鈦合金具有密度小、強(qiáng)度高、比強(qiáng)度大、無磁性、導(dǎo)熱率小、彈性模量、抗阻尼性能低等特點(diǎn),廣泛應(yīng)用于航空航天、汽車、船舶、化工等領(lǐng)域。其中TC4鈦合金的應(yīng)用較為
廣泛。TC4鈦合金是一種典型的(α+β) 兩相鈦合金,它具有較高的蠕變抗力和持久強(qiáng)度以及良好的熱穩(wěn)定性和耐沖刷腐蝕性能,能耐高溫300℃的含鹽與酸性的流體的腐蝕,
比強(qiáng)度高,焊接性能良好,結(jié)構(gòu)效益高,耐久性和損傷容限高,綜合性能優(yōu)異[1]。
TC4鈦合金管材的使用日趨迫切并已成為未來趨勢。國外在Ti-6Al-4V 合金的基礎(chǔ)上進(jìn)行了多種成分調(diào)整發(fā)展出的如GR5、GR23、GR29 等鈦合金已運(yùn)用于實(shí)際生產(chǎn)制造。
國內(nèi)也早于20 世紀(jì)90 年代開展TC4鈦合金的成分適應(yīng)性的調(diào)整及相關(guān)規(guī)格無縫管材的工藝試制工作。鈦合金管材加工由于材料壓力加工范圍窄、變形抗力高等原因?qū)е鹿ば驈?fù)
雜、生產(chǎn)周期長、加工難度大、成品率低。TC4鈦合金管材的生產(chǎn)多以熱擠壓制坯的方法為主,技術(shù)相對成熟,成品規(guī)格多,后續(xù)多采用溫軋或機(jī)加工兩種方式進(jìn)行深加工以針對
不同的性能需求。也可采用斜軋穿孔法制備管坯,但其性能相較于熱擠壓法較低。
本文主要以擠壓制坯為主線對“擠壓+ 溫軋”和“擠壓+ 機(jī)加”兩種后續(xù)的加工工藝路線試制TC4鈦合金無縫管材進(jìn)行了對比研究。通過研究對比其金相組織、力學(xué)性能和表面質(zhì)量的差異,為后續(xù)的TC4鈦合金無縫管材加工生產(chǎn)制造提供參考。
1、材料及方法
1.1 材料
所用鑄錠采用真空自耗電弧爐二次熔煉,并經(jīng)過多次鍛造開坯,機(jī)加工得到Φ210mm 的錠坯,其化學(xué)成分(質(zhì)量分?jǐn)?shù),%)為:Al :5.5~6.75,V :3.5~4.5,F(xiàn)e ≤ 0.03,O :0.20,H ≤ 0.0 1 5 , N ≤ 0.0 5 , C ≤ 0.0 8 , T i 余量, 滿足G B /T3620.1-2007要求。金相法測得相變點(diǎn)995℃。
1.2 方法
1.2.1 制定的兩種工藝路線
工藝1(擠壓+ 溫軋):3150t 臥式擠壓機(jī)擠壓管坯→溫矯直→酸洗→化涂→溫軋→除油→酸洗→真空退火→矯直→平頭→拋光→酸洗→無損檢測→清潔→成品檢查→包裝→入庫。
工藝2(擠壓+ 機(jī)加):3150t 臥式擠壓機(jī)擠壓管坯→溫矯直→熱處理→三點(diǎn)壓力矯直→機(jī)加→酸洗→無損檢測→清潔→成品檢查→包裝→入庫。
溫軋過程中的管坯加熱溫度及過程溫度控制非常重要,要求軋制過程的溫度要均衡平穩(wěn),不得忽高忽低,對設(shè)備的結(jié)構(gòu)及功能穩(wěn)定性要求較高。
目前多以兩輥軋機(jī)為主要平臺(tái)進(jìn)行溫軋,芯頭采用硬質(zhì)合金鋼。機(jī)加應(yīng)保證工藝設(shè)計(jì)的機(jī)加余量足夠,對坯料平直度、幾何尺寸一致性及表面質(zhì)量等要求較高,需要在機(jī)加前進(jìn)行三點(diǎn)壓力矯直管坯的直線度,以滿足車削加工的精度。熱處理采用大氣爐空冷。真空退火要求退火爐真空度≤ 0.1Pa,隨爐冷卻至室溫[2]。
在3150t 臥式擠壓機(jī)上熱擠壓得到的TC4鈦合金無縫管實(shí)物如圖1. 所示。分別對兩種工藝路線試制得到的管材進(jìn)行取樣,對比分析金相組織、力學(xué)性能的差異性。目視檢查對比其表面質(zhì)量。
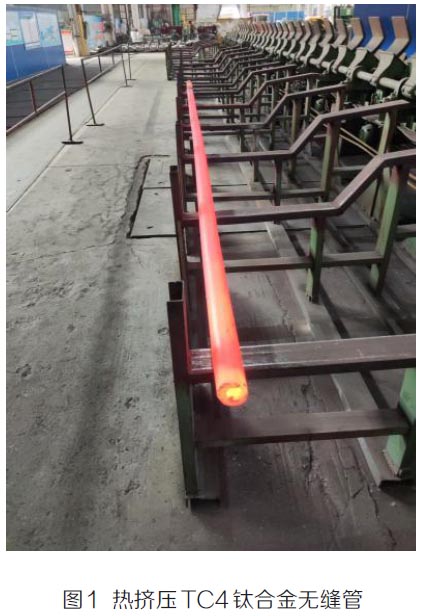
1.2.2 取樣
對工藝1 路線管坯擠壓態(tài)(R)取樣,試樣編號(hào):1-1、1-2 ;對工藝2 路線管坯擠壓態(tài)(R)取樣,試樣編號(hào):1-3、1-4 ;對工藝1 路線管材退火態(tài)(M)取樣,試樣編號(hào):2-1、2-2 ;對工藝2 路線管材退火態(tài)(M)取樣,試樣編號(hào):3-1、3-2。取樣位置為管材頭部200mm 處。
分別取8mm×8mm×80mm 縱向方棒樣,隨后機(jī)加至Φ5×80mm 的圓棒樣,在TC-12-066 拉伸機(jī)上進(jìn)行室溫拉伸性能測試。
對擠壓態(tài)(R)和兩種工藝路線得到的管材的退火態(tài)(M)的金相試樣進(jìn)行磨制、拋光,采用酸性溶液腐蝕后,拍攝試樣橫向高倍金相照片,照片精度為50μm。
2、結(jié)果與分析
2.1 金相組織和力學(xué)性能的對比
2.1.1 金相組織
熱擠壓得到的TC4鈦合金無縫管金相組織為典型(α+β) 兩相區(qū)組織,如圖2 所示,其組織形貌兼有網(wǎng)籃組織和魏氏組織。
在片層α 相組織區(qū)域邊緣存在著轉(zhuǎn)變?chǔ)?相,β 晶粒粗大,無等軸α,有針狀α 和條狀α,有晶界α 和大塊α,見圖2a)。工藝1 得到的管材的金相組織見圖2c),進(jìn)行溫軋,得到的組織更加細(xì)密均勻。工藝2 得到的管材的金相組織見圖2d),在機(jī)加退火后,組織形貌基本延續(xù)了擠壓態(tài),組織均勻化有一定有限的提升,晶粒略有長大,晶內(nèi)部分長條形α 相變厚,晶界上的α 相也開始粗化。
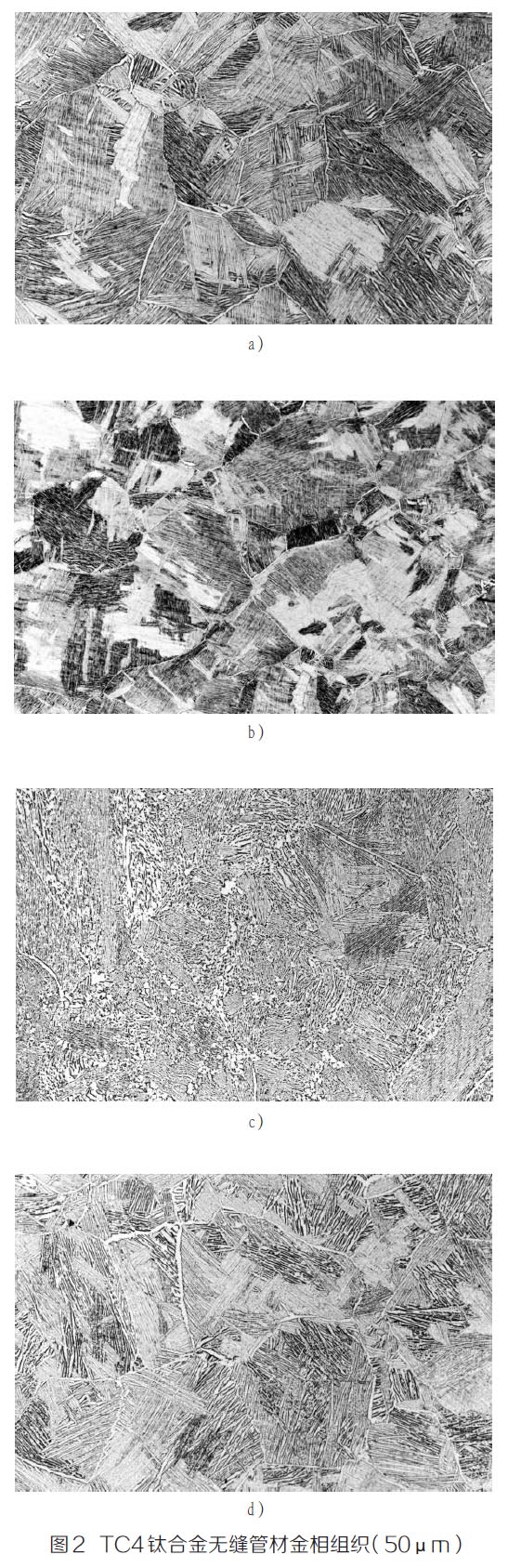
2.1.2 力學(xué)性能
由表1 可見,擠壓法生產(chǎn)的TC4鈦合金無縫管材擁有良好的室溫力學(xué)性能。工藝1 相較于工藝2,抗拉強(qiáng)度Rm 和屈服強(qiáng)度Rρ0.2 均略高,延伸率較高。整體力學(xué)性能上進(jìn)行比較,工藝1 制備的TC4鈦合金無縫管材的綜合力學(xué)性能更加優(yōu)異,這與組織形貌的顯示相匹配。
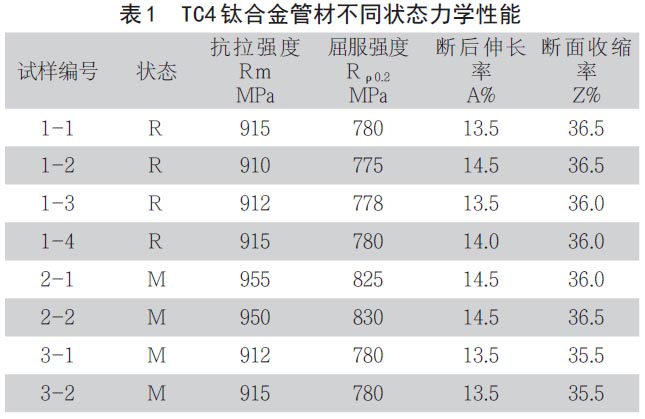
2.2 表面質(zhì)量的對比
采用熱擠壓法在3150t 擠壓機(jī)平臺(tái)上得到的TC4 管坯長度一般為8m。頭部300mm 位置的外表面有規(guī)律性的折疊和凹坑不平缺陷,呈環(huán)形周向分布,如圖3 所示。頭部300mm 以后外表面再無缺陷。這是由于錠坯端面直角位置在加熱及變形過程中容易熱集中,坯料內(nèi)外金屬塑性不均,且處于劇烈變化的位置,同一截面上金屬流速非常不均勻所導(dǎo)致。尾部200mm 位置的內(nèi)表面有輕微折疊缺陷,這是由于變形即將結(jié)束的尾部內(nèi)表面潤滑劑由于消耗損失導(dǎo)致潤滑能力下降,摩擦熱增大,內(nèi)表面金屬在個(gè)別位面上的塑性差異,以及金屬粘結(jié)剝離摩擦導(dǎo)致。管坯頭尾的缺陷并不會(huì)影響到后續(xù)管材的過程質(zhì)量穩(wěn)定性,可在后續(xù)工序上通過機(jī)加修磨等形式予以消除。
工藝1 和工藝2 制備得到的TC4鈦合金無縫管材的表面質(zhì)量優(yōu)異,表面粗糙度均能達(dá)到3.2 以下,無明顯差別,遠(yuǎn)高于指標(biāo)要求。但工藝1 在實(shí)際生產(chǎn)過程中工序較長,過程控制難點(diǎn)較多,過程穩(wěn)定性較低,個(gè)別工序的加工難度較大。
工藝2 造成的材料損失較大,機(jī)加工后的金屬屑基本無有效用途,材料成本較高,生產(chǎn)同樣長度的成品管材需要較長的擠壓錠坯,或者調(diào)整擠壓管坯的規(guī)格才能減少機(jī)加損失。
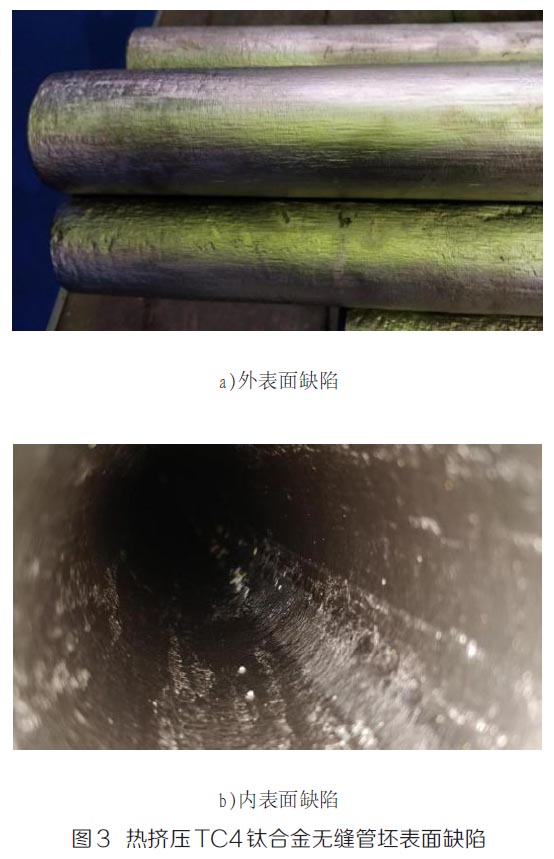
3、結(jié)論
(1)熱擠壓TC4鈦合金無縫管材的組織形貌兼有網(wǎng)籃組織和魏氏組織。工藝1 相較于工藝2 得到的組織更加細(xì)密均勻。
(2)工藝1 相較于工藝2,抗拉強(qiáng)度和屈服強(qiáng)度均略高。整體力學(xué)性能上比較,工藝1 制備的TC4鈦合金無縫管材更為優(yōu)異。
(3)工藝1 和工藝2 制備的管材表面質(zhì)量均優(yōu)異。工藝1 在實(shí)際生產(chǎn)過程中穩(wěn)定性較低,過程控制難點(diǎn)多,加工難度較大。工藝2 造成的材料損失較大,材料成本較高,生產(chǎn)
同樣長度的成品管材需要較長的擠壓錠坯。
參考文獻(xiàn):
[1] 李寶霞, 李紅博, 趙富強(qiáng), 等. 大規(guī)格TC4 無縫管材工藝研究[J]. 有色金屬加工,2018,47(5):47-49.
[2] 顏孟奇, 張業(yè)勤, 齊立春, 黃利軍, 李煥峰.TC4鈦合金冷軋無縫管材的制備工藝及織構(gòu)演變規(guī)律研究[J]. 材料開發(fā)與應(yīng)用,2020,35(05):63-68.
相關(guān)鏈接