1、靶材的定義
靶材是通過物理氣相沉積(PVD)技術(shù)鍍膜的濺射源。它利用高能量的離子束轟擊所需濺射鍍膜源材料的表面,高速離子撞擊到源材料表面,與其表面原子發(fā)生動能交換,使想要鍍膜的源材料表面原子獲取較大的動能,從而脫離表面原子的束縛沉積到鍍膜基片上,被轟擊的源材料稱為濺射靶材。其實物圖如下圖 1-1 所示。
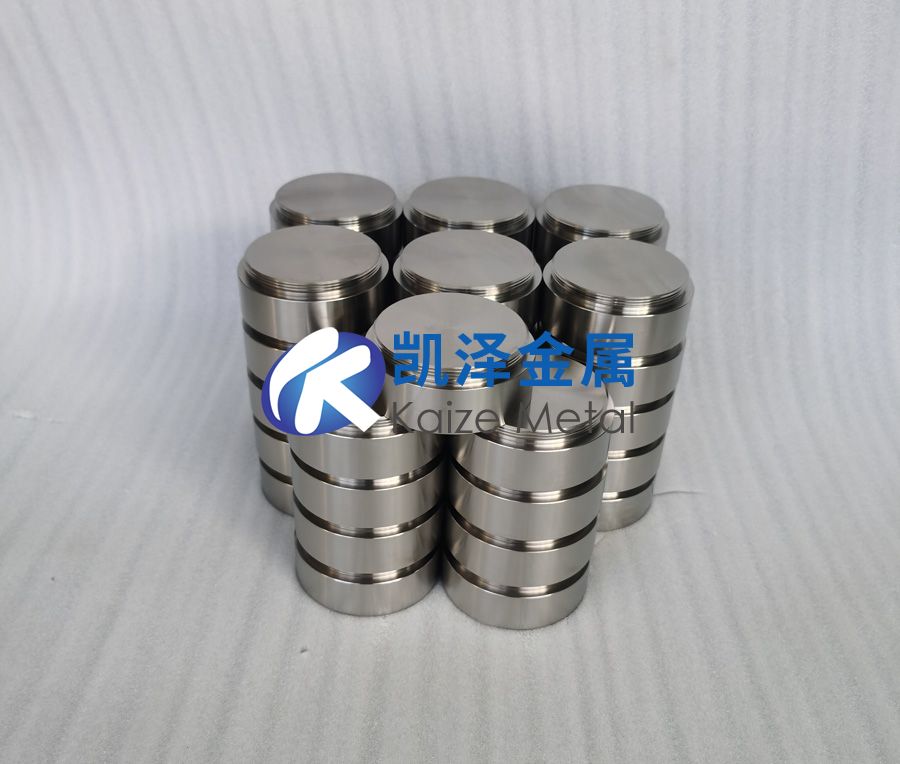
2、高純鋁合金濺射靶材的特性
在所有應(yīng)用產(chǎn)業(yè)中,半導(dǎo)體產(chǎn)業(yè)對靶材濺射薄膜的質(zhì)量要求最高。要求靶材具有很高的純度,靶材的純度影響濺射薄膜的均勻性。不同性能的薄膜材料,對靶材純度的要求不同。以純Al靶為例,純度越高,濺射薄膜的耐蝕性,及電學(xué)、光學(xué)性能越好。
靶材應(yīng)具有良好的致密度,不應(yīng)有分層、夾雜、疏松和氣孔等缺陷。當(dāng)靶材內(nèi)部出現(xiàn)分層時,濺射速率會受到很大的影響,從而影響濺射薄膜的均勻性。靶材致密度差,在磁控濺射的過程中,高能離子束轟擊到靶材的表面,靶材內(nèi)部氣體釋放,從而造成顆粒的飛濺。
靶材在濺射鍍膜過程中,其晶粒尺寸的大小及組織均勻性對濺射薄膜沉積速率影響較大。研究結(jié)果表明,靶材組織中晶粒尺寸越細小,濺射速率越快;晶粒尺寸大小越均勻,濺射鍍膜后形成的薄膜厚度分布越均勻。李洪賓等人研究發(fā)現(xiàn),在濺射鍍膜各項工藝參數(shù)都相同的條件下,靶材濺射鍍膜速率的大小取決于原子密排度隨晶粒尺寸的變化而變化。
濺射靶材在鍍膜過程中受高能離子束的轟擊,要求其具有一定的抗沖擊性能,Al-Cu合金中第二相的尺寸及分布對靶材的抗沖擊性能有較大影響。通常,第二相細小彌散分布,其強化效果越好。陳希等人研究發(fā)現(xiàn),納米級針狀第二相彌散分布于晶內(nèi),在靶材沖擊過程中出現(xiàn)部分回溶現(xiàn)象,起到很好的彌散強化效果,有利于靶材抗沖擊性能的提高;微米級第二相顆粒由于尺寸較大,且是硬脆相,在靶材沖擊過程中不易變形,容易造成局部應(yīng)力集中,從而產(chǎn)生沖擊微裂紋,影響靶材的使用壽命。
3、靶材的組織控制及研究現(xiàn)狀
目前,常用的鋁合金靶材制備方法主要有鑄造法和粉末冶金法兩種。
鑄造法是將一定配比的合金原料進行熔煉,然后再將溶液澆注于模具中,冷卻后形成鑄錠,再通過機械加工等方法形成靶材。采用鑄造法熔煉所得的靶材,其致密度較好,雜質(zhì)含量較低,但由于不同金屬流動性不同,容易造成成分的不均勻。
粉末冶金法是將不同的金屬鑄錠制成粉末,然后按照一定的比例進行混合,在等靜壓的條件下進行壓鑄成型。粉末冶金法制成的靶材組織均勻性較好,但不同的金屬粉末在混合過程中容易進入雜質(zhì),使得靶材雜質(zhì)含量高。由于銅的熔點與鋁的熔點相差較大,在進行真空熔煉時極易造成成分不均勻現(xiàn)象,為了解決鑄造法獲得合金靶材的成分不均勻現(xiàn)象,通常要對合金進行相應(yīng)的塑性加工方法,使其成分均勻并達到細化晶粒的目的。
傳統(tǒng)的鋁合金靶材制備工藝為對靶材進行不同變形量的軋制處理,然后再進行不同的退火工藝處理,使其發(fā)生再結(jié)晶,達到細化晶粒,組織均勻的目的。Nakashima 等人通過 ECAP 工藝,在不改變工件外形的條件下產(chǎn)生劇烈塑性變形,從而獲得納米級晶粒。雖然 ECAP 工藝細化晶粒的效果很顯著,但是造成了原材料的極大浪費,成本較高,不適宜工業(yè)生產(chǎn)。累計疊軋焊(ARB)也是一種使材料產(chǎn)生劇烈塑性變形從而細化晶粒的一種加工方法,將軋制后的合金板材剪斷,累加后再次軋制,反復(fù)疊軋以產(chǎn)生劇烈塑性變形來細化晶粒。累計疊軋焊在累計軋制的過程中由于溫度過高,出現(xiàn)了嚴重的氧化現(xiàn)象,導(dǎo)致靶材純度較低,影響薄膜的性能。高壓扭轉(zhuǎn)法是與等通道角擠壓法(ECAP)一樣,均被 Valiev 等人用于制備超細晶的一種 SPD 方法,其裝置主要由模具和壓頭組成,下模采用固定式,壓頭可以轉(zhuǎn)動,實驗前將試樣放入模具中,利用壓頭對試
樣施加 GPa 級別的高壓,壓頭在轉(zhuǎn)動過程中與金屬表面接觸,產(chǎn)生很大的摩擦力,使金屬材料發(fā)生剪切變形,從而達到細化晶粒的目的。目前,利用高壓扭轉(zhuǎn)法已成功制備超細晶材料,可以細化晶粒尺寸至100 nm 左右,但高壓扭轉(zhuǎn)法(HPT)使用 GPa 級別的高壓,對模具的要求較高,另外,其制備的試樣基本都是圓盤狀,且試樣尺寸較小,對靶材尺寸限制較大,不利用大尺寸靶材的生產(chǎn)。
Selines 等人將鋁合金冷卻至-196 ℃條件下,然后進行超低溫軋制,為得到濺射靶材所需要的晶粒尺寸及組織均勻性,低溫冷軋后的試樣需要進行再結(jié)晶退火,消除應(yīng)力,從而細化晶粒至亞微米級,而且組織均勻,材料的成形性和延展性也得到很大程度的提高。但低溫冷軋在保證晶粒尺寸細化的同時也大大的增加了成本,從而使低溫冷軋及退火工藝在靶材制備中僅停留在高端產(chǎn)品領(lǐng)域,不利于工業(yè)化生產(chǎn)。
傳統(tǒng)的軋制退火工藝,可通過調(diào)整不同的軋制變形量及退火工藝參數(shù)使材料發(fā)生再結(jié)晶,同樣可以細化晶粒,消除鑄錠中的成分不均勻現(xiàn)象,達到靶材的使用要求,提高濺射靶材的利用率和濺射薄膜的均勻性。傳統(tǒng)的軋制退火工藝,成本較低,工業(yè)上易于實現(xiàn)。因此對傳統(tǒng)的冷軋及再結(jié)晶退火工藝參數(shù)進行探索優(yōu)化是很有必要的。
相關(guān)鏈接