引言
磁控濺射是一種被廣泛應(yīng)用于薄膜制備和表面改性的高效物理氣相沉積技術(shù)。在磁控濺射過程中,靶材受到離子轟擊,產(chǎn)生高能量的離子和中性粒子,從而使靶材表面的原子或分子被剝離并沉積到基底表面,形成所需的薄膜[1]。而濺射靶材的微觀結(jié)構(gòu)對于薄膜質(zhì)量起著至關(guān)重要的作用。為了實現(xiàn)所需的薄膜特性,必須精確調(diào)節(jié)靶材的純度、相對密度、晶粒尺寸和晶粒取向等因素。金屬污染和孔隙存在也會對薄膜電阻率產(chǎn)生不利影響[2]。此外,無擇優(yōu)取向的濺射靶材可用于沉積光滑且連續(xù)的薄膜,而較小晶粒尺寸也已被證明可以提高濺射速率[3]。
鎢基合金是磁控濺射常用靶材之一,因其具有優(yōu)良的熱穩(wěn)定性、化學(xué)穩(wěn)定性和機械性能,在先進光學(xué)涂層、半導(dǎo)體行業(yè)等應(yīng)用領(lǐng)域中具有重要的地位。因此,鎢基合金靶材在先進光學(xué)涂層、半導(dǎo)體行業(yè)等領(lǐng)域中扮演著至關(guān)重要的角色[4]。同時,由于鎢及其合金通常具有較高的熔點,因此一般采用粉末冶金來替代傳統(tǒng)的熔煉鑄造來制備粉末冶金靶材。使用納米尺寸的顆粒可以提高高熔點金屬粉末基燒結(jié)體的相對密度。近年來,鎢基合金靶材及其磁控濺射薄膜也受到了廣泛關(guān)注和深入研究,例如:W-Mo靶材[5],W-B靶材[6],W-S[7],W-Cu[8,9]靶材等等。本文介紹了鎢基合金靶材的制備方法以及其在磁控濺射薄膜性能和應(yīng)用領(lǐng)域方面的最新進展。
1、鎢基合金靶材的粉末冶金制備工藝
粉末冶金法是制備鎢基合金靶材最常見的方法,通常先將鎢粉與其他合金粉末按比例混合,然后通過球磨或機械合金化等方法使其均勻混合。隨后,將混合粉末置于模具中壓制成坯料,最終進行燒結(jié)處理以獲得靶材。由于燒結(jié)方法不同,通常分為熱壓、熱等靜壓、放電等離子燒結(jié)等方式[10]。
1.1熱壓技術(shù)((HP)
熱壓燒結(jié)同時進行加熱和加壓,使粉料處于熱塑性狀態(tài),有利于顆粒的接觸擴散和流動傳質(zhì)過程,因此成型壓力僅為冷壓的1/10;同時能降低燒結(jié)溫度、縮短時間,并抵制晶粒長大,得到晶粒細(xì)小、致密度高以及機械、導(dǎo)電性能良好的產(chǎn)品,并且熱壓燒結(jié)可以大概分為真空熱壓和惰性氣體熱壓兩種氣氛條件[11,12]。
黃志明等[13]利用平均粒度為7μm的鎢硅混合粉末,以10℃.min-1的升溫速率,在1200℃的真空熱壓條件下保溫1~3h,成功制備出了組織結(jié)構(gòu)均勻且相對密度≥99%的高純鎢硅靶材。
如圖1所示,可以看出靶材的組織結(jié)構(gòu)均勻且無明顯孔洞(顏色較淺的區(qū)域為WSi2,顏色較深的區(qū)域為Si)。Dunlop等[14]采用TiH2粉末與W粉混合,在1350℃、35MPa的真空熱壓條件下制備了致密度約為99%的W-Ti合金靶材。通過TiH2脫氫時對碳、氧等氣體的吸附作用,使總氣體含量小于0.085%(質(zhì)量分?jǐn)?shù)),碳含量少于0.01%(質(zhì)量分?jǐn)?shù)),從而減少磁控濺射薄膜產(chǎn)生顆粒數(shù)量。Wang等[15]運用真空熱壓燒結(jié)技術(shù)成功制備了致密度達到97.8%的W-10%Re高純合金靶材。此外還有Xu等[16]采用熱壓微波燒結(jié)制備鎢銅合金,Ma等[17]通過真空反應(yīng)熱壓法從元素鎢和無定形硼粉末合成四硼化鎢。

熱壓燒結(jié)具有較高的經(jīng)濟效益,因而成為目前最常用的粉末冶金技術(shù)。上述研究表明,通過熱壓燒結(jié)所得到的鎢基合金靶材大多具有較高的致密度和較均勻的組織結(jié)構(gòu),所以目前商業(yè)化的鎢基合金靶材大多都是通過熱壓技術(shù)制備和生產(chǎn)的。
1.2熱等靜壓技術(shù)((HIP)
熱等靜壓技術(shù)(HotIsostaticPressing,HIP)是一種高溫高壓制備工藝,其主要用于制造高性能金屬、陶瓷和復(fù)合材料等工程材料[12]。該技術(shù)通過將待加工的材料置于高溫高壓下,并實施均勻的加壓和溫度控制,使得材料在壓力和溫度作用下達到等靜壓狀態(tài)。在這種狀態(tài)下,材料內(nèi)部的氣孔、微裂紋和其他缺陷會被均勻地壓實和填充,從而提高了材料的密度和均勻性[18]。
Wickersham等[19]利用熱等靜壓(HIP)技術(shù)制備了鎢鈦合金靶材,并在高壓條件下發(fā)現(xiàn),溫度超過885℃會導(dǎo)致富含鈦相的形成。對于在885℃至740℃溫度范圍內(nèi)制備的靶材,富含鈦相的生成取決于具體的加工工藝。當(dāng)溫度低于740℃時,不會形成富含鈦相,并且靶材密度接近100%。此外Hu等[20]研究了熱等靜壓工藝參數(shù)對鎢合金性能和斷裂行為的影響,Li等[21]通過噴霧干燥技術(shù)和熱等靜壓制備了接近理論密度(99.69%)和高電導(dǎo)率(86.78%IACS)的Cu-20%(質(zhì)量分?jǐn)?shù))W(Cu-20W)復(fù)合材料。
綜上所述,由于HIP制備鎢基合金靶材需要嚴(yán)格的高壓條件和較高生產(chǎn)成本,因此大多數(shù)情況下仍停留在實驗階段而未能實際應(yīng)用于生產(chǎn)。
1.3放電等離子燒結(jié)技術(shù)((SPS)
放電等離子燒結(jié)(SPS,SparkPlasmaSintering)技術(shù)是一種高效的粉末冶金制備技術(shù),它是一種結(jié)合了電熱效應(yīng)和機械效應(yīng)的新型壓固工藝,能夠在相對較短的時間內(nèi)實現(xiàn)高密度、高強度的材料制備[12];該技術(shù)主要原理是利用電流在導(dǎo)電材料中產(chǎn)生的局部加熱效應(yīng),結(jié)合機械壓力,實現(xiàn)材料的快速燒結(jié)和致密化[22]。
Mo-W合金非常適合電子、納米技術(shù)、傳感器和TFT-LCD柵電極的應(yīng)用[23],但是熔煉法不適用于熔點較高的金屬和金屬合金,例如Mo、W及其合金[24],所以Kim等[5]利用SPS技術(shù)在1400℃條件下制備出了高純度鎢鉬合金靶材,其致密度高于99%。研究發(fā)現(xiàn),使用Mo和W高能球磨的納米粉末制備的樣品相對密度較低,分別為97.04%、97.17%和98.55%,而氧化物還原的納米粉末制備的樣品在相同溫度下表現(xiàn)出更高的燒結(jié)相對密度分別為98.21%、99.28%和99.62%。圖2展示了氧化物還原粉末制備并在1300℃以上燒結(jié)后的壓坯具有光滑晶界和致密微觀結(jié)構(gòu)。
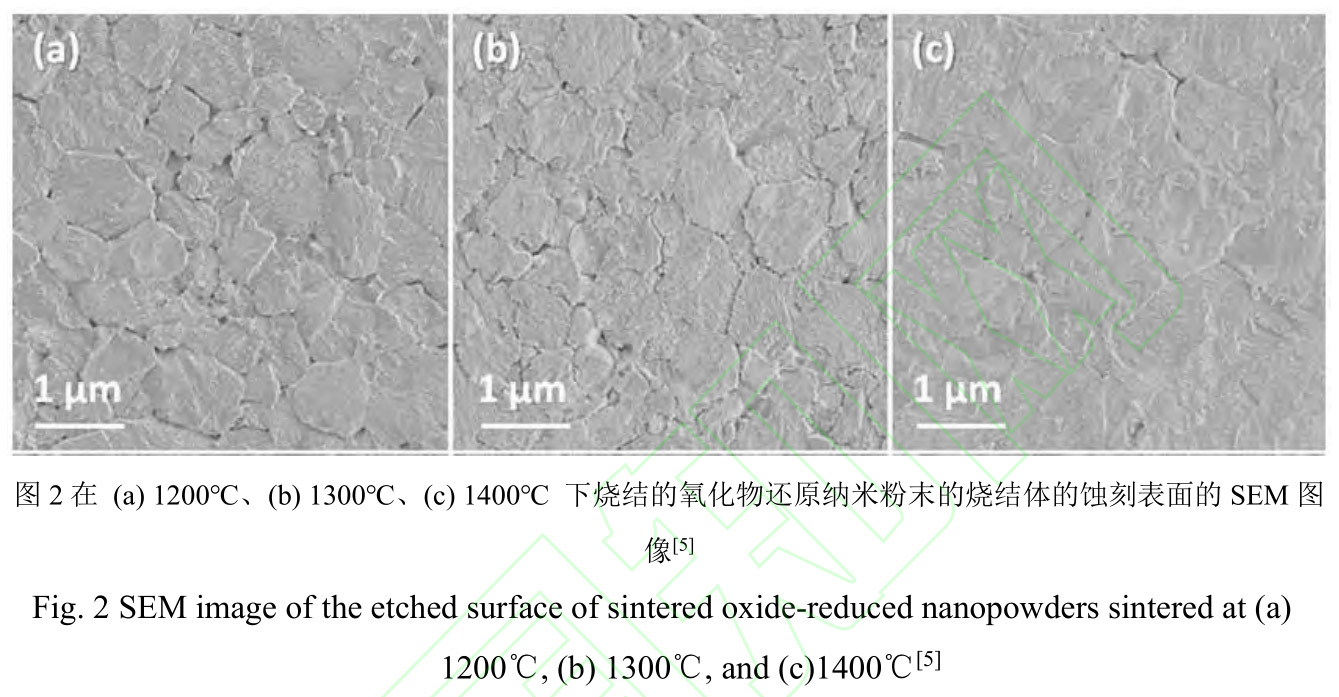
綜上所述,由于目前SPS在鎢基靶材的制備中相關(guān)研究較少;需制備的靶材尺寸越大,對SPS設(shè)備的壓力和功率要求也越高,因而采用SPS規(guī)模生產(chǎn)濺射靶材受設(shè)備限制的情況尚待解決。
從現(xiàn)有的研究發(fā)現(xiàn),無論是SPS還是HIP,目前由于其較高的使用成本或是較為嚴(yán)苛的使用條件,暫時都還無法大規(guī)模的用于工業(yè)生產(chǎn),相較于這兩種制備方法HP經(jīng)過了數(shù)十年的發(fā)展已經(jīng)十分完善,其經(jīng)濟效益都相對較高,但同時也是由于其多年的發(fā)展,通過其制備的靶材很難有太多的創(chuàng)新及改善。所以筆者認(rèn)為未來鎢基合金靶材的發(fā)展的未來還是在于新型的工藝技術(shù),將會有更多先進的工藝如增材制造(3D打?。25,26]、等離子燒結(jié)[27]等應(yīng)用于鎢基合金靶材的制備中。
2、磁控濺射薄膜的應(yīng)用及特性
磁控濺射技術(shù)是在20世紀(jì)60年代和1970年代開發(fā)的,此后一直是等離子體濺射沉積的主要方法。多年來,磁控濺射技術(shù)不斷發(fā)展,以增加金屬電離、提高靶材利用率、避免反應(yīng)濺射中的靶材中毒、提高沉積速率,并最大限度地減少電弧的電不穩(wěn)定性,并降低運營成本[28]。功能性涂層和層狀結(jié)構(gòu)需求持續(xù)增長,促使整體質(zhì)量和功能不斷提高。濺射沉積工藝的發(fā)展得到推動,因為需要提高濺射源利用率、沉積薄膜均勻性、實現(xiàn)金屬定向沉積以及滿足控制需求。離子轟擊基材能量影響成膜材料,而磁控濺射已成為廣泛應(yīng)用于工業(yè)中的重要技術(shù)[29]。
2.1鎢基合金薄膜的應(yīng)用領(lǐng)域
2.1.1W-Ti/CoW無擴散屏障材料
集成電路(IntegratedCircuit,IC)是一種微型電子器件,它將大量的電子元件(如晶體管、電阻、電容等)集成到一個單一的半導(dǎo)體芯片上,通過特定的電路連接方式實現(xiàn)了各種功能,例如放大、邏輯運算、存儲和控制等[30]。磁控濺射鎢基合金薄膜在半導(dǎo)體集成電路中具有多種重要應(yīng)用,用于連接、阻抗調(diào)節(jié)、電極結(jié)構(gòu)和介電層等方面,對于提高集成電路的性能、穩(wěn)定性和可靠性具有重要意義[31]。
目前,含Ti量為10%(質(zhì)量分?jǐn)?shù))~30%(質(zhì)量分?jǐn)?shù))的W-Ti合金已成功應(yīng)用于Al、Cu和Ag布線技術(shù)[19]。作為擴散阻擋層材料,W-Ti薄膜不僅可穩(wěn)定擴散阻擋層,還可以作為反應(yīng)型擴散阻擋層。它與硅有良好的粘附性,并且對Cu的擴散阻擋作用尤為明顯[32]。
Guidi等[33]利用W-30%Ti靶材,采取磁控濺射方式在導(dǎo)電金屬Ag和基體Si之間鍍了一層W-Ti薄膜,并進行了熱處理。觀察到以下現(xiàn)象:溫度接近700℃時,薄膜中的銀原子開始大量聚集,并導(dǎo)致了硅的生成,從而使薄膜的電阻系數(shù)迅速增加。這表明,W-Ti薄膜不僅在低溫下有效阻擋了銀布線與單晶硅之間的擴散,而且還展現(xiàn)出潛在的高溫應(yīng)用價值。同時,Su等[34]發(fā)現(xiàn)50%(質(zhì)量分?jǐn)?shù))的CoW合金磁控濺射薄膜具有與目前主流銅互連中的擴散屏障材料TaN相似的抗擴散能力和潤濕能力,并且在CoW薄膜上接近70nm的孔洞也滿足Cu在其上面的鑲嵌要求,表明其可能作為下一代Cu互連單層無籽勢壘的有前途候選者。
如圖3所示,在CoW襯底上初始階段核密度高于Ta、TaN或W襯底,并且隨電鍍時間增加呈均勻變化。因此,在這種情況下可以在CoW基板上實現(xiàn)連續(xù)且光滑的Cu膜。
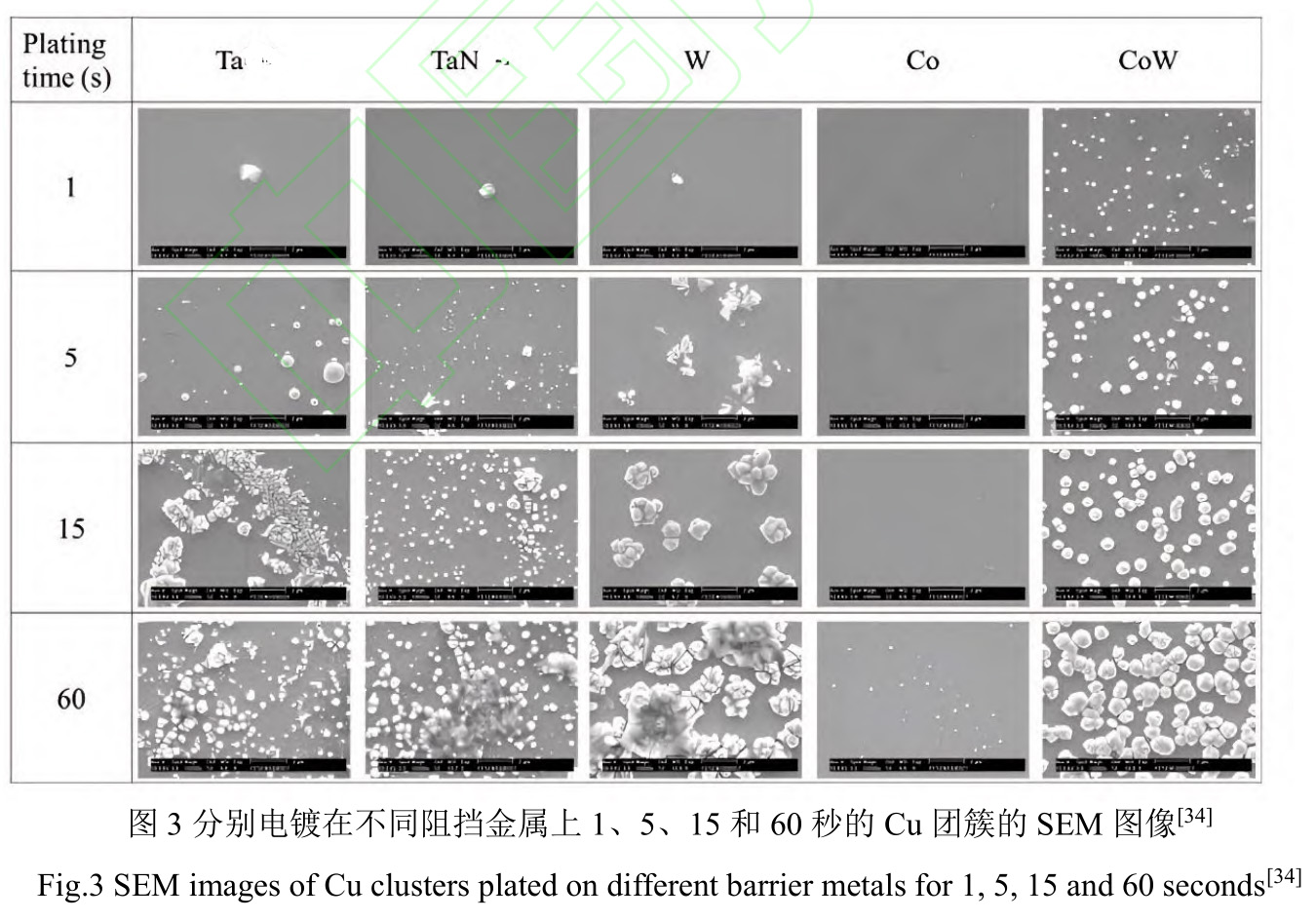
綜上所述,由于鎢具有較強抗原子擴散的能力,目前的研究中大多都是以鎢為基體應(yīng)用于集成電路的抗擴散阻擋層材料,添加的其它元素大多起到增加粘附性的作用,有些元素也起到少量的抗擴散作用例如Ti等[34]。
2.1.2W-Si超導(dǎo)材料
超導(dǎo)材料是一類在低溫下表現(xiàn)出超導(dǎo)現(xiàn)象的材料。當(dāng)這些材料被冷卻到臨界溫度以下(即超導(dǎo)臨界溫度)時,其電阻突然變?yōu)榱?,并呈現(xiàn)完全的電子輸運現(xiàn)象[35]。鎢(W)和硅化鎢(WSi2)具有低電阻率、抗應(yīng)力遷移和強電遷移能力等優(yōu)點,因此成為當(dāng)前研究的熱點。Suzuki等人[36]利用低壓化學(xué)氣相沉積(LPCVD)方法,使用六氟化鎢(WF6)和硅烷(SiH4)制備的W薄膜顯著提高了超導(dǎo)轉(zhuǎn)變溫度。隨后Kondo[37]通過磁控濺射技術(shù)和熱擴散技術(shù)成功制備出W-Si和W-Ge非晶超導(dǎo)薄膜,使用LPCVD時,膜在高達354°C的溫度下沉積,并表現(xiàn)出超導(dǎo)性。同時發(fā)現(xiàn)濺射和熱擴散對于獲得具有高熱穩(wěn)定性的非晶態(tài)W-Si也是有效的,并且分析了W-Si和W-Ge薄膜中準(zhǔn)金屬含量與電子特性和晶體結(jié)構(gòu)的關(guān)系。這些材料不僅適用于現(xiàn)有超大規(guī)模集成電路(ULSI)應(yīng)用,也適用于未來大規(guī)模集成超導(dǎo)晶體管的材料。
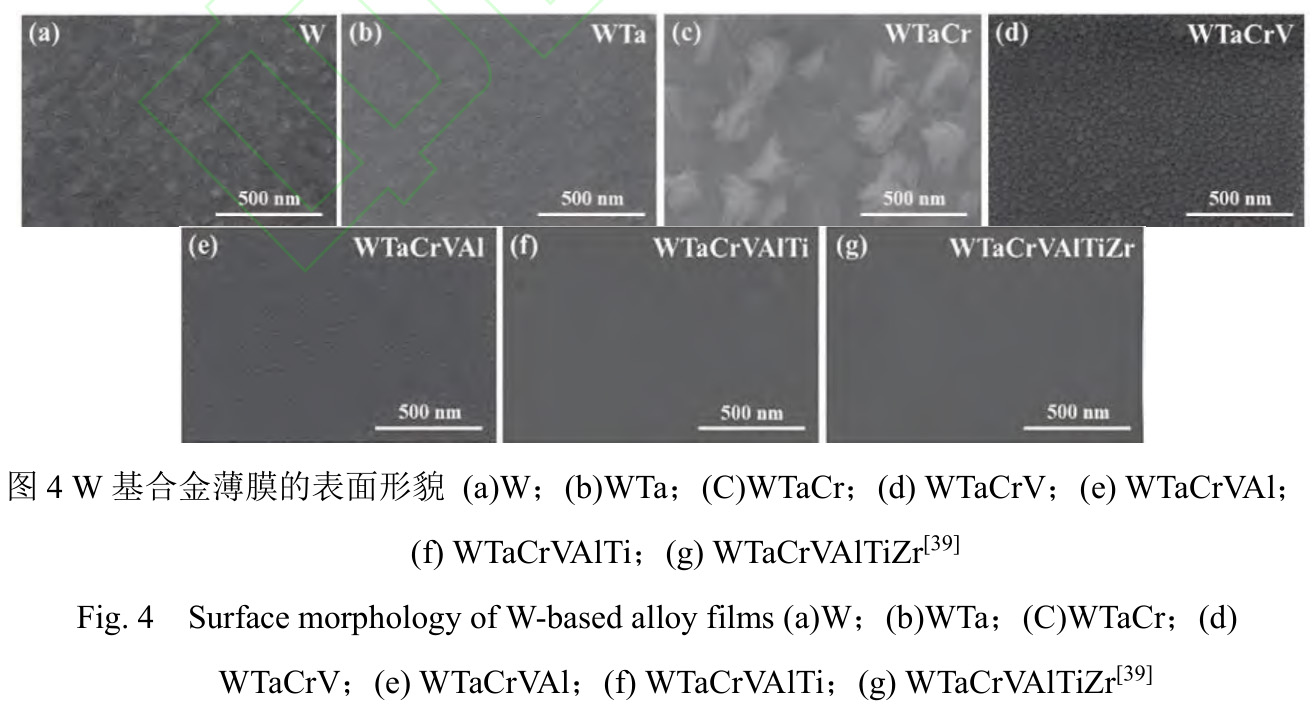
2.1.3WTaCrVAlTiZr面向等離子體材料((PFM)
等離子體材料的研究和開發(fā)對核聚變能、等離子體物理研究以及等離子體噴涂技術(shù)具有重要意義。面向等離子體材料是指用于等離子體物理研究和應(yīng)用的材料,其特性和性能在等離子體環(huán)境中起著關(guān)鍵作用[38]。鎢因其高熔點、低熱膨脹系數(shù)、高電阻率和低中子活化而被視為未來聚變裝置中最重要的面向等離子體材料(PFM)候選材料[39],同時高溫抗氧化性是PFM的重要安全標(biāo)準(zhǔn),自鈍化鎢合金和表面涂層保護技術(shù)可以使鎢合金具有優(yōu)異的抗氧化性和耐腐蝕性。Zhang等[39]人利用磁控濺射技術(shù)成功制備了一系列連續(xù)添加元素的W基合金薄膜。實驗結(jié)果顯示,當(dāng)合金中加入Al和Ti時,其抗氧化能力顯著提高。此外,Zr元素可顯著增強鍍層的抗氧化性能、提高膜層附著力,并改變其生長機制以降低氧化速率。同時WSi2涂層呈現(xiàn)出致密且典型的雙層微觀結(jié)構(gòu),具有顯著的抗氧化性能。
2.1.4W-B硬質(zhì)涂層
刀具的硬質(zhì)涂層是一種將優(yōu)異硬度和耐磨性材料覆蓋在刀具表面以增強其性能的技術(shù)。這些涂層通常由碳化鎢(WC)[40]、氮化鈦(TiN)、氮化鋁(AlN)[41]、碳化硅(SiC)等硬質(zhì)材料制成[42],被廣泛應(yīng)用于鉆頭、銑刀、車刀、切削工具等,以提高其性能和使用壽命。
Chrzanowska等[43,44]觀察到了相似的特性,他們研究了平面不銹鋼基材上αWB涂層的摩擦系數(shù)和耐磨性。通過射頻磁控濺射(RFMS)沉積的αWB薄膜具有良好的附著力。Jiang等人[45]表明,直流磁控濺射(DCMS)制備出具有亞穩(wěn)態(tài)AlB2型結(jié)構(gòu)的αWB2涂層,其納米復(fù)合材料結(jié)構(gòu)表現(xiàn)出約43.2±5GPa的超硬度。Radziejewska等[46]在商用WC-Co切削刀片上通過射頻磁控濺射沉積了WBx和(W,Ti)B2涂層,如圖5所示。在難切削304不銹鋼車削試驗中,W-B涂層刀具比未涂層刀具表現(xiàn)出更好的耐磨性,并且與未覆蓋WC-Co刀片相比,覆蓋W-B薄膜后刀面磨損量減少了30%,此外,在測試條件下保護了邊緣碎裂情況發(fā)生。
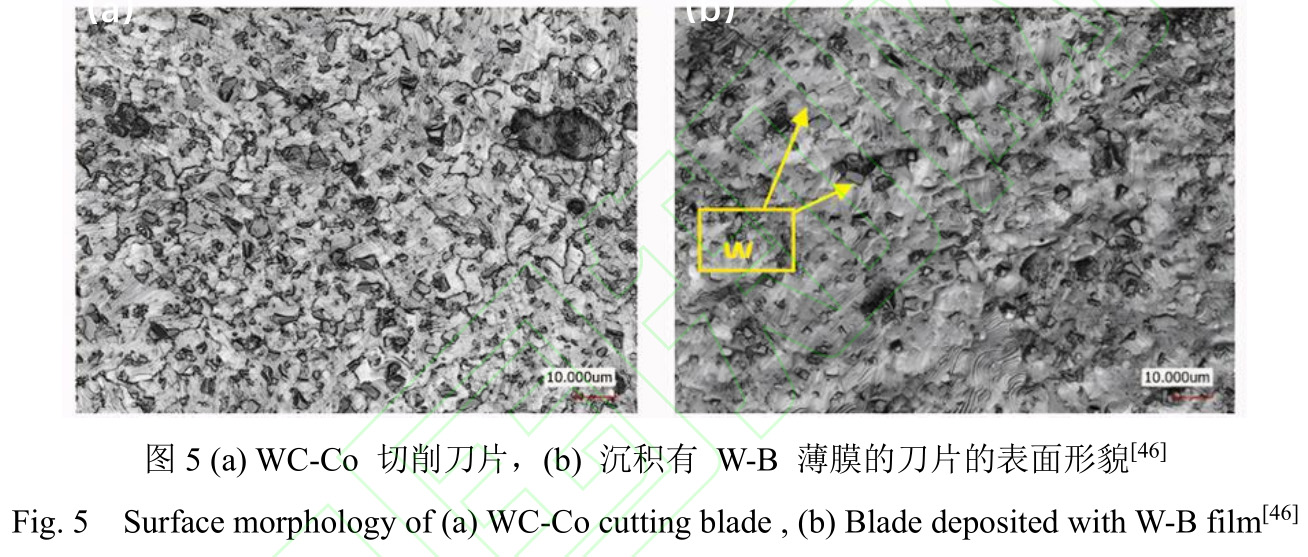
2.2鎢基合金薄膜的性能分析
2.2.1抗擴散性能
鎢基合金薄膜主要應(yīng)用于電子器件、半導(dǎo)體和集成電路板等領(lǐng)域。其中,鎢基合金薄膜的關(guān)鍵性能在于其抗擴散特性。由于鎢元素具有高熔點、低擴散系數(shù)、穩(wěn)定晶體結(jié)構(gòu)和化學(xué)惰性等特點;因此,使得鎢基合金薄膜在高溫環(huán)境下能夠保持較好的結(jié)構(gòu)穩(wěn)定性,并且具有抵抗擴散現(xiàn)象的特點[47]。目前在抗擴散領(lǐng)域,磁控濺射的WTi合金薄膜是應(yīng)用最廣泛[32]。
其中,鎢起主要的抗原子擴散作用,鈦則主要加強薄膜的耐腐蝕性能。此外,還有用于銅互連應(yīng)用的磁控濺射CoW薄膜[3]。鎢元素增強了對銅的抗擴散能力,并且可以抑制薄膜的氧化和損壞。如圖6所示,隨著鎢含量增加,失效溫度也相應(yīng)提高。失效溫度升高意味著優(yōu)異的抗擴散能力,因為銅在達到擴散溫度之前會更長時間保持穩(wěn)定狀態(tài);而作為銅粘附層的鈷表現(xiàn)出良好粘結(jié)性能。
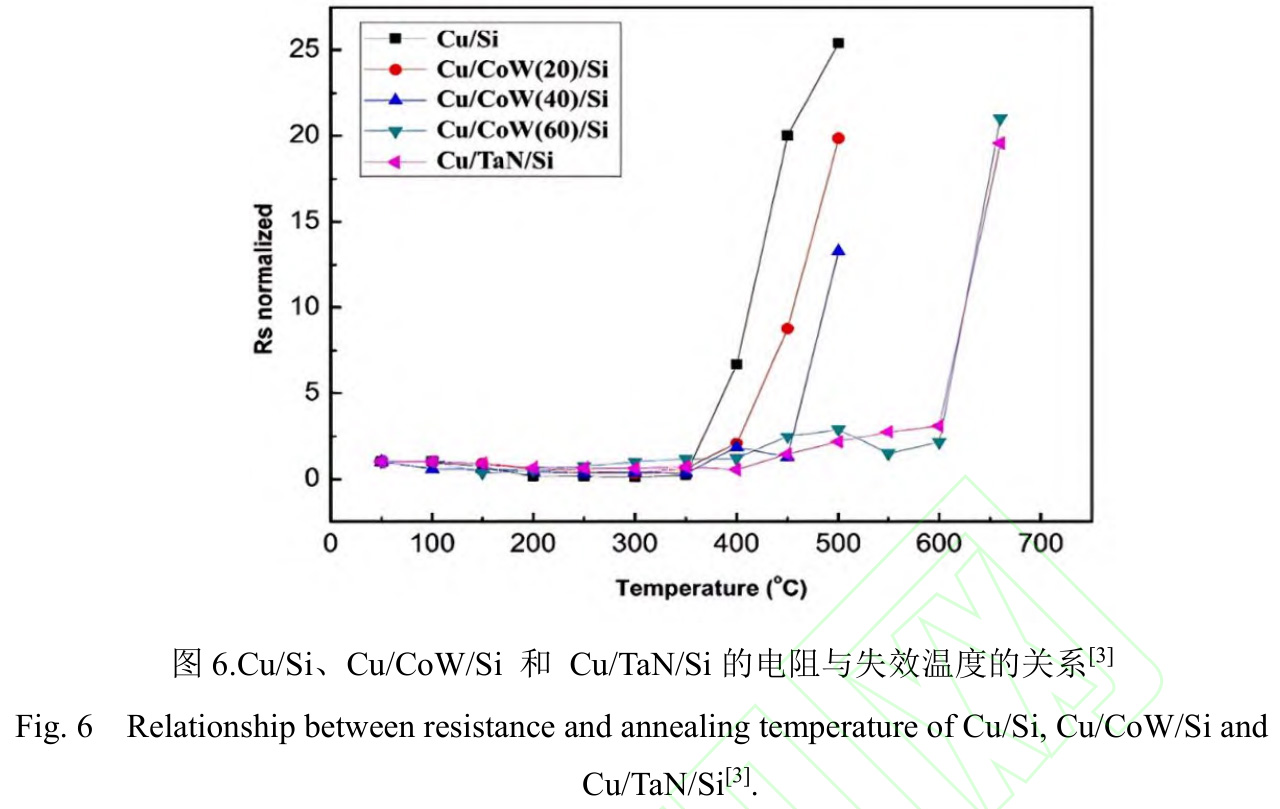
2.2.2摩擦磨損性能
磁控濺射制備的鎢基合金薄膜具有高硬度、低摩擦系數(shù)、耐高溫性和化學(xué)惰性等優(yōu)異的摩擦磨損性能,例如W-N[48]、W-Zr[49]、W-B[50]等。Jiang等人[45]磁控濺射所制備的W-B薄膜具有亞穩(wěn)態(tài)AlB2型結(jié)構(gòu)的直流磁控濺射αWB2涂層表現(xiàn)出約43.2±5GPa的超硬度。在這種情況下,滑動過程中測得的穩(wěn)態(tài)摩擦系數(shù)為0.23,薄膜的磨損率為6.5×10?6mm3·N?1·m?1,表明其具有優(yōu)異的摩擦磨損性能。Euchner等[51]發(fā)現(xiàn)通過磁控濺射在整個成分范圍內(nèi)沉積的Ti1?xWxB2?z固溶體薄膜均以AlB2結(jié)構(gòu)類型結(jié)晶,并且表現(xiàn)出良好的熱穩(wěn)定性和40GPa左右的高硬度。同時Smolik等[52]觀察到添加10%(質(zhì)量分?jǐn)?shù))鎢元素可使二硼化鈦涂層斷裂韌性KIC增加7倍以上,從KIC(TiB2)=0.67增加到KIC(TiBW)=4.98MPa·m1/2。與TiB2涂層相比,Ti-B-W薄膜具有更高的硬度(400mN載荷下H=38GPa)和相似的表面粗糙度。
此外,在文中提及了W-B薄膜耐磨性優(yōu)于Ti-B-W薄膜,如表1所示。
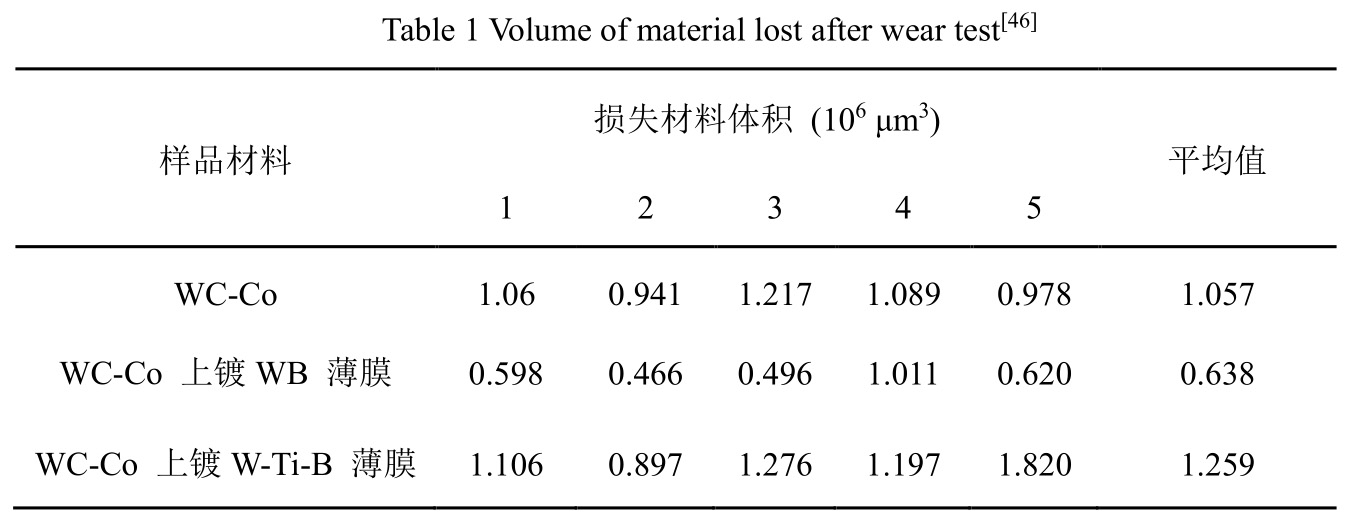
從以上可以看出鎢作為高硬度,低摩擦系數(shù)的金屬,以其合金作為靶材所制備出的薄膜同樣也擁有著優(yōu)異的摩擦磨損性能,從中可以看出使用它們來保護難加工材料的WC-Co切削刀具的可能性。
2.2.3抗腐蝕氧化性能
在過去幾十年中,針對機械應(yīng)用的鎢基合金硬質(zhì)涂層進行了大量研究。除了具有非常高的硬度和附著力外,鎢基合金涂層還需要具備抗腐蝕性和抗氧化性,在使用溫度達到數(shù)百攝氏度時不會失效[53]。例如,WSi2磁控濺射涂層呈現(xiàn)出致密且典型的雙層微觀結(jié)構(gòu),其優(yōu)異的抗氧化性能源于表面致密、光滑[54]。Louro等人[50]對W-N-M(M=Ni和Ti)濺射涂層的沉積和氧化行為進行了詳細(xì)分析,發(fā)現(xiàn)W-Ti薄膜良好的抗氧化性歸因于在氧化層晶界中以非常細(xì)小的顆粒形式形成TiO2,這有助于阻礙氧離子向內(nèi)擴散。另一方面,對于含鎳薄膜,如果Ni含量足夠高以促進足夠厚的NiWO4層,則NiWO4尖晶石型相外層的形成可以產(chǎn)生優(yōu)異的抗氧化行為。Zhang等[39]采用磁控濺射方法制備了一系列連續(xù)添加元素的W基合金薄膜。從圖7和圖8可以看出,隨著元素數(shù)量增加,W基合金薄膜表面形貌逐漸變得光滑,并且其耐酸堿的腐蝕性和抗氧化性也逐漸提高。
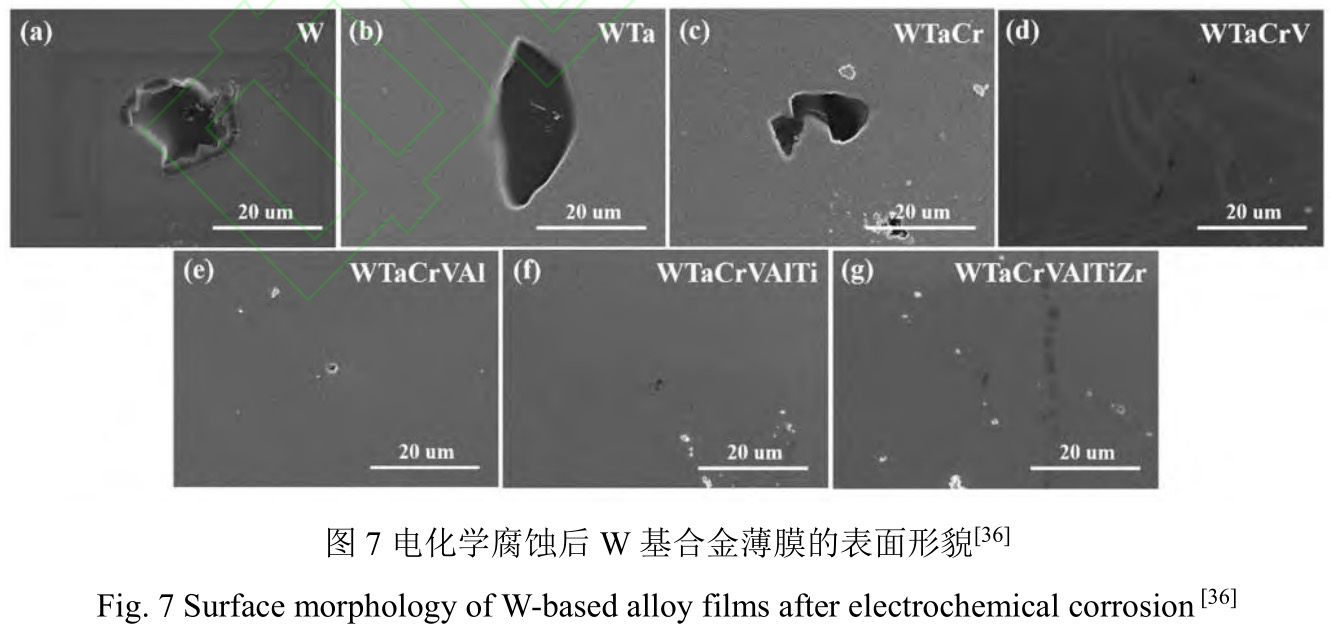
綜上所述,隨著元素數(shù)量的增加,膜層的耐腐蝕性和抗氧化性逐漸提高。混合熵的增加降低了吉布斯自由能,使鎢基合金更加穩(wěn)定,是耐腐蝕性和抗氧化性同時提高的重要原因之一。此外,Cr、Al、Ti、Zr元素具有較強的鈍化作用,易于形成致密的氧化膜,這也是提高耐蝕性和抗氧化性的重要原因。這也使得未來鎢基合金薄膜作為硬質(zhì)涂層擁有廣闊的發(fā)展前景。
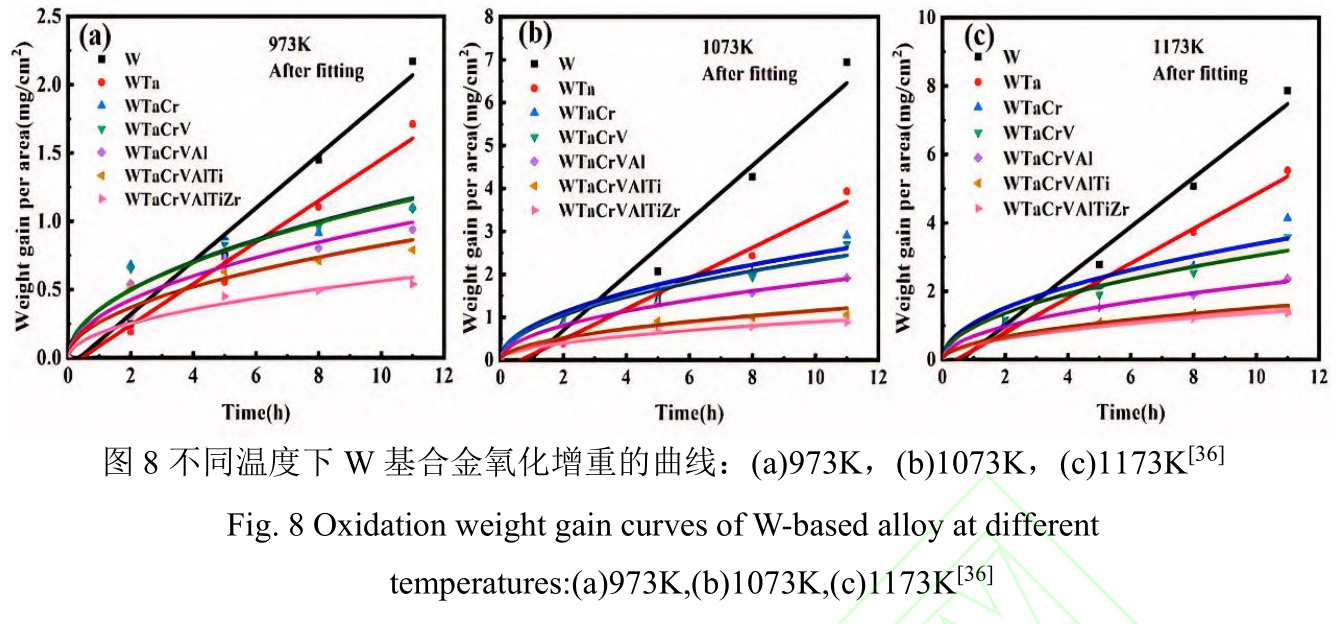
3、展望
磁控濺射鎢基合金薄膜具有優(yōu)異的抗擴散性能、摩擦磨損性能、抗腐蝕氧化性能等多項優(yōu)異性能,使其在集成電路、硬質(zhì)合金涂層和等離子材料方面具有重要應(yīng)用和研究價值。我國近年來加快了對鎢基合金合金靶材的研究與應(yīng)用,雖然目前真空熱壓仍然是是鎢基合金靶材的主要制備技術(shù),但也有一些在此領(lǐng)域還少有研究的技術(shù)(如SPS技術(shù))用于鎢基合金靶材的制備研究。
未來主要的發(fā)展方向有幾個,首先是制粉,粉末的晶粒大小直接影響其燒結(jié)合金的多項性能,例如合金的致密度,導(dǎo)電性能,硬度等等。同時提升所制備粉末的純度也是一個重要的發(fā)展方向;其次是燒結(jié)工藝的改進,目前新型燒結(jié)工藝主要的問題還是在于到達所需致密度的燒結(jié)條件較為苛刻,而致密度又嚴(yán)重影響著其磁控濺射薄膜的連續(xù)性;最后,計算模擬和智能制造技術(shù)的應(yīng)用,將進一步提高鎢基合金靶材的生產(chǎn)效率和產(chǎn)品一致性。通過計算機仿真技術(shù),可以優(yōu)化工藝參數(shù)和產(chǎn)品設(shè)計,縮短研發(fā)周期;通過智能制造系統(tǒng),可以實現(xiàn)生產(chǎn)過程的實時監(jiān)控和調(diào)控,提高生產(chǎn)的自動化和精確度。
4、結(jié)語
本文論述了近年來鎢基合金靶材主要的以及新興的制備方法,并從其磁控濺射薄膜的性能出發(fā)介紹了其幾種主要的應(yīng)用領(lǐng)域。相信在未來,隨著超純粉體生產(chǎn)能力的提升和靶材制備工藝和設(shè)備的升級,粉末冶金法制備的鎢基合金濺射靶材的純度、致密度和性能將持續(xù)提高,在電子器件、硬質(zhì)涂層等領(lǐng)域的應(yīng)用前景將更加廣闊。
參考文獻
[1] GUDMUNDSSON J T. Plasma Sources Science and Technology, 2020, 29(11).
[2] CHELVANATHAN P, SHAHAHMADI S A, ARITH F, et al. Thin Solid Films, 2017. DOI:10.1016/j.tsf.2017.07.057
[3] REZA M, SAJURI Z, YUNAS J, et al. IOP Conference Series: Materials Science and Engineering, 2016. DOI: 10.1088/1757-899x/114/1/012116
[4] WANG Q X, LIANG S H. Vacuum, 2011.85(11), 979
[5] KIM S, KWON T, KIM S, et al. International Journal of Refractory Metals and Hard Materials,2024, 118.
[6] IVANOV E, DEL RIO E. International Journal of Refractory Metals and Hard Materials, 2018,72: 223-7.
[7] GELLERUP S, ARNOLD C L, CAIRNS E, et al. Vacuum, 2023, 213.
[8] AI Y-P. Chemical Physics Letters, 2017, 690: 1-4.
[9] AMIRJAN M, ZANGENEH-MADAR K, PARVIN N. EInternational Journal of Refractory Metals and Hard Materials, 2009, 27(4): 729-33.
[10] LI Z-B, ZHANG H, ZHANG G-H, et al. Metallurgical and Materials Transactions A, 2022,53(3): 1085-98.
[11] GERMAIN F S, SLOSARIK S E. JOM, 1962. DOI: 10.1007/bf03378159
[12] Manikandan R, Raja Annamalai A. Materials Today Communications, 2024,39.
[13] Huang Z M,Wang D Z,Wu Z Z, et al. Powder Metallurgy Technology,2021 39(05): 445-51. (in Chinese)
黃志民, 王德志, 吳壯志, et al. 粉末冶金技術(shù) . 2021, 39(05): 445-51.
[14] DUNLOP J A, RENSING H. U.S. patent application, US4838935,1989.
[15] WANG Y M, TANG Q H, ZHOU P. Journal of Materials Engineering and Performance, 2021,30(10): 7223-35.
[16] XU L, SRINIVASAKANNAN C, ZHANG L, et al. Journal of Alloys and Compounds,2016,658,23.
[17] MA K, CAO X, YANG H, et al. Ceramics International, 2017,43(12),8551.
[18] BYUN J M, LEE E S, HEO Y J, et al. International Journal of Refractory Metals & Hard Materials, 2021,99, 105602.
[19] WICKERSHAM C E, POOLE J E, MUELLER J J. Journal of Vacuum Science & Technology A: Vacuum, Surfaces, and Films, 1992, 10(4): 1713-7.
[20] HU B, CAI G. Materials, 2022, 15(23), 8647.
[21] LI X, WANG Q, WEI S, et al. Journal of Alloys and Compounds, 2023, 975, 172571.
[22] DINE S, BERNARD E, HERLIN BOIME N, et al. Advanced Engineering Materials,2018,20(8), 1701138
[23] WANG Y, TANG Q, CHEN D, et al. Journal of Thermal Spray Technology, 2019, DOI:10.1007/s11666-019-00958-x.
[24] HAO Y, TAN C, YU X, et al. Journal of Alloys and Compounds, 2020, 819, 152975.
[25] MüLLER A V, DOROW-GERSPACH D, BALDEN M, et al. Journal of Nuclear Materials,2022.
[26] TALIGNANI A, SEEDE R, WHITT A, et al. Additive Manufacturing, 2022,566.
[27] KIM J Y, LEE E S, HEO Y J, et al. Powder Metallurgy, 2023,66 (5) , 644
[28] WANG Y, TANG Q, CHEN D, et al. International Journal of Refractory Metals & Hard Materials, 2019,87.
[29] ENGWALL A M, SHIN S J, BAE J, et al. Surface & Coatings Technology, 2019,363,191.
[30] PAULEAU Y. Thin Solid Films, 1984, DOI: 10.1016/0040-6090(84)90051-8
[31] BHAGAT S, HAN H, ALFORD T L. Thin Solid Films, 2006, 515 (4) , 1998
[32] LO C-F, GILMAN P. Journal of Vacuum Science & Technology A: Vacuum, Surfaces, and Films, 1999, 17(2): 608-10.
[33] GUIDI V, BOSCARINO D, COMINI E, et al. Sensors and Actuators B: Chemical, 2000, 65(1):264-6.
[34] SU Y-H, KUO T-C, LEE W-H, et al. Microelectronic Engineering, 2017, 171: 25-30.
[35] LAZARIDES N, TSIRONIS G P. Physics Reports, 2018, 87 (3).
[36] SUZUKI M, KOBAYASHI N, MUKAI K, et al. Journal of The Electrochemical Society ,1990,137(10): 3213.
[37] KONDO S. Journal of Materials Research, 1992. DOI: 10.1557/jmr.1992.0853
[38] NISHINO N. Carbon, 1997. DOI: 10.1016/s0008-6223(97)82814-x
[39] ZHANG W, QI Y, ZHANG L, et al. Surface and Coatings Technology, 2022, 434.
[40] PERO R, MAIZZA G, MONTANARI R, et al. Materials, 2020,13 (9).
[41] ZHOU Z, XU Y, CHEN X, et al. Ceramics International, 2020,46 (4) , 4095.
[42] YUMASHEV A, MIKHAYLOV A J P C. Polymer Composites, 2020, 41(7): 2875.
[43] CHRZANOWSKA J, KURPASKA ?, GI? Y?SKI M, et al. Ceramics International, 2016,42 (10) , 12221.
[44] CHRZANOWSKA-GI? Y?SKA J, DENIS P, WO? NIACKA S, et al. Ceramics International,2018,44 (16) , 19603.
[45] JIANG C, PEI Z, LIU Y, et al. Physica Status Solidi (A) - Applications and Materials Science,2013,210 (6) , 1221.
[46] RADZIEJEWSKA J, PSIUK R, MO? CICKI T. Coatings, 2020, 10(12).
[47] MAHJABIN S, HAQUE M M, BASHAR M S, et al. Energy & Fuels, 2023, 37( 24), 19860.
[48] YU H, YANG X, XIAO X, et al. Advanced Materials, 2018, 30 (51).
[49] ? ERVENá M, ? ERSTVy R, DVO? áK T, et al. Journal of Alloys and Compounds, 2021, 888.
[50] SADOVSKIY Y, BEGRAMBEKOV L, AYRAPETOV A, et al. Journal of Physics: Conference Series, 2016, 748.
[51] EUCHNER H, MAYRHOFER P H, RIEDL H, et al. Acta Materialia, 2015, 101 , 55.
[52] SMOLIK J, KACPRZY?SKA-GO?ACKA J, SOWA S, et al. Coatings, 2020, 10 (9).
[53] LOURO C, CAVALEIRO A. Journal of The Electrochemical Society, 1997, DOI:10.1149/1.1837394.
[54] SERDOBINTSEV A A, STARODUBOV A V, KOZHEVNIKOV I O, et al. Journal of Physics:Conference Series, 2020, 1697(1).
李銳,2023 年 9 月于昆明理工大學(xué)獲得工學(xué)學(xué)士學(xué)位?,F(xiàn)為昆明理工大學(xué)材料科學(xué)與工程學(xué)院碩士研究生,在劉意春教授的指導(dǎo)下進行研究。目前主要研究領(lǐng)域為金屬靶材及表面工程。
趙琪,昆明貴金屬研究所助理研究員。2022 年中南大學(xué)材料科學(xué)與工程專業(yè)博士畢業(yè),2022 年博士畢業(yè)后到貴金屬研究所工作至今。目前主要從事金屬靶材和金屬基
復(fù)合材料等方面的研究工作。發(fā)表論文 20 余篇,包括 Materials Science and Engineering: A , Journal of Alloys and Compounds, Diamond and Related Materials,Journal of Materials Research and Technology 以及 Applied Surface Science 等。
劉意春,昆明理工大學(xué)材料科學(xué)與工程學(xué)院教授、博士研究生導(dǎo)師。2001 年 7 月上海交通大學(xué)材料科學(xué)與工程專業(yè)本科畢業(yè),2011 年上海交通大學(xué)材料學(xué)專業(yè)博士畢業(yè)后到昆明理工大學(xué)工作至今。目前主要從事粉末冶金和金屬基復(fù)合材料等方面的研究工作。發(fā)表論文 100 余篇,包括 Materials Science and Engineering: A , Materials Characterization, Diamond and Related Materials, Journal of Materials Research andTechnology 等。
無相關(guān)信息