1、引言
提高鈦合金零件的加工效率、減少零件加工變形一直是鈦合金加工過程中的研究重點。鈦合金高速加工可有效降低零件的變形量,是鈦合金零件加工的研究方向[1]。本文在分析鈦合金異形零件加工方案的基礎上,針對實際加工過程中影響加工效率的問題提出新的工藝方案:采用高速銑削對零件進行粗加工,并根據零件結構特點將零件劃分為不同加工區(qū)域,分析確定各加工區(qū)域的加工順序,對零件進行精加工。通過對工藝的優(yōu)化,使零件加工變形得到了有效控制,而且加工效率得到明顯提高。
2、零件加工方案分析
2.1零件加工方案
如圖1所示,某機型鈦合金零件呈“人”字形,零件外廓尺寸約1000mm×600mm×70mm,零件頭部厚度為27mm,腹板厚度從緊鄰頭部腹板到腿部腹板逐漸減小,緊鄰頭部腹板厚度為6mm,腿部腹板厚度為2mm。
鈦合金異形零件原加工方案為:粗銑外形→粗銑第一面內形→粗銑第二面內形→精銑第二面內形→精銑第一面內形→精銑外形→銑切零件工藝凸臺,所用刀具為立銑刀。零件加工仿真結果見圖2。
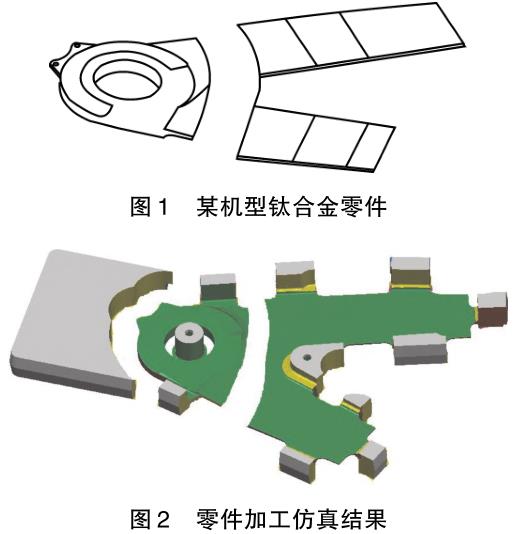
2.2加工方案分析
通過對原加工方案進行分析,提出如下問題:
①鈦合金零件毛料為模鍛件,材料較大,銑外形工作量大,采用上述方案加工零件,毛料最終去除量約占毛坯料重量的70%;銑外形工序的毛料去除量約占毛壞料總去除量的40%。由于銑外形工序為非增值工序(不直接產生生產價值的工序),因此,若將該工序優(yōu)化或取消,將大幅提高零件加工效率;②采用上述方案加工零件,在實際加工過程中,腿部腹板處易發(fā)生翹曲變形,導致零件型面檢測出現(xiàn)問題;③銑外形工序對壓板擺放位置要求嚴格,若壓板位置出現(xiàn)偏差,容易出現(xiàn)刀具與壓板相撞的加工事故。因此,銑外形時,需要操作人員時刻留意刀具與壓板是否會發(fā)生碰撞,浪費大量精力;④分析可知,銑外形工序需要在開敞式機床上進行加工,以便于觀察零件加工狀態(tài),但目前主流機床為封閉或半封閉式機床,無法直觀查看零件的加工狀態(tài),容易出現(xiàn)加工事故。
綜上所述,該零件加工方案急需進行工藝優(yōu)化改進,可優(yōu)化點分析如下:
①由于銑外形工序為非增值工序,加工工作量占總加工工作量比重較大,且銑外形過程中極易出現(xiàn)加工事故,可取消銑外形工序;②立銑刀粗加工零件時,切削深度大,切削速度慢,易造成零件變形,可采用高速銑削進行零件粗加工,留少量余量,再利用立銑刀進行零件精加工;③零件精加工時,腹板厚度不同,剛度不同。若不分區(qū)域加工,薄處腹板容易因相鄰腹板不能提供足夠剛度而發(fā)生振顫,需根據腹板厚度,結合零件自身結構特點進行加工區(qū)域劃分,并合理規(guī)劃各區(qū)域加工順序進行零件精加工。
3、零件加工工藝優(yōu)化
通過對零件加工方案進行分析,結合可優(yōu)化點分析,從工藝流程優(yōu)化、粗加工優(yōu)化及精加工優(yōu)化三個部分對該鈦合金異形零件進行加工工藝優(yōu)化。
3.1加工工藝流程優(yōu)化
鈦合金異形零件在銑切外形時存在諸多弊端,因此,在工藝流程優(yōu)化過程中,取消銑切外形工序,直接進行零件內形的加工,并在加工過程中引入鈦合金高速銑削加工技術。
優(yōu)化后的加工工藝流程見圖3。具體加工過程:①采用高速銑削加工技術進行零件粗加工,以減小因毛料去除量大所引起的加工變形;②根據零件結構特點對零件加工區(qū)域進行劃分及排序,完成零件精加工。
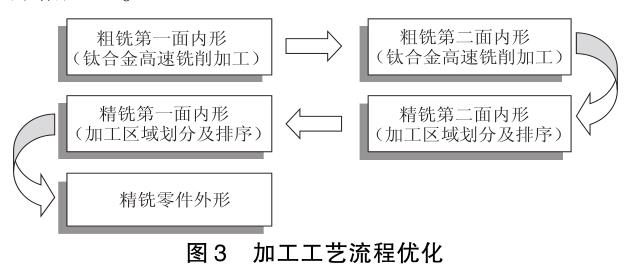
3.2鈦合金高速銑削加工技術
切削線速度達到100m/min以上的鈦合金切削方式被稱為高速切削[2]。高速銑削是鈦合金零件銑削加工的發(fā)展方向,具有加工效率高、切削熱量少及切削振動小的特點[3],不僅能夠提高零件加工效率,還可有效減小零件變形量。
由于零件腿部腹板較薄,粗加工材料去除量大,在實際加工中極易發(fā)生翹曲變形,因此將高速銑削引入零件粗加工過程,充分利用高速銑削中切削力小、引起零件變形量小的特點進行該鈦合金異形零件的粗加工。該鈦合金異形零件高速銑削粗加工時,使用?63R4淺切刀,考慮到零件最終的表面粗糙度及光度要求,零件粗加工后留0.5mm余量,利用立銑刀進行精加工,加工參數(shù)設置見表1。

3.3零件加工區(qū)域劃分及加工順序規(guī)劃
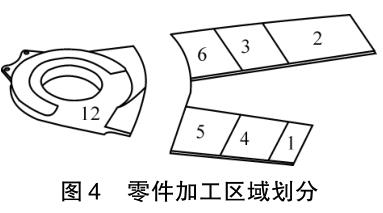
該鈦合金異形零件的腹板厚度從緊鄰頭部腹板到腿部腹板逐漸減薄,緊鄰頭部腹板厚度為6mm,腿部腹板厚度為2mm。在精加工過程中,為保證腹板在加工時的剛度要求,避免發(fā)生振顫造成厚度超差,根據零件自身結構特點,將腹板劃分為12個區(qū)域(見圖4)。加工順序由小到大排列,加工腹板厚度由薄到厚,使得在加工薄處腹板時,相鄰腹板面可為其提供足夠剛度,從而避免發(fā)生震顫。該零件頭部厚度為27mm,不存在切削震顫問題,放至最后加工,采用?25R4硬質合金刀具進行精加工。該鈦合金異形零件正反面結構類似,均采用相同的區(qū)域劃分方法進行加工。采用優(yōu)化后的工藝方案加工零件,不僅將零件加工效率提升40%,還避免了零件腿部腹板發(fā)生翹曲變形,該優(yōu)化方案已成功應用到實際加工中。利用優(yōu)化后的方案加工零件,仿真結果見圖5。
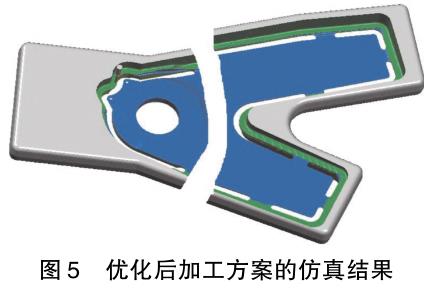
4、結語
提高鈦合金零件加工效率和減小零件加工過程中的變形是鈦合金零件加工過程中的重要研究課題。針對某機型鈦合金異形零件加工方案所存在的問題,提出加工工藝優(yōu)化方法:將高速銑削技術應用到鈦合金異形零件粗加工過程中,并根據零件特點將腹板進行區(qū)域劃分,規(guī)劃各區(qū)域加工順序,進行零件精加工。
采用優(yōu)化后工藝方案加工零件發(fā)現(xiàn),加工效率明顯提升。本文工藝優(yōu)化分析方法對后續(xù)類似結構的鈦合金零件加工具有一定借鑒意義。
參考文獻
[1]王曉明,韓江.TC4鈦合金高速銑削表面粗糙度研究[J].機械設計與制造,2019(5):232-240.
[2]耿國盛.鈦合金高速銑削技術的基礎研究[D].南京:南京航空華天大學,2006.
[3]趙勛,屈植華,王社權,等.鈦合金高速銑刀的開發(fā)及試驗研究[J].工具技術,2018,52(8):77-82.
第一作者:卜慶奎,碩士,工程師,沈陽飛機工業(yè)(集團)有限公司,110850沈陽市
FirstAuthor:BuQingkui,Master,Engineer,ShenyangAir?craftCorporation,Shenyang110850,China
相關鏈接