近年來,我國高新技術領域迅猛發(fā)展,航空航天、海洋工程、石油化工及武器裝備等高端領域結構件正向輕量化、高強化、高可靠性和耐久性等極端服役性能發(fā)展,鈦合金因其比強度高、耐蝕性好、耐高溫、抗疲勞等優(yōu)異性能,成為高端裝備的優(yōu)選結構材料。高端裝備通常由形狀、尺寸各異的若干個零部件構成,這些零部件的尺寸精度及性能直接影響裝備整體的可靠性及安全性[1 - 6],這就對零部件的成形技術及尺寸精度提出了更高的要求。
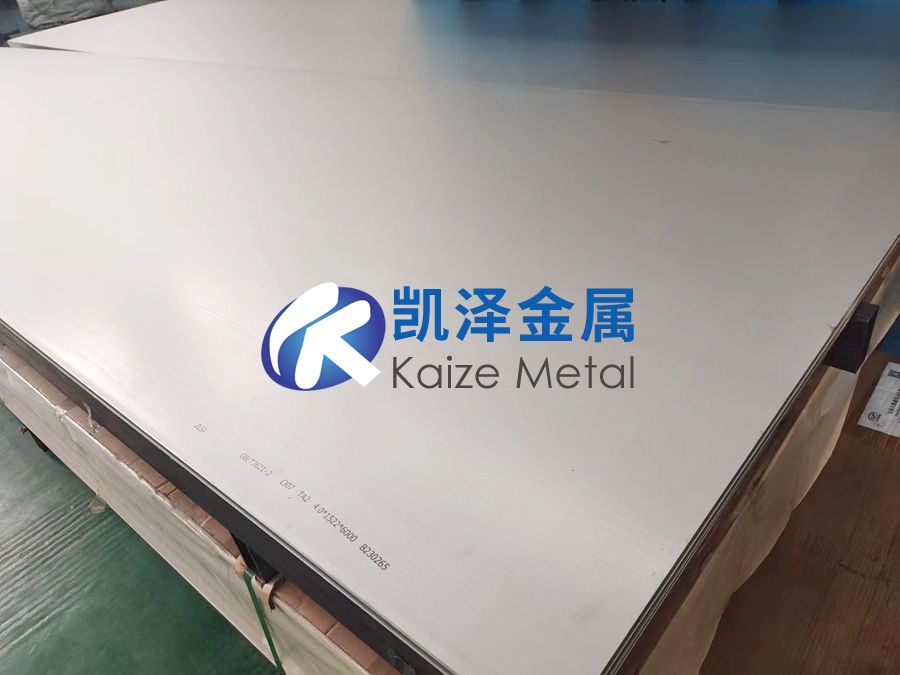
鈦合金屬于難變形合金,成形加工困難,特別是 α-Ti 的晶體結構為密排六方結構,具有較大的致密度和配位數(shù),晶胞中的原子排列緊密,滑移系少,滑移過程的空間位向少,位錯運動的阻力較大[7],塑性差,成形過程中的抗力較大,故成形尺寸精度不高。此外,鈦合金熱熔小、導熱性差,也導致其熱加工窗口狹窄。因此,為了制備滿足高端裝備要
求的各種形狀的鈦合金產品,就必須選擇與鈦合金加工特性相適應的冷、熱成形加工技術。
西北有色金屬研究院鈦合金研究所長期致力于鈦合金材料及相關加工技術研究,開發(fā)出了一系列適合不同形狀、規(guī)格的鈦合金零部件產品加工技術。
本文主要介紹冷沖壓成形技術、超塑成形技術、旋壓成形技術、熱推制成形技術、熱模鍛成形技術的特點及其在鈦合金成形中的應用,以期為推動我國鈦合金成形技術的進步提供參考。
1、冷沖壓成形技術
冷沖壓成形是在常溫下利用沖壓設備和模具,使各種不同規(guī)格的板料在壓力作用下變形成所需形狀的一種加工工藝。材料的冷沖壓成形性與材料特性有關,一般要求材料具有良好的機械性能、較大的變形能力以及理想的金相組織,其中,機械性能包含了材料的屈服強度、抗拉強度、延伸率、硬度、塑性應變比 r 等參數(shù)。
較高的屈服強度和抗拉強度會使材料的沖壓成形抗力增加,成形難度增大,模具壽命降低。此外,高的屈服強度還會使零件成形結束脫模后的回彈增大,尺寸精度降低,而高延伸率材料的成形極限較大,有利于沖壓成形。一般金屬材料的冷沖壓成形需要分多次才能達到最終的產品形狀,加工過程中會出現(xiàn)硬化現(xiàn)象。這種現(xiàn)象源于材料在承受一定塑性變形后繼續(xù)施加載荷使變形抗力增加以對抗塑性變形的再產生,較高的加工硬化系數(shù)意味著材料繼續(xù)加工會抑制局部變形,并造成硬化,導致塑性降低而不易加工。但較低加工硬化系數(shù)的材料在繼續(xù)加工時會引起局部變形增大而導致薄弱區(qū)域開裂,因此拉伸成形需要材料具有合適的加工硬化系數(shù) n。
材料的塑性應變比 r 是表征材料各項異性的參數(shù),主要影響拉伸性能,較高的 r 值說明材料的各向異性不明顯。綜上,良好的沖壓成形性對材料的性能要求是具有低的屈強比、高的延伸率、適當?shù)募庸び不禂?shù) n 和較高的塑性應變比 r。
表 1 列出了幾種金屬材料與拉伸成形性能相關的參數(shù)[8~ 10]。由表 1 可以看出,鈦的拉伸成形性能較其他金屬差,因此其冷加工成形更加困難。
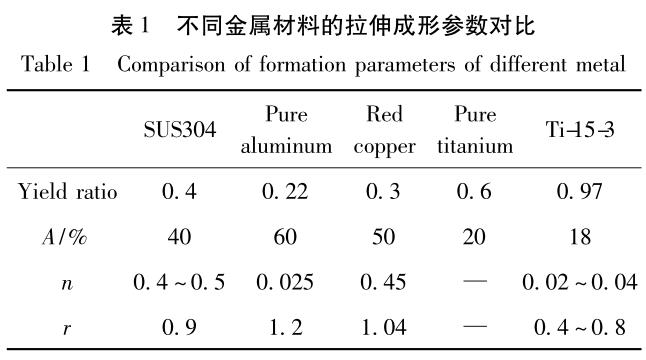
鈦合金板材在室溫下的可成形性十分有限,其室溫力學性能和微觀組織表現(xiàn)出的流線都具有明顯的各向異性,成形過程中容易產生缺陷[11]。因此,冷成形技術僅適合于鈦合金薄板的加工。自 20 世紀90 年代,西北有色金屬研究院鈦合金研究所針對用戶需求開展了鈦金屬隔膜成形技術研究,并根據(jù)鈦合金材料的性能特點設計開發(fā)出了一種適合深拉成形的 高 塑 性、低 屈 服 強 度 的 隔 膜 專 用 鈦 合 金 板材[12]。針對鈦合金屈強比高、材料回彈大的特點,研究人員通過模具設計及成形工藝參數(shù)的優(yōu)化開發(fā)出了低速率拉伸成形工藝、分步多次成形技術以及機加工與沖壓相結合成形技術[13 - 15],成功制備出了規(guī)格在 180 mL ~ 70 L 范圍內的十幾種高精度變壁厚鈦翻轉隔膜、Ti-15-3 合金球形高壓氣瓶[16]、箔材三維空間結構翅片等產品,有效避免了回彈造成的尺寸
精度差、材料各向異性導致的周向變形不均及參數(shù)控制不當造成的制耳、起皺、開裂等現(xiàn)象,滿足了國防重點工程亟需。圖 1 為西北有色金屬研究院鈦合金研究所采用冷沖壓成形技術制備的鈦合金產品。
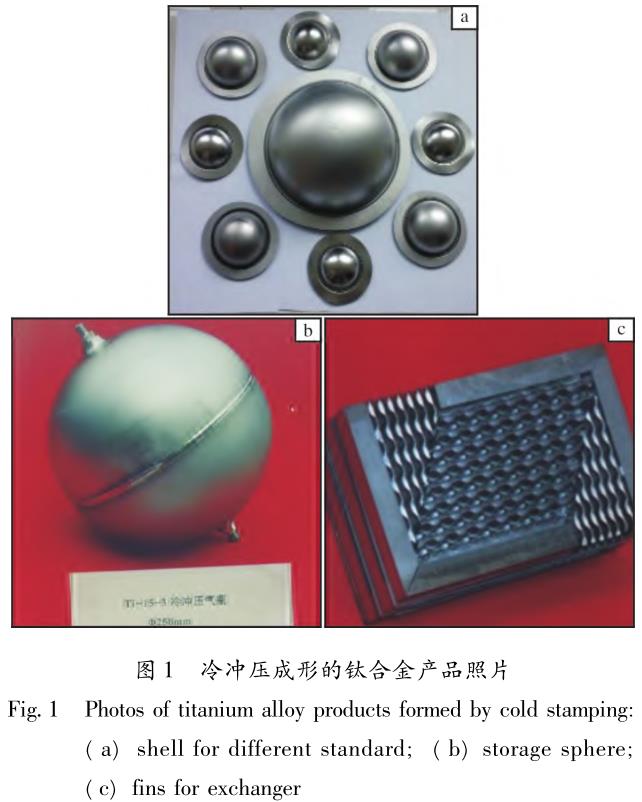
2、超塑成形技術
2. 1超塑成形技術的特點
超塑成形是利用金屬材料在一定溫度及應變速率下所呈現(xiàn)的超塑性( 具有超塑性的材料能伸長若干倍而不出現(xiàn)縮頸和斷裂) ,將坯料加工成所需尺寸和形狀的工藝。通常,超塑成形是在密封條件下,通過向鈦合金板材一側或兩側施加氣體成形壓力,依靠板材 的 減 薄 獲 得 與 模 具 型 腔 相 近 的 結 構 件 外形[17]。超塑成形工藝具有成形性好、變形量大、尺寸精度高、表面質量好、無殘余應力、減少零件加工數(shù)量等優(yōu)點,不易出現(xiàn)板材在傳統(tǒng)成形過程中出現(xiàn)的回彈、破裂等現(xiàn)象[18],在減輕飛行器結構重量、降低生產成本方面顯示出極大的優(yōu)越性。
2. 2超塑性分類及成形條件
根據(jù)實現(xiàn)超塑性的條件,超塑性主要分為相變超塑性和組織超塑性。相變超塑性又稱為動態(tài)超塑性或環(huán)境超塑性,是指材料在一定溫度和外加載荷條件下,經多次循環(huán)相變或同素異構轉變獲得大的延伸率。而本文所涉及的超塑成形主要為組織超塑性。
實現(xiàn)組織超塑性一般需要滿足組織條件、應變速率條件和溫度條件。( 1) 組織條件:組織細化,即要求細微晶粒,尺寸一般小于 10 μm。晶粒等軸化有利于在切應力作用下產生晶界滑移或轉動。大角度晶界在切應力作用下很容易發(fā)生晶界滑動,因此基體晶界應為大角度晶界。晶界遷移可以使應力集中松弛,有利于維持變形中晶粒的等軸性。超塑性合金中最好有第二相存在,這樣有利于在變形過程中抑制基體晶粒的長大,但第二相的強度和硬度應當與基體材料處于同一量級,以避免變形過程中兩相界面產生空洞而過早斷裂。( 2) 應變速率條件:不同的材料有不同的應變速率 ε 與應變速率敏感性指數(shù) m、流動應力 σ 的關系曲線,需要選擇最佳應變速率,一般在 10- 4~ 10- 2 s- 1 范圍內,遠低于常規(guī)
變形,一定程度上使超塑成形的生產效率和應用受到限制。( 3) 溫度條件:一般要求成形溫度不小于0. 5Tm( Tm為材料熔點) 。
除以上 2 種超塑性外,金屬材料在再結晶或組織轉變時,顯微組織在不穩(wěn)定的狀態(tài)下會生成等軸超細晶,此時在短時間內快速施加外力,也會表現(xiàn)出超塑性。有些材料在退火狀態(tài)下產生超塑性,有些材料在大電流作用下產生超塑性[19]。
2. 3超塑成形技術發(fā)展及應用
從 20 世紀 60 年代開始,受高性能戰(zhàn)斗機需求推動,國外航空工業(yè)率先開展超塑成形技術研究,超塑性及其應用研究也進入了快速發(fā)展時期。70 年代早期,美國 Rockwell 公司利用超塑成形技術制造了形狀復雜的 F-15 戰(zhàn)斗機鈦合金整體骨架結構,使鈦合金制造工藝發(fā)生了技術變革。隨后,美國的BLATS 計劃將鈦合金超塑成形/擴散連接( SPF/DB)
組合技術列為重點研究項目,制造了 B-1B 戰(zhàn)略轟炸機的短艙框架、輔助動力艙門等重要構件,不僅大幅降低了成本,還顯著提高了成形效率。隨后研究人員開發(fā)了超塑性鍛造技術,該技術相比用 SPF/DB技術零件數(shù)量更少,主要用于國防工業(yè)。民用方面,采用等溫鍛造技術制成了人造心臟瓣膜、人工髖關節(jié)、高爾夫棒等精密零件。
西北有色金屬研究院鈦合金研究所自 20 世紀 80年代開始進行鈦合金超塑成形技術的探索研究,并制備出用于制造飛行數(shù)據(jù)記錄儀( 黑匣子) 的 Ti-451合金超塑成形殼體( 圖 2a)
[20],產品通過了飛機適航條款所規(guī)定的高強度沖擊、高溫燒蝕等嚴格測試。
此外,還利用厚壁管坯吹脹成形工藝制備出整體無焊縫型 TC4 鈦合金高壓氣瓶( 圖 2b) 。
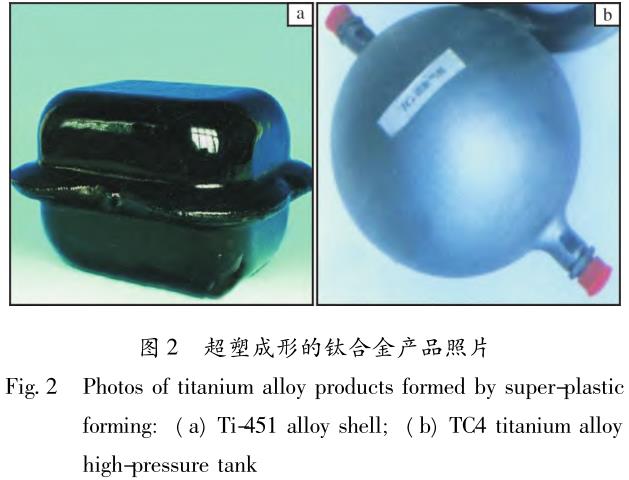
進入 21 世紀,西北有色金屬研究院鈦合金研究所又承擔了多項超塑成形鈦合金的研究項目,合金種類包括 TC4、SP700 和 TA15 等,先后研制出了滿足性能指標要求的超細晶 TA15 和 SP700 鈦合金板材,其晶 粒 尺 寸 小 于 3 μm,超 塑 性 延 伸 率 大 于2000% ,并采用超塑成形/擴散連接技術制備出了航空用相關產品[21 - 25]。圖 3 為 SP700 鈦合金的超細晶組織、超塑拉伸試樣及產品外觀。
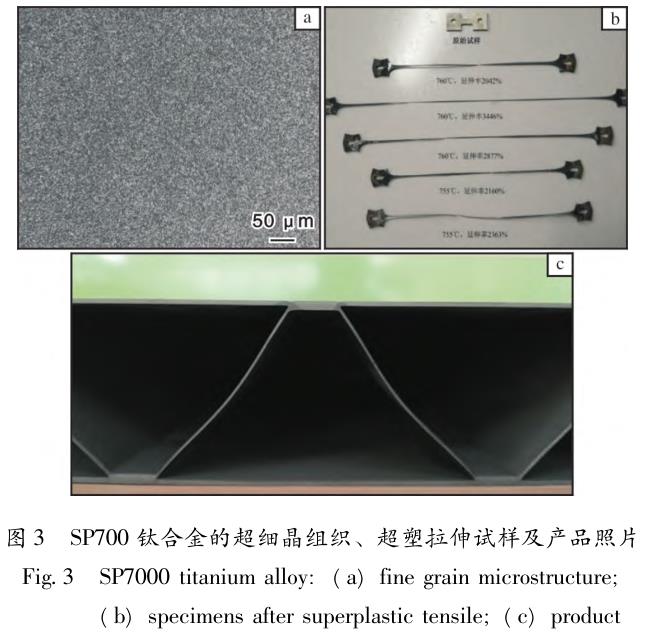
3、旋壓成形技術
旋壓成形是一項傳統(tǒng)成形工藝,該工藝具有變形力小、節(jié)約原材料等特點。近年來,隨著機電一體化控制、高精度實時測量及大數(shù)據(jù)人工智能技術的引入,旋壓成形技術與裝備得到了長足的發(fā)展,并已經成為金屬壓力加工的重要方法。目前旋壓裝備正向著系列化和標準化方向發(fā)展。在許多工業(yè)發(fā)達國家,旋壓設備的標準化程度很高,旋壓成形工藝穩(wěn)定,產品多種多樣,應用范圍日益廣泛。
圓筒形件的強力旋壓變形過程中,始終遵循著體積不變的原則,工件形狀的改變包括旋壓前后圓筒壁厚減薄、直徑變小、長度增加等,同時產品內徑也會因工藝參數(shù)的不同而改變。最終產品要素為圓筒內外徑、壁厚、長度、直線度、圓度等,產品長度可用式( 1) 計算[26]。

式中: L1 為工件長度;L0 為毛坯長度;S0 為毛坯厚度; S1 為工件厚度; d1 為工件內徑。
由于鈦合金的冷旋壓變形能力較低,尤其是高強鈦合金,在旋壓加工過程中需要對加工部位進行局部加熱( 加熱方式包括火焰加熱和感應加熱) 。20世紀 80 年代,西北有色金屬研究院鈦合金研究所采用局部加熱強力旋壓工藝制備出圓柱形 Ti-451 合金罐體[27],如圖 4 所示。該罐體規(guī)格為 φ130 mm ×1. 2 mm × 160 mm,爆破壓力達到 16 MPa,通過了極限爆破壓力和耐久性能考核。
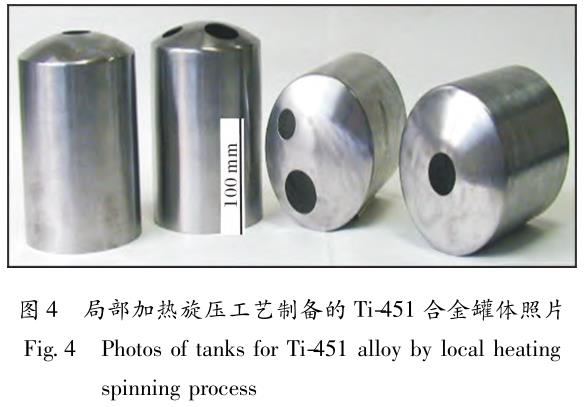
應用戶需求,西北有色金屬研究院鈦合金研究所開展了鈦合金波紋管的研制。采用滾珠旋壓加工技術制備出極薄壁 CT20 鈦合金管材,其壁厚僅為管徑的 1 /600 ~ 1 /200,并以其為坯料成功制備出多層結構波紋管,如圖 5 所示。
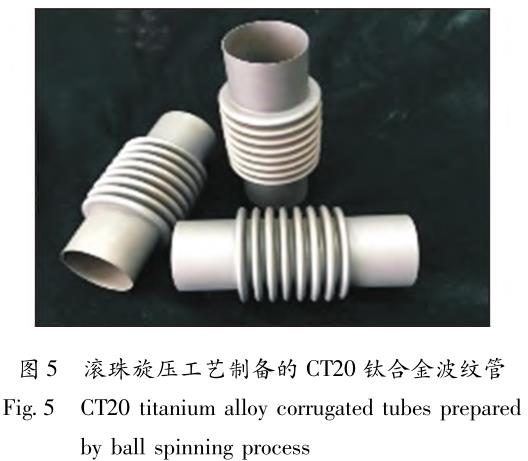
4、熱推制成形技術
熱推制成形是環(huán)管和彎頭產品常用的成形方法,它采用專用彎頭推制機、彎頭成形芯棒和感應線圈加熱裝置,使套在模具上的坯料管在推制機的推動下向前運動,進行加熱、擴徑并彎曲成形的過程。
這種成形方式避免了傳統(tǒng)彎管工藝在彎管成形時,因管壁凸邊受拉減薄、管壁凹邊受壓增厚而造成的彎管壁厚不均勻的現(xiàn)象,這對于航空航天用高承壓容器制備具有重要的意義。
在彎頭成形過程中,彎頭芯棒是不可缺少的成形模具。通過合理設計成形芯棒,可使彎頭內外側變形均勻,獲得較好的壁厚均勻性。西北有色金屬研究院鈦合金研究所在開發(fā)某航天用鈦環(huán)形氣瓶內襯過程中,針對所設計的環(huán)管進行了有限元數(shù)值模擬[28]。圖 6a、6b 分別為采用有限元模擬的環(huán)管成形過程中的應力、應變云圖[28]。模擬結果表明,環(huán)
管成形過程中應力應變比較均勻。圖 7a 為制備的TA2 鈦環(huán)形氣瓶內襯,其管徑為 36 mm,外環(huán)直徑為 260 mm,各項技術指標均達到設計要求。采用該技術同時制備了 TA15 鈦合金大規(guī)格環(huán)形高壓氣瓶,如圖 7b 所示。該氣瓶管徑為 100 mm,外環(huán)直徑為700 mm,爆破壓力達到 70 MPa。
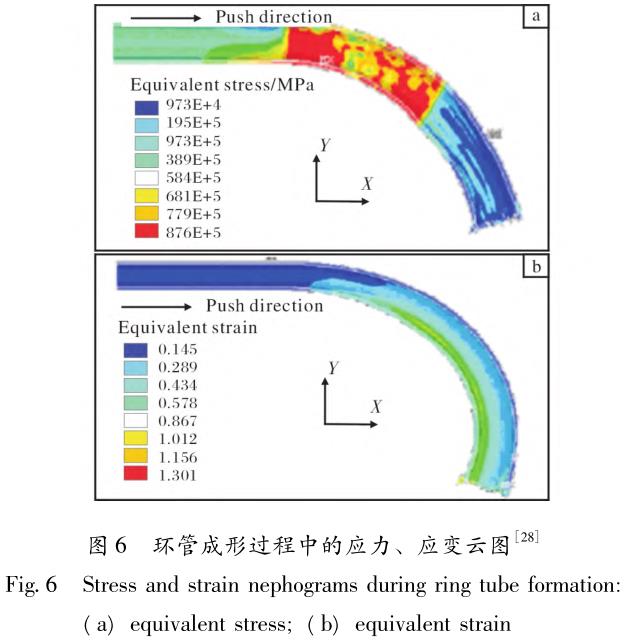
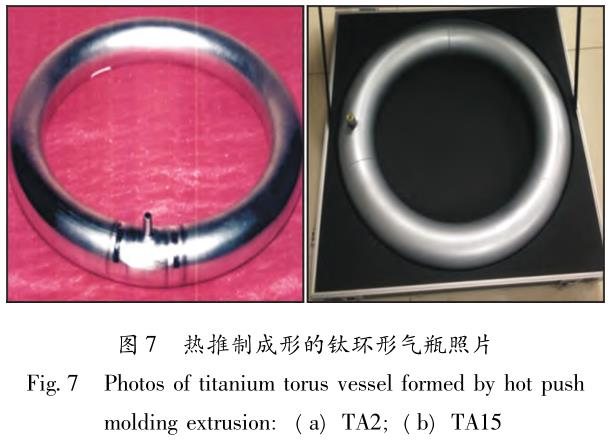
5、熱模鍛成形技術
熱模鍛是鈦合金加工成形的常用方法之一,該方法充分利用鈦合金高溫下流變應力低、易于成形的特性,將其加工成各種形狀的產品。與等溫模鍛相比,熱模鍛的成本更低,生產效率也更高。開始熱模鍛前,需要進行模具設計、坯料準備及熱模鍛工藝參數(shù)的確定。如果按傳統(tǒng)方式通過經驗進行確定,往往不夠精確。而采用數(shù)值模擬方法可以在加工成形前發(fā)現(xiàn)模具和工藝設計中可能存在的問題,通過優(yōu)化工藝參數(shù)提高產品質量,避免人力、物力和時間的浪費。
例如某錐形體由一種新型鈦合金制備,由于缺乏該合金的加工成形經驗,利用有限元軟件對其熱模鍛過程進行數(shù)值模擬,并對結果進行分析。圖 8為錐形體熱模鍛的幾何模型示意圖[29]。
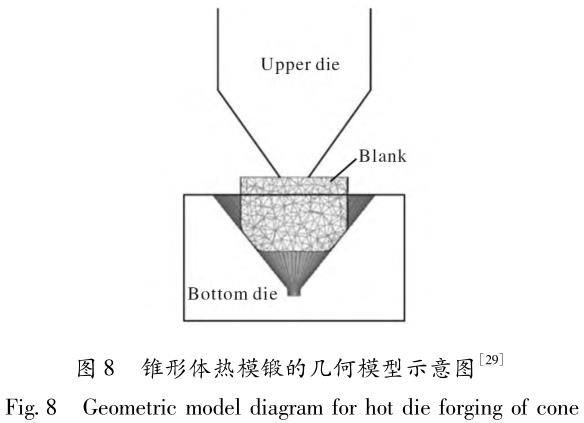
材料成形過程十分復雜,為簡化模擬過程,可以進行一些假設,如不計材料的彈性變形,材料完全均質且各向同性,體積不可壓縮,變形流動服從Levy-Misses 流動原理。熱模鍛過程的數(shù)值模擬結果表明,在錐體成形過程中,塑性變形不均勻,尤其是當變形進入最后階段,坯料變形部分與下模完全貼合,此時再繼續(xù)施加變形時,材料將發(fā)生不均勻減薄。因此,在模具設計時要注意下壓限位裝置的設置。圖 9 為熱模鍛成形的大規(guī)格鈦合金錐形體。
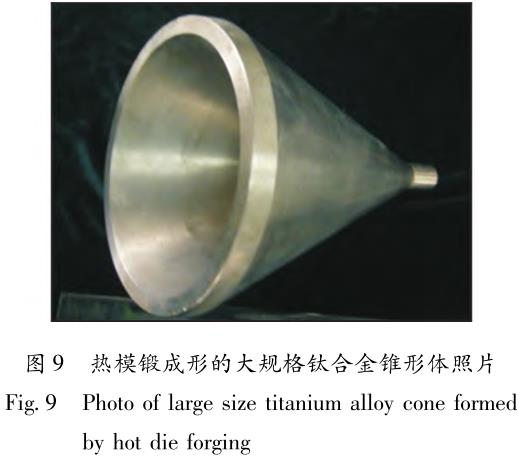
6、結語
西北有色金屬研究院經過多年技術攻關,針對特殊的應用需求,設計并開發(fā)出了適合鈦合金板、棒、管等加工的多項成形技術,制備出了不同形狀、規(guī)格及品種的鈦合金復雜零部件,滿足了多項國防重點工程對鈦合金深加工產品的亟需,同時也推動了鈦合金成形技術的進步。
目前,鈦合金成形技術雖已進入工程應用階段,并展現(xiàn)出巨大的技術經濟效益,但仍以航空航天等工業(yè)為主,應用領域有一定的局限性。如果要廣泛拓展鈦合金的應用領域,必須大幅度提高鈦合金成形加工的效率并降低其成本。將傳統(tǒng)加工成形工藝與目前蓬勃發(fā)展的大數(shù)據(jù)人工智能及數(shù)值模擬預測等新技術進行深度融合,是推進技術進步的有效手段,也將是鈦合金成形技術的發(fā)展方向。
參考文獻References
[1]李軍兆,孫清潔,于航. 高性能鈦合金先進成形技術研究現(xiàn)狀[J]. 鋼鐵釩鈦,2021,42( 6) : 17 - 27.
[2]劉欣,楊景超,李恒,等. 管路構件塑性變形連接技術研究進展及挑戰(zhàn)[J]. 航空學報,2022,43( 4) : 525258.
[3]金和喜,魏克湘,李建明,等. 航空用鈦合金研究進展[J]. 中國有色金屬學報,2015,25( 2) : 280 - 292.
[4]趙永慶. 國內外鈦合金研究的發(fā)展現(xiàn)狀及趨勢[J]. 中國材料進展,2010,29( 5) : 1 - 8.
[5]李梁,孫健科,孟祥軍. 鈦合金的應用現(xiàn)狀及發(fā)展前景[J]. 鈦工業(yè)進展,2004,21( 5) : 9 - 24.
[6]張新,劉鴻羽,車昶,等. 鈦合金低成本成形技術研究進展[J]. 鑄造,2021,70( 10) : 1141 - 1148.
[7]張翥,王群驕,莫畏. 鈦的金屬學和熱處理[M]. 北京:冶金工業(yè)出版社,2009.
[8]劉益民. 304 應變硬化指數(shù)及塑性應變比的測量準確性研究[J]. 山西冶金,2015( 1) : 17 - 21.
[9]洪權,羅國珍,張樹啟,等. Ti-15-3 合金的工藝、性能與晶粒度間關系的研究[J]. 材料工程,1992( S1) : 170- 171.
[10]潘秋紅,張毅峰,王雷剛,等. 冷軋生產工藝對 1100鋁合金板塑性應變比與杯形件制耳率的影響[J]. 機械工程材料,2009,33( 9) : 47 - 50.
[11]龔從揚. 鈦合金板料先進成形制造技術研究進展[J].模具技術,2017( 6) : 48 - 54.
[12]西北有色金屬研究院. 一種高塑性低屈服強度的鈦板的短流程制備方法: CN201711344040. 8[P]. 2018 - 04- 20.
[13]西北有色金屬研究院. 一種薄壁金屬半球壁厚減薄裝置: CN201120266852. 7[P]. 2012 - 3 - 28.
[14]西北有色金屬研究院.一種半球形殼體的成形方法:CN200710083904. 5[P]. 2010 - 12 - 16.
[15]西北有色金屬研究院. 一種鈦合金變壁厚壓力容器殼體的 加 工 方 法:CN200710083905. X[P]. 2010 - 12- 15.
[16]西北有色金屬研究院. 用于鈦合金超薄壁球面零部件環(huán)焊縫自動焊接的夾具: CN201020134212. 6[P]. 2010- 10 - 20.
[17]Liu J,Tan M J,Guo M. Superplastic-like forming of Ti-6Al-4V alloy[J]. International Journal of Advanced Manu-facturing Technology,2013,69: 1097 - 1104.
[18]Baenes A J. Superplastic forming 40 years and still growing[J].Journal of Materials Engineering and Performance,2007,16( 4) : 440 - 454.
[19]張凱峰,王國峰. 先進材料超塑成形技術[M]. 北京:科學出版社,2012.
[20]鄧炬,胡文英,謝麗英. Ti-451 合金在飛行事故記錄儀上的應用[J].稀有金屬材料與工程,1990,19 ( 2) :30 - 33.
[21]王凱旋,郭萍,毛小南,等.一種新型超塑性鈦合金的性能[J]. 材料熱處理學報,2019,40( 9) : 26 - 31.
[22]張永強,毛小南,潘浩,等. 細晶 TA15 鈦合金板材制備工藝及其超塑性研究[J].鈦工業(yè)進展,2018,35( 1) : 20 - 23.
[23]吳以琴,胡文英,昌文華,等.用 Ti-451 合金制造薄壁壓力容器[J]. 稀有金屬材料與工程,1990,19( 1) :30 - 34.
[24]曾立英,趙永慶,李倩.鈦合金低溫超塑性的研究進展[J]. 熱加工工藝,2006,35( 22) : 60 - 65.
[25]曾立英,趙永慶,李丹柯,等.超塑性鈦合金的研究進展[J]. 金屬熱處理,2005,30( 5) : 28 - 33.
[26]趙琳瑜,韓冬,張立武,等. 旋壓成形技術和設備的典型應用與發(fā)展[J]. 鍛壓技術,2007,32( 6) : 18 - 27.
[27]朱曉翠,羅偉,崔文俊. SP700 鈦合金薄板超塑性研究[J]. 湖南有色金屬,2022,36( 1) : 43 - 45.
[28]周偉,周廉,于振濤. TA2 鈦環(huán)形管熱推成形的三維有限元數(shù)值模擬[J].稀有金屬材料與工程,2005,34( 10) : 1585 - 1587.
[29]周偉,葛鵬,趙永慶,等. TC4 合金錐體模鍛過程的數(shù)值模擬[J]. 鈦工業(yè)進展,2010,27( 5) : 19 - 22.
相關鏈接