減小了零件粗加工后的變形量。在數(shù)控鉆導(dǎo)孔程序編制過程中,要考慮走刀方式、切削深度、接近方式等。由于導(dǎo)孔一般較小,鉆頭較細(xì),所以在加工過程中容易折斷,折斷時(shí)會(huì)打傷零件,導(dǎo)致零件超差或報(bào)廢。有的鉆頭會(huì)折斷在零件內(nèi)部,難以取出,并傷及零
件。接近零件方式不正確、加工速度過快、退刀方式錯(cuò)誤和積屑等因素都會(huì)導(dǎo)致鉆頭折斷,所以在數(shù)控程序編制過程中需要全面考慮。
4、結(jié)語(yǔ)
通過研究適用于鈦合金航空結(jié)構(gòu)件導(dǎo)孔的多軸數(shù)控加工方法,解決了生產(chǎn)的實(shí)際問題。
以本文試驗(yàn)零件為例,緣條最厚處達(dá)到20mm,如采用傳統(tǒng)方法,常規(guī)鉗工鉆制約需35~40h,加工難度較大,費(fèi)時(shí)費(fèi)力,產(chǎn)品質(zhì)量也不易保證。
采用數(shù)控加工導(dǎo)孔時(shí)間僅需10.4h,既省時(shí)省力,又提高了產(chǎn)品質(zhì)量。
特別是對(duì)于批量化生產(chǎn)的零件,加工優(yōu)勢(shì)更加顯著。該方案已通過實(shí)際加工驗(yàn)證,生產(chǎn)零件質(zhì)量合格,加工過程穩(wěn)定。
參考文獻(xiàn)
[1]王歡.鈦合金螺旋銑孔試驗(yàn)研究[D].大連:大連理工大學(xué),2015.
[2]趙鵬飛.孔加工切削參數(shù)優(yōu)化系統(tǒng)的研究與開發(fā)[D].南京:南京理工大學(xué),2013.
第一作者:孫麗敏,航空工業(yè)沈陽(yáng)飛機(jī)工業(yè)集團(tuán)有限公司數(shù)控加工廠,110850沈陽(yáng)市First
Author:Sun Limin,Shenyang Aircraft Industrial (Group)Co.,Ltd.,Shenyang110850,China
相關(guān)鏈接